Chemical vapor deposition (CVD) is a widely used method for synthesizing carbon nanotubes (CNTs) and other thin-film materials. It involves a series of chemical reactions in a vacuum environment, where gaseous precursors decompose or react on a substrate to form a solid film. For CNT fabrication, CVD is particularly advantageous due to its ability to control the structural properties of the nanotubes, such as diameter, length, and alignment. The process typically involves thermal treatments, gas-phase rearrangement, and catalyst deposition, making it cost-effective and environmentally manageable. By adjusting parameters like temperature, pressure, and gas flow rates, CVD can produce high-purity CNTs with tailored properties, making it a preferred method for industrial and research applications.
Key Points Explained:
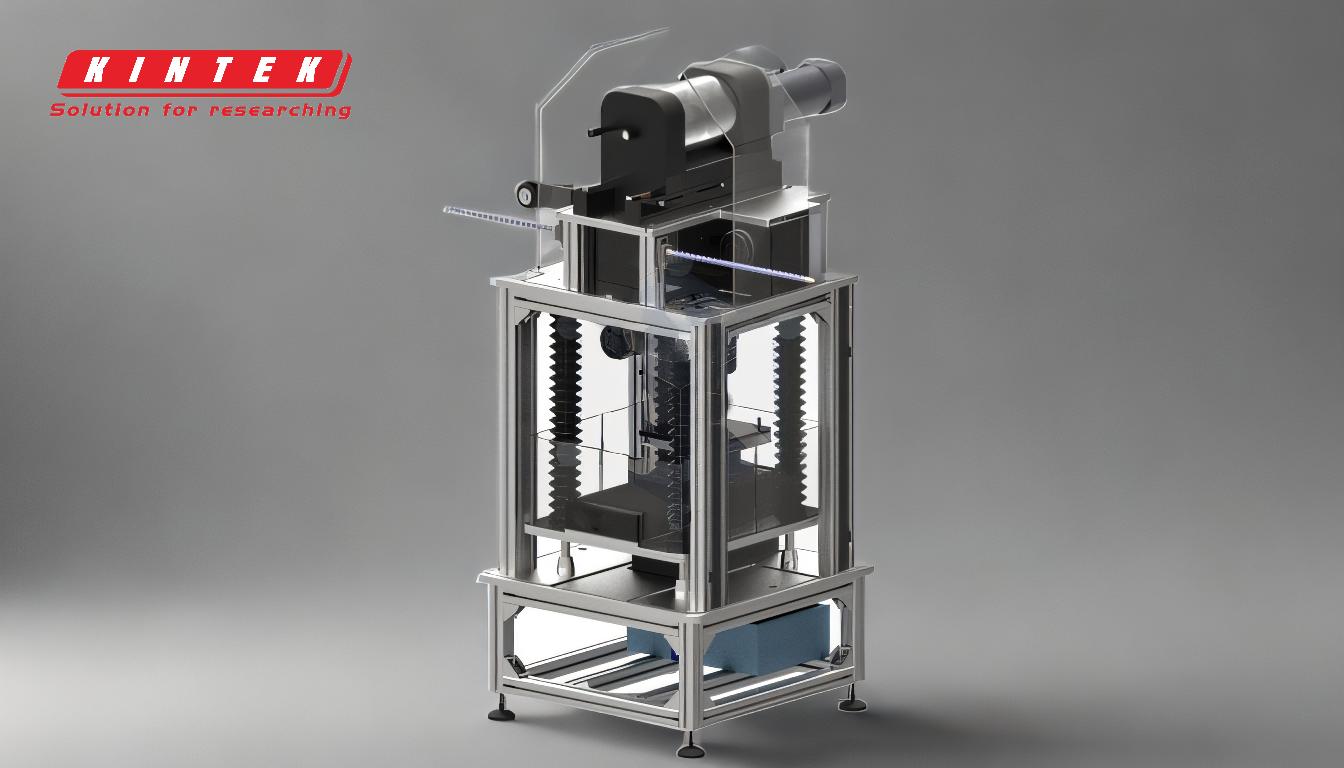
-
Overview of Chemical Vapor Deposition (CVD):
- CVD is a process where gaseous precursors undergo chemical reactions on a heated substrate to form a solid thin film.
- It is widely used for synthesizing carbon nanotubes (CNTs) due to its ability to control structural properties like diameter, length, and alignment.
-
Steps Involved in CVD for CNT Fabrication:
- Transport of Gaseous Species: Reacting gases are introduced into the vacuum chamber and transported to the substrate surface.
- Adsorption: The gaseous species adsorb onto the substrate surface.
- Surface Reactions: Heterogeneous surface-catalyzed reactions occur, leading to the decomposition or reaction of the gaseous species.
- Nucleation and Growth: The decomposed atoms or molecules form nucleation sites, leading to the growth of CNTs.
- Desorption and Removal: Gaseous by-products are desorbed and removed from the chamber.
-
Thermal Decomposition and Catalyst Role:
- In CNT synthesis, thermal treatments are used to decompose the gaseous precursors into carbon atoms.
- Catalysts, such as transition metals (e.g., iron, nickel, or cobalt), are often deposited on the substrate to facilitate the growth of CNTs by lowering the energy barrier for carbon atom rearrangement.
-
Advantages of CVD for CNT Synthesis:
- High Purity: CVD can produce high-purity CNTs with minimal impurities.
- Structural Control: Parameters like temperature, pressure, and gas flow rates can be adjusted to control the properties of the CNTs.
- Cost-Effectiveness: Catalytic chemical vapor deposition (CCVD) is particularly cost-effective for large-scale production.
- Environmental Impact: By optimizing material and energy consumption, CVD can minimize greenhouse gas emissions and ecotoxicity.
-
Challenges and Considerations:
- Energy Consumption: The process requires significant energy for heating and maintaining the vacuum environment.
- Catalyst Deposition: Proper catalyst preparation and deposition are critical for achieving uniform CNT growth.
- By-Product Management: Gaseous by-products must be carefully managed to reduce environmental impact.
-
Applications of CVD-Synthesized CNTs:
- CNTs produced via CVD are used in various applications, including electronics, composites, energy storage, and biomedical devices, due to their exceptional mechanical, electrical, and thermal properties.
By understanding the CVD process and its parameters, researchers and manufacturers can optimize CNT synthesis for specific applications while minimizing environmental impact.
Summary Table:
Aspect | Details |
---|---|
Process Overview | Gaseous precursors react on a heated substrate to form a solid thin film. |
Key Steps | Transport, adsorption, surface reactions, nucleation, desorption. |
Catalyst Role | Transition metals (e.g., iron, nickel, cobalt) lower energy barriers. |
Advantages | High purity, structural control, cost-effectiveness, eco-friendly. |
Challenges | High energy use, catalyst deposition, by-product management. |
Applications | Electronics, composites, energy storage, biomedical devices. |
Interested in optimizing CNT synthesis for your applications? Contact our experts today to learn more!