Ash content in coal refers to the inorganic, non-combustible residue left after coal is completely burned. It is a critical parameter in assessing the quality and usability of coal, as it directly impacts combustion efficiency, handling, and environmental considerations. The ash content is typically expressed as a percentage of the total weight of the coal sample and consists of mineral oxides and other inorganic compounds. Understanding ash content is essential for industries relying on coal for energy, as it influences factors such as heating value, slagging, fouling, and emissions. While the provided references focus on ash content in food, the principles apply similarly to coal, emphasizing the importance of inorganic material measurement in quality assessment.
Key Points Explained:
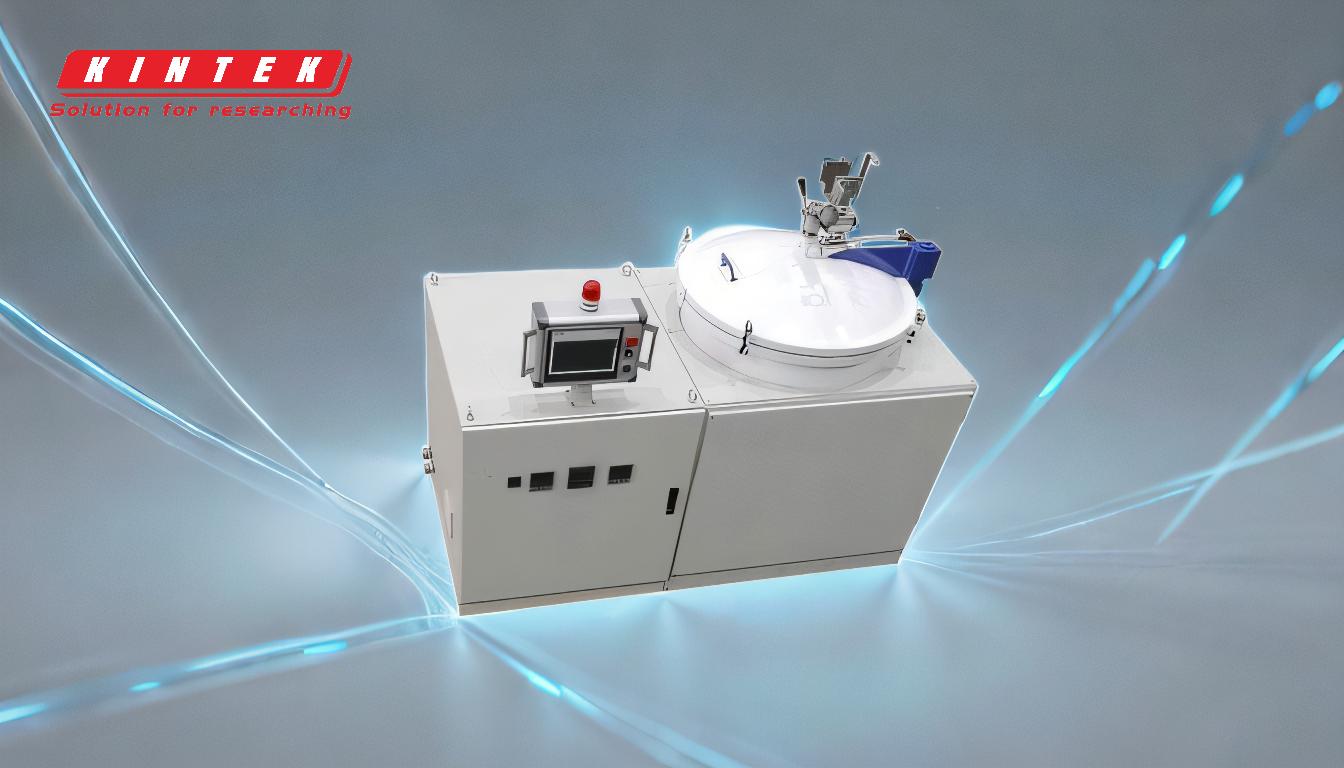
-
Definition of Ash Content in Coal
- Ash content in coal is the inorganic, non-combustible material that remains after coal is completely burned.
- It primarily consists of oxides of inorganic elements such as silica, alumina, iron, calcium, and magnesium.
- The ash content is expressed as a percentage of the total weight of the coal sample.
-
Significance of Ash Content in Coal
- Combustion Efficiency: Higher ash content reduces the effective heating value of coal, as the inorganic material does not contribute to energy production.
- Handling and Transportation: Coal with high ash content requires more effort and cost to transport and handle due to the increased weight of non-combustible material.
- Environmental Impact: Ash content influences emissions, as it can lead to the release of particulate matter and other pollutants during combustion.
- Operational Challenges: High ash content can cause slagging and fouling in boilers, reducing efficiency and increasing maintenance costs.
-
Measurement of Ash Content
- Ash content is determined by burning a coal sample at high temperatures (typically around 750°C to 800°C) until all combustible material is oxidized.
- The remaining residue is weighed, and the ash content is calculated as a percentage of the original sample weight.
- This process is standardized by organizations such as ASTM International and ISO to ensure consistency and accuracy.
-
Factors Influencing Ash Content
- Geological Origin: The mineral composition of the coal-forming environment affects the type and amount of ash content.
- Mining and Processing: Mechanical processes during mining and washing can influence the ash content by removing or adding inorganic material.
- Coal Rank: Different ranks of coal (e.g., lignite, bituminous, anthracite) have varying ash content due to differences in their formation processes.
-
Practical Implications for Coal Purchasers
- Cost-Effectiveness: Purchasers should consider the ash content when evaluating the cost-effectiveness of coal, as higher ash content reduces the usable energy per ton.
- Environmental Compliance: Lower ash content coal is often preferred to meet stricter environmental regulations and reduce emissions.
- Operational Efficiency: Selecting coal with appropriate ash content can minimize operational challenges and maintenance costs in combustion systems.
-
Comparison with Ash Content in Food
- While the provided references focus on ash content in food, the concept is analogous to coal. In both cases, ash content measures inorganic, non-combustible material.
- However, the acceptable ash content varies significantly between coal and food. For example, food products typically aim for an ash content of around 5%, whereas coal ash content can range from 5% to 40% or more, depending on the type and quality of coal.
-
Industry Standards and Testing Methods
- Standardized methods for ash content determination ensure consistency and reliability across industries.
- Common standards include ASTM D3174 for coal and ISO 1171 for solid fuels.
- These methods involve precise procedures for sample preparation, combustion, and residue analysis to ensure accurate results.
-
Future Trends and Considerations
- Advances in coal cleaning technologies aim to reduce ash content and improve the quality of coal for industrial use.
- Increasing environmental regulations are driving demand for low-ash coal to minimize emissions and improve sustainability.
- Research into alternative uses for coal ash, such as in construction materials, is gaining attention as a way to reduce waste and environmental impact.
By understanding ash content in coal, purchasers and users can make informed decisions about coal selection, ensuring optimal performance, cost-effectiveness, and compliance with environmental standards.
Summary Table:
Key Aspect | Details |
---|---|
Definition | Inorganic, non-combustible residue left after coal is burned. |
Composition | Oxides of silica, alumina, iron, calcium, and magnesium. |
Measurement | Expressed as a percentage of the total weight of the coal sample. |
Impact on Combustion | Higher ash content reduces heating value and increases operational costs. |
Environmental Concerns | Influences emissions, slagging, and fouling in boilers. |
Testing Standards | ASTM D3174 and ISO 1171 ensure accurate ash content measurement. |
Practical Implications | Lower ash content improves cost-effectiveness and environmental compliance. |
Need help selecting the right coal for your operations? Contact our experts today for tailored advice!