Ceramic coating is also commonly referred to as nano-coating or glass coating. These terms are often used interchangeably in the automotive and industrial sectors to describe a liquid polymer that chemically bonds with the surface of a vehicle or object, providing a durable, protective layer. Ceramic coatings are known for their hydrophobic properties, UV resistance, and ability to enhance the appearance of surfaces. While "ceramic coating" is the most widely recognized term, "nano-coating" emphasizes the nanotechnology used in its formulation, and "glass coating" highlights the glossy, glass-like finish it provides.
Key Points Explained:
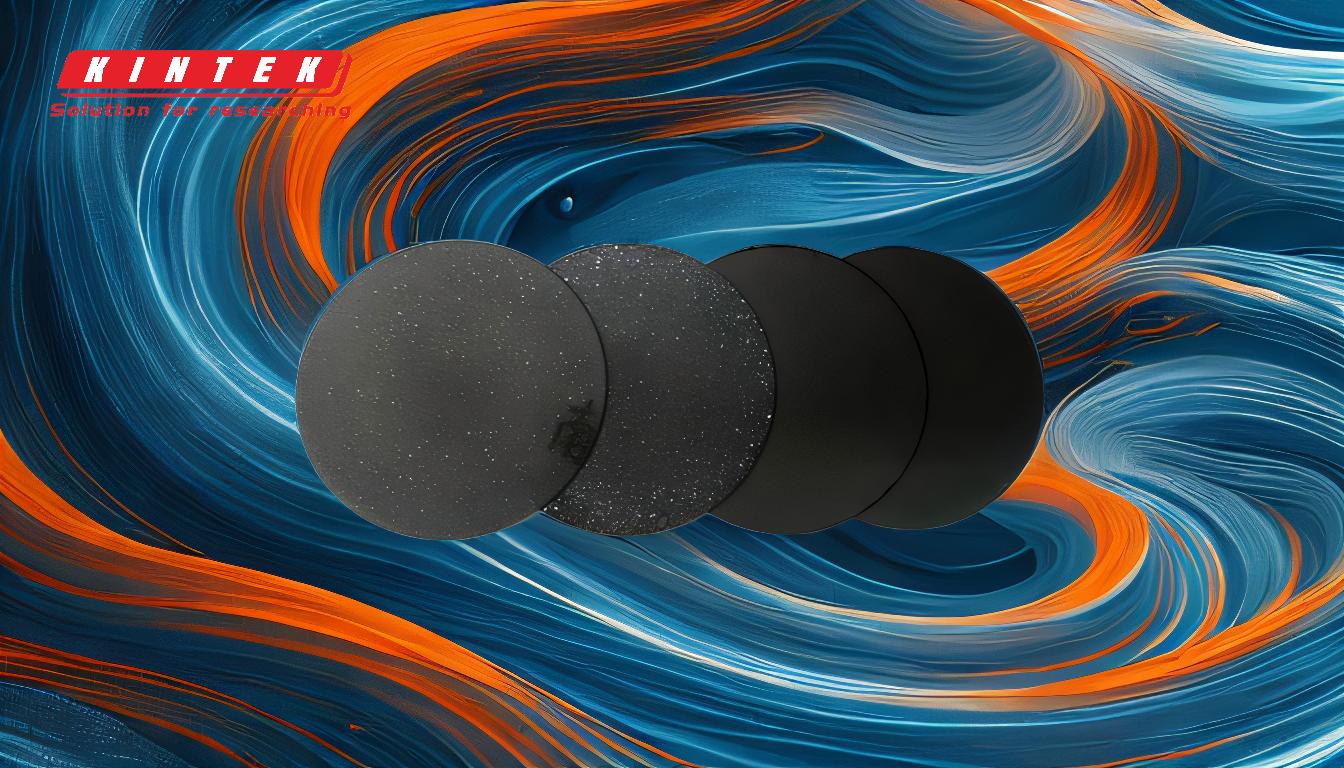
-
Ceramic Coating as Nano-Coating:
- The term "nano-coating" refers to the use of nanotechnology in the formulation of ceramic coatings. These coatings contain nanoparticles that fill in microscopic imperfections on the surface, creating a smooth and durable layer.
- Nano-coatings are known for their ability to repel water, dirt, and contaminants due to their hydrophobic properties.
- This term is often used in industries where precision and advanced technology are emphasized, such as automotive detailing and industrial applications.
-
Ceramic Coating as Glass Coating:
- "Glass coating" is another name for ceramic coating, highlighting the glossy, glass-like finish it provides. This term is particularly popular in the automotive industry, where the coating enhances the shine and clarity of a vehicle's paint.
- Glass coatings are valued for their ability to protect surfaces from UV rays, oxidation, and environmental contaminants while maintaining a high-gloss appearance.
- This term is often used in marketing to emphasize the aesthetic benefits of ceramic coatings.
-
Interchangeability of Terms:
- While "ceramic coating" is the most commonly used term, "nano-coating" and "glass coating" are often used interchangeably depending on the context and the specific benefits being highlighted.
- The choice of terminology may vary by region, industry, or marketing strategy, but all three terms refer to the same type of protective coating.
-
Benefits of Ceramic Coatings:
- Durability: Ceramic coatings provide long-lasting protection compared to traditional waxes or sealants.
- Hydrophobic Properties: The coating repels water, making it easier to clean and maintain surfaces.
- UV Resistance: Protects surfaces from fading and damage caused by ultraviolet rays.
- Enhanced Appearance: Provides a glossy, reflective finish that enhances the visual appeal of surfaces.
-
Applications of Ceramic Coatings:
- Automotive: Used to protect car paint, wheels, and glass from environmental damage and to maintain a showroom finish.
- Marine: Applied to boats and yachts to protect against saltwater corrosion and UV damage.
- Industrial: Used on machinery, equipment, and structures to provide a protective barrier against wear and tear.
- Consumer Electronics: Applied to screens and surfaces to prevent scratches and smudges.
By understanding these key points, a purchaser can make informed decisions about the type of coating that best suits their needs, whether they prioritize durability, aesthetics, or advanced technology.
Summary Table:
Aspect | Details |
---|---|
Terminology | Ceramic coating, nano-coating, glass coating (used interchangeably) |
Key Features | Hydrophobic, UV-resistant, durable, glossy finish |
Applications | Automotive, marine, industrial, consumer electronics |
Benefits | Long-lasting protection, easy cleaning, enhanced appearance |
Technology | Nanotechnology for precision and durability |
Ready to protect your surfaces with ceramic coating? Contact us today for expert advice!