A controlled atmosphere furnace is a specialized heating device designed to create a specific gaseous environment within its chamber, which is essential for processes like heat treatment, brazing, sintering, and material research. It offers precise temperature control, a tightly sealed environment, and the ability to introduce protective or reactive gases to achieve desired material properties. These furnaces are widely used in industries and laboratories for applications such as chemical analysis, metal and ceramic processing, and heat treatment of small steel parts. Key advantages include energy efficiency, safety, and the ability to handle parts of various shapes and sizes.
Key Points Explained:
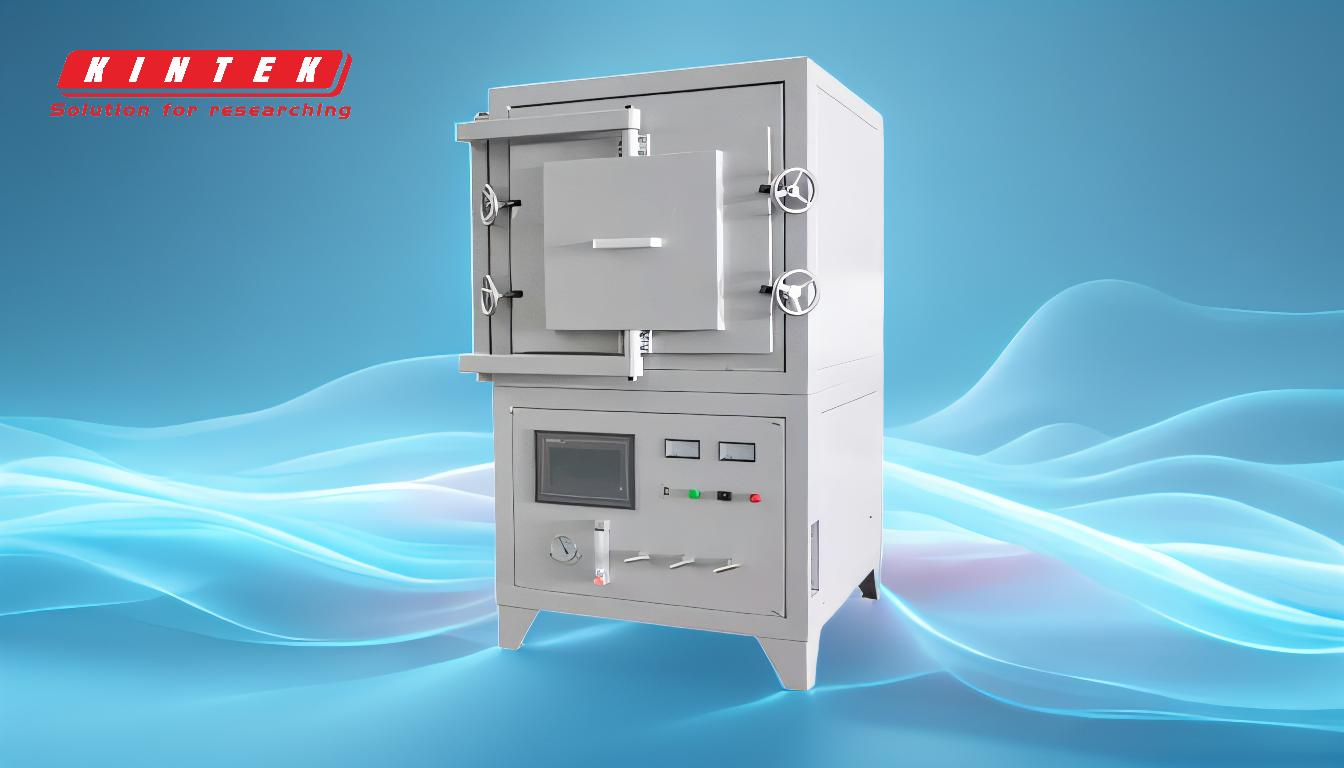
-
Definition and Purpose:
- A controlled atmosphere furnace is designed to maintain a specific gaseous environment within its chamber, which is crucial for processes like heat treatment, brazing, and sintering.
- It ensures that materials are processed under optimal conditions, free from contaminants like oxygen or moisture, which could otherwise alter the material properties.
-
Key Features:
- Tightly Sealed Chamber: The furnace must have a tightly sealed chamber or muffle to prevent external air infiltration, ensuring the integrity of the controlled atmosphere.
- Precise Temperature Control: Advanced controls allow for accurate adjustments of temperature, time, and pressure, which are critical for achieving consistent results.
- Safety Mechanisms: Safety devices are integrated to handle gaseous atmospheres, especially those that could form explosive mixtures.
-
Applications:
- Industrial Use: Widely used in industries for processes like aluminum brazing, sintering of metals and ceramics, and heat treatment of small steel parts.
- Laboratory Use: Suitable for chemical analysis, physical measurements, and research in academic and industrial laboratories.
-
Advantages:
- Energy Efficiency: These furnaces are designed to consume less energy while maintaining high performance, leading to reduced operating costs.
- Versatility: They can handle parts of all shapes and sizes, making them suitable for a wide range of applications.
- Thermal Homogeneity: Ensures uniform heating, which is critical for achieving consistent material properties.
- Differentiated Finish: The controlled environment allows for precise finishes, free from oxidation or contamination.
-
Environmental and Safety Considerations:
- Eco-Friendly: The ability to control the atmosphere reduces emissions and waste, making it an environmentally friendly option.
- Safe Operation: The integration of safety devices ensures safe handling of reactive or potentially hazardous gases.
-
Specific Use Cases:
- Aluminum Brazing: Controlled atmosphere brazing furnaces are particularly effective for aluminum brazing, providing optimal conditions for bonding without oxidation.
- Material Research: In laboratories, these furnaces are used for sintering, melting, and heat treatment of materials, ensuring accurate and repeatable results.
By combining precise control, safety, and versatility, controlled atmosphere furnaces are indispensable tools in both industrial and laboratory settings, enabling advanced material processing and research.
Summary Table:
Aspect | Details |
---|---|
Definition | Specialized heating device for creating specific gaseous environments. |
Key Features | Tightly sealed chamber, precise temperature control, safety mechanisms. |
Applications | Heat treatment, brazing, sintering, chemical analysis, material research. |
Advantages | Energy efficiency, versatility, thermal homogeneity, eco-friendly operation. |
Use Cases | Aluminum brazing, metal and ceramic processing, laboratory research. |
Ready to enhance your material processing? Contact us today to learn more about controlled atmosphere furnaces!