Atomic Layer Deposition (ALD) is a highly precise thin film deposition technique that operates through sequential, self-limiting chemical reactions on a substrate's surface. It involves the use of gas-phase precursors that are introduced alternately into a reaction chamber, where they form atomic layers through surface reactions. Each precursor reacts with the substrate or the previous layer to create a chemically bonded film, and the process repeats until the desired thickness is achieved. ALD is known for its exceptional control over film thickness, uniformity, and conformality, making it ideal for applications requiring high precision, such as semiconductor manufacturing, nanotechnology, and advanced coatings.
Key Points Explained:
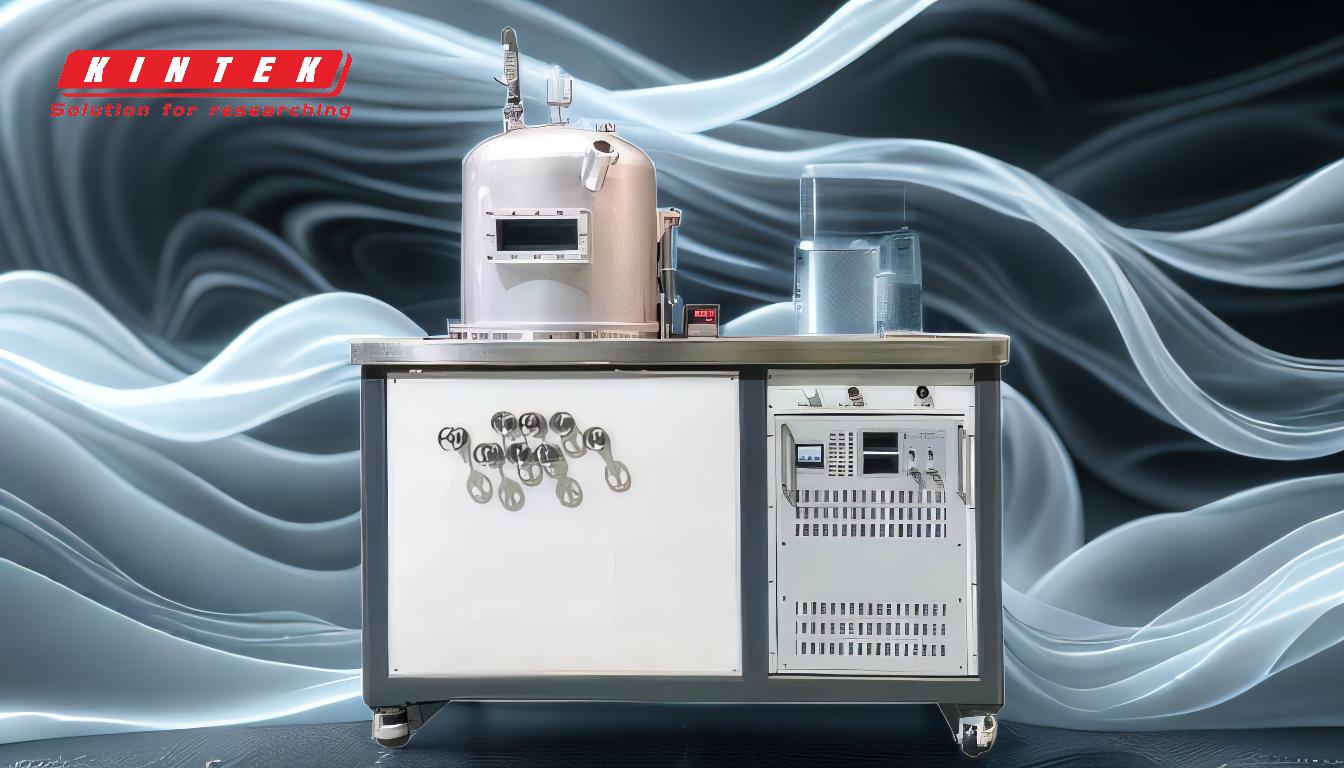
-
Definition and Purpose of ALD:
- ALD is a specialized form of Chemical Vapor Deposition (CVD) that enables the deposition of ultra-thin, uniform, and conformal films at the atomic level.
- It is used to create high-quality thin films with precise thickness control, often in applications like semiconductor devices, sensors, and optical coatings.
-
How ALD Works:
- ALD operates through a cyclic process involving two or more precursors (gaseous chemicals) that react sequentially on the substrate's surface.
- The process is self-limiting, meaning each reaction stops once the surface is fully saturated, ensuring atomic-level precision.
-
Steps in the ALD Process:
-
Step 1: Precursor Exposure:
- The first precursor is introduced into the chamber, where it chemically adsorbs onto the substrate surface, forming a monolayer.
-
Step 2: Purging:
- Excess precursor and by-products are removed from the chamber through evacuation and purging.
-
Step 3: Reactant Exposure:
- A second precursor (or reactant) is introduced, which reacts with the adsorbed monolayer to form a solid film.
-
Step 4: Purging Again:
- The chamber is purged again to remove any remaining reactants and by-products.
-
Step 5: Repetition:
- The cycle repeats until the desired film thickness is achieved.
-
Step 1: Precursor Exposure:
-
Key Characteristics of ALD:
-
Atomic-Level Precision:
- Each cycle deposits a layer that is typically just a few angstroms thick, allowing for nanometer-scale control over film thickness.
-
Conformality:
- ALD films are highly conformal, meaning they uniformly coat complex geometries, including high-aspect-ratio structures.
-
Pinhole-Free Layers:
- The self-limiting nature of the reactions ensures dense, defect-free films.
-
Versatility:
- ALD can deposit a wide range of materials, including oxides, nitrides, metals, and polymers.
-
Atomic-Level Precision:
-
Advantages of ALD:
-
Uniformity:
- Excellent thickness uniformity across large areas and complex surfaces.
-
Precision:
- Precise control over film thickness at the atomic level.
-
Scalability:
- Suitable for both small-scale research and large-scale industrial production.
-
Low Temperature:
- ALD can often be performed at relatively low temperatures, making it compatible with temperature-sensitive substrates.
-
Uniformity:
-
Applications of ALD:
-
Semiconductors:
- Used for gate oxides, high-k dielectrics, and diffusion barriers in microelectronics.
-
Energy Storage:
- Enhances the performance of batteries and supercapacitors by depositing thin, uniform coatings on electrodes.
-
Optics:
- Produces anti-reflective coatings, mirrors, and filters with precise optical properties.
-
Biomedical:
- Used to create biocompatible coatings on medical devices and implants.
-
Nanotechnology:
- Enables the fabrication of nanoscale devices and structures with atomic precision.
-
Semiconductors:
-
Gas-Phase Precursors in ALD:
- ALD relies on gas-phase precursors that are volatile and reactive.
- Common precursors include metal halides, organometallics, and reactive gases like water, ammonia, or ozone.
- The choice of precursors depends on the desired material and the specific application.
-
Challenges and Considerations:
-
Slow Deposition Rate:
- ALD is inherently slower than other deposition techniques due to its cyclic nature.
-
Precursor Compatibility:
- Precursors must be carefully selected to ensure proper reactivity and stability.
-
Cost:
- High-purity precursors and specialized equipment can make ALD expensive.
-
Slow Deposition Rate:
By understanding these key points, a purchaser of equipment or consumables for ALD can make informed decisions about the technology's suitability for their specific needs, whether for research, development, or industrial applications.
Summary Table:
Key Aspect | Details |
---|---|
Definition | A precise thin film deposition technique using sequential, self-limiting reactions. |
Process | Cyclic steps: precursor exposure, purging, reactant exposure, and repetition. |
Key Characteristics | Atomic-level precision, conformality, pinhole-free layers, and versatility. |
Advantages | Uniformity, precision, scalability, and low-temperature operation. |
Applications | Semiconductors, energy storage, optics, biomedical, and nanotechnology. |
Precursors | Gas-phase chemicals like metal halides, organometallics, and reactive gases. |
Challenges | Slow deposition rate, precursor compatibility, and high costs. |
Ready to explore ALD solutions for your industry? Contact our experts today to learn more!