A belt type furnace is a continuous heating system designed for industrial heat treatment processes. It uses a conveyor belt, often made of alloy or ceramic, to transport materials through a tunnel-shaped heating chamber. These furnaces are highly efficient for high-volume production, offering uniform temperature distribution, fast thermal responses, and the ability to integrate multiple heating processes into one continuous operation. They are commonly used for processes like hardening, annealing, carburizing, and sintering, and are particularly suited for small parts such as fasteners, screws, and nuts. Belt furnaces are known for their durability, low maintenance, and ability to operate under controlled atmospheres, making them a cost-effective solution for industrial heat treatment.
Key Points Explained:
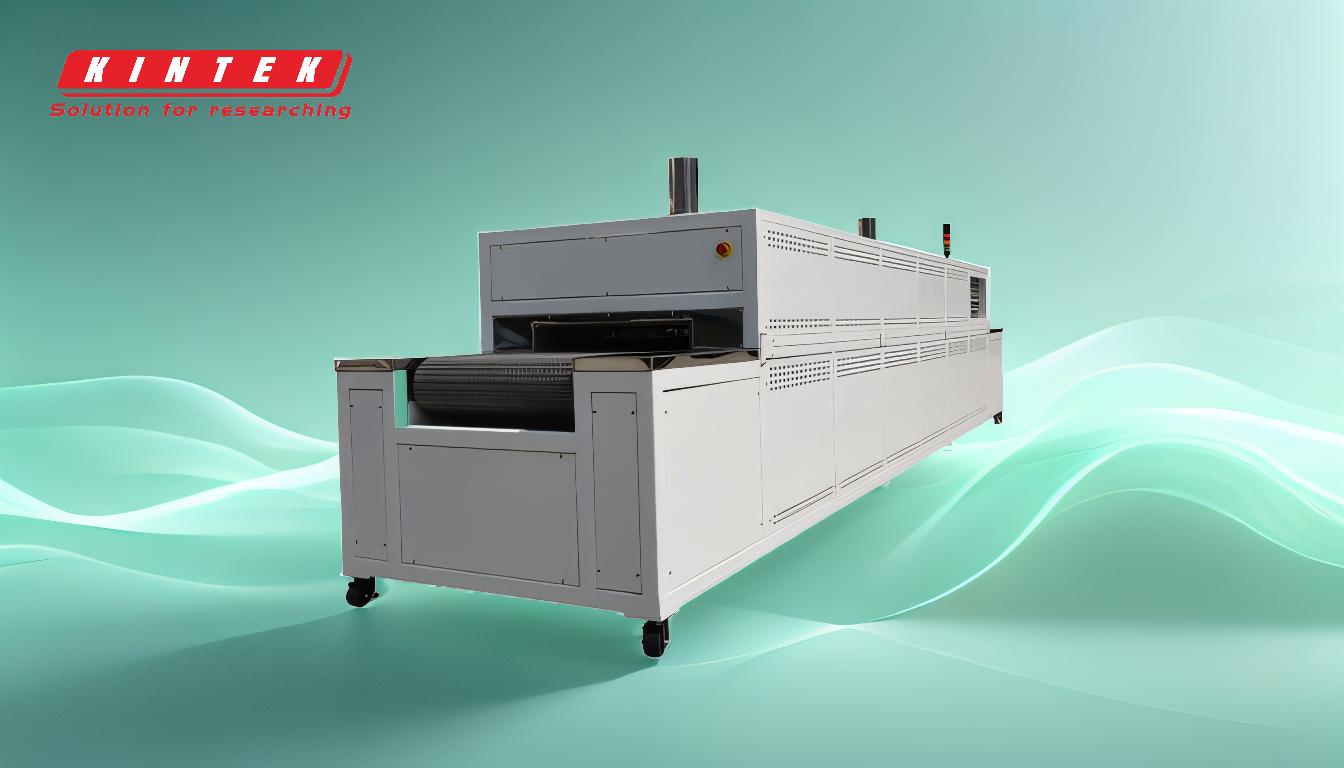
-
Definition and Structure of Belt Type Furnaces:
- Belt type furnaces are continuous heating systems that utilize a conveyor belt (alloy or ceramic) to move materials through a tunnel-shaped heating chamber.
- The furnace is divided into heating modules, allowing for precise control over temperature and process conditions.
-
Applications and Processes:
- These furnaces are ideal for high-volume heat treatment of small parts, such as screws, nuts, bolts, and other fasteners.
- Common processes include controlled atmosphere hardening, carbonitriding, carburizing, annealing, sintering, and tempering.
- They are particularly effective for processes requiring uniform temperature distribution and fast thermal responses.
-
Temperature Range and Heating Capabilities:
- Belt furnaces can operate at high temperatures, typically up to 2100°F (1150°C), making them suitable for a wide range of heat treatment applications.
- The tunnel-shaped heating chamber allows for consistent and stable temperature distribution across the entire process.
-
Advantages of Belt Type Furnaces:
- Continuous Operation: The conveyor belt system enables continuous processing, reducing downtime and increasing productivity.
- Gentle Handling: Mesh belt furnaces provide a "gentle approach" to prevent damage to delicate components during processing.
- Controlled Atmosphere: These furnaces can operate under controlled atmospheres, reducing the risk of contamination and oxidation.
- Durability and Low Maintenance: Belt furnaces are known for their extended lifespan and low monitoring needs, making them cost-effective for industrial use.
-
Comparison with Other Furnace Types:
- Bell Furnaces: Unlike batch-type bell furnaces, belt furnaces are continuous and better suited for high-volume production.
- Tube Furnaces: Tube furnaces are typically used for smaller, inorganic samples and are not designed for continuous processing like belt furnaces.
- Box Furnaces: Box furnaces are batch-type and require manual loading/unloading, whereas belt furnaces automate the process for higher efficiency.
-
Operational Considerations:
- Belt furnaces are designed to minimize the risk of mixing and contamination of components within the furnace.
- They are often equipped with multiple controlled zones, allowing for precise temperature regulation and process optimization.
- The use of a conveyor belt ensures consistent exposure of materials to heat, resulting in uniform treatment outcomes.
-
Industrial Suitability:
- Belt furnaces are particularly well-suited for industries requiring high-volume heat treatment, such as automotive, aerospace, and manufacturing.
- Their ability to handle small parts efficiently and maintain controlled atmospheres makes them indispensable for processes like carburizing and hardening.
In summary, belt type furnaces are a versatile and efficient solution for continuous heat treatment processes, offering precise temperature control, durability, and the ability to handle high-volume production with minimal maintenance. They are a preferred choice for industries requiring consistent and reliable heat treatment of small components.
Summary Table:
Feature | Details |
---|---|
Structure | Continuous heating system with a conveyor belt (alloy or ceramic) |
Temperature Range | Up to 2100°F (1150°C) |
Applications | Hardening, annealing, carburizing, sintering, and tempering |
Advantages | Continuous operation, gentle handling, controlled atmosphere, low maintenance |
Industrial Use | Automotive, aerospace, manufacturing |
Ready to optimize your heat treatment process? Contact us today to learn more about belt type furnaces!