Chemical vapor deposition (CVD) is a sophisticated technique used to deposit thin films of high-quality, high-performance materials onto substrates. This process involves exposing a substrate to gaseous precursors that decompose and react on the substrate's surface, forming a solid material layer. CVD is widely used in industries such as electronics, cutting tools, and solar cell manufacturing due to its ability to produce uniform, durable, and precise coatings. The process requires a high level of skill and specialized equipment, making it a critical method for creating advanced materials in modern technology.
Key Points Explained:
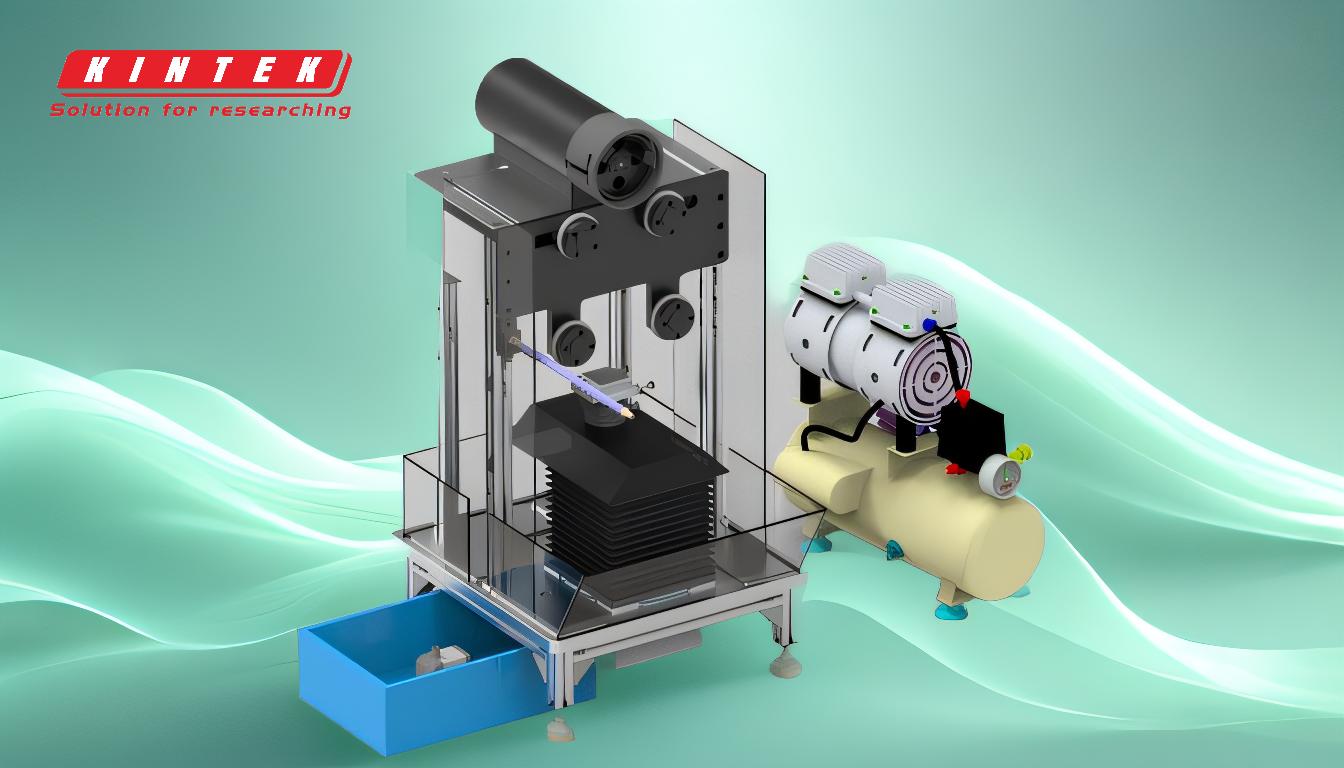
-
Definition of Chemical Vapor Deposition (CVD):
- CVD is a process where gaseous precursors are introduced into a reaction chamber containing a substrate. These precursors undergo chemical reactions on the substrate's surface, resulting in the deposition of a thin, solid film. This method is known for producing high-quality coatings with excellent uniformity and adhesion.
-
Applications of CVD:
- Electronics: CVD is essential in the electronics industry for depositing thin films on semiconductors, which are used in transistors, integrated circuits, and other microelectronic devices. It also forms conductive layers and insulating barriers in electrical components.
- Cutting Tools: CVD coatings are applied to cutting tools to enhance their durability, prevent corrosion, and reduce wear, extending their lifespan and improving performance.
- Solar Cells: In the renewable energy sector, CVD is used to deposit photovoltaic materials onto substrates, creating thin-film solar cells that are efficient and cost-effective.
-
Process Details:
- The substrate is placed in a reaction chamber, and the coating material is introduced in gaseous form. The gas reacts with the substrate or decomposes on its surface, forming the desired thin film. The process can be tailored by adjusting parameters such as temperature, pressure, and gas composition to achieve specific film properties.
-
Advantages of CVD:
- CVD produces films with high purity, excellent uniformity, and strong adhesion to the substrate. It is versatile and can be used to deposit a wide range of materials, including metals, ceramics, and semiconductors. Additionally, CVD can coat complex geometries and large surfaces efficiently.
-
Challenges and Skill Requirements:
- CVD requires precise control over process parameters and a deep understanding of chemical reactions. The equipment is complex and often expensive, necessitating skilled operators to achieve optimal results. Despite these challenges, the benefits of CVD make it a preferred method for many high-tech applications.
-
Comparison with Other Deposition Methods:
- Unlike physical vapor deposition (PVD), which uses physical processes like sputtering or evaporation to deposit materials, CVD relies on chemical reactions. This difference allows CVD to produce films with unique properties and better conformality on complex shapes. However, PVD is often faster and can be used for heat-sensitive materials.
-
Future Trends in CVD:
- Advances in CVD technology are focusing on reducing costs, improving deposition rates, and expanding the range of materials that can be deposited. Innovations such as plasma-enhanced CVD (PECVD) and atomic layer deposition (ALD) are pushing the boundaries of what is possible, enabling new applications in nanotechnology and flexible electronics.
In summary, chemical vapor deposition is a critical process for creating high-performance thin films in various industries. Its ability to produce precise, durable coatings makes it indispensable in fields ranging from electronics to renewable energy. While the process is complex and requires specialized skills, ongoing advancements continue to enhance its capabilities and broaden its applications.
Summary Table:
Aspect | Details |
---|---|
Definition | CVD deposits thin films via chemical reactions of gaseous precursors. |
Applications | Electronics, cutting tools, solar cells. |
Process | Gases react on substrate surfaces to form solid films. |
Advantages | High purity, uniformity, adhesion, and versatility. |
Challenges | Requires skilled operators and specialized equipment. |
Future Trends | Innovations like PECVD and ALD expanding applications. |
Discover how CVD can elevate your material coatings—contact our experts today!