Cold isostatic pressing (CIP) is a powder compaction method that applies uniform pressure from all directions using a liquid or gaseous medium. This process is widely used to consolidate metal and ceramic powders into near-net shapes with high density and uniformity. CIP is particularly advantageous for producing complex geometries and materials that are difficult to process using traditional methods. The process involves placing powder in a flexible mold, which is then pressurized in a chamber, often reaching pressures as high as 100,000 psi. CIP is utilized in various industries, including aerospace, automotive, and electronics, for applications such as advanced ceramics, refractory materials, and electrical insulators.
Key Points Explained:
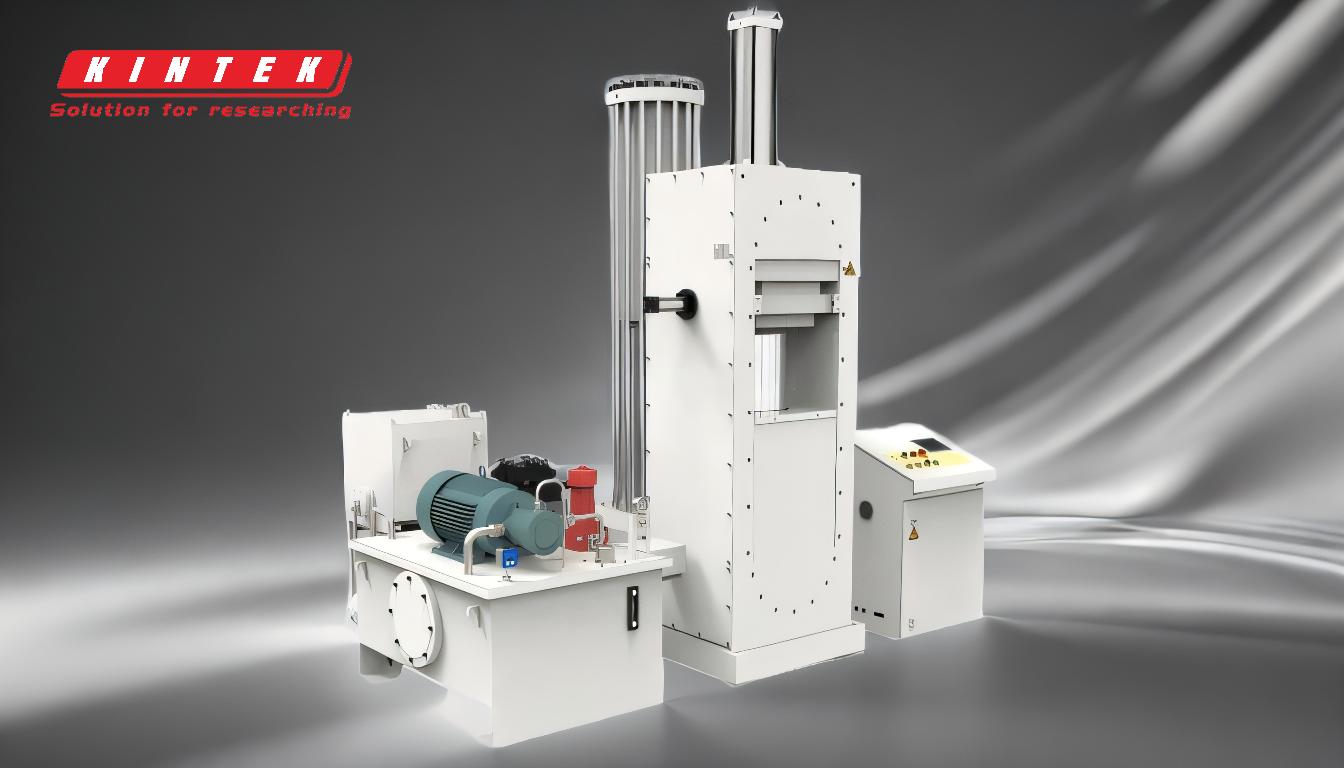
-
Definition and Mechanism of Cold Isostatic Pressing:
- Cold isostatic pressing (CIP) is a powder compaction technique that applies uniform hydrostatic pressure from all directions using a liquid or gaseous medium. This ensures even compaction and high-density products.
- The process involves placing powder in a flexible mold, typically made of polyurethane, and sealing it. The mold is then subjected to high pressure in a chamber, often using an oil-water mixture as the pressurizing medium.
-
Wet-Bag vs. Dry-Bag Techniques:
- Wet-Bag Technique: In this method, the flexible mold containing the powder is submerged in a pressure vessel filled with a pressurizing fluid. After compaction, the mold is removed from the vessel.
- Dry-Bag Technique: Here, the flexible mold is fixed within the pressure vessel, and powder is loaded without removing the mold. This method is more suitable for high-volume production.
-
Pressure and Density Achievements:
- CIP can achieve extremely high pressures, often up to 100,000 psi, ensuring uniform compaction.
- The process can achieve a theoretical density of about 100% for metals and about 95% for ceramic powders, making it highly effective for producing dense and uniform components.
-
Advantages of CIP:
- Uniform Compaction: The hydrostatic pressure ensures uniform density and mechanical properties throughout the compacted part.
- Complex Geometries: CIP is capable of producing parts with complex shapes that are difficult to achieve with other methods.
- Material Versatility: It is suitable for a wide range of materials, including metals, ceramics, and refractory materials.
-
Applications of CIP:
- Advanced Ceramics: Materials such as silicon nitride, silicon carbide, and boron carbide are commonly processed using CIP.
- Refractory Materials: CIP is used to produce high-performance refractory materials for extreme environments.
- Electrical Insulators: The process is ideal for manufacturing electrical insulators with precise dimensions and properties.
-
Economic and Quality Benefits:
- CIP technology improves product performance and quality, leading to increased economic benefits. Its advantages over other molding processes have expanded its application fields and increased its technological maturity.
By understanding these key points, one can appreciate the versatility and effectiveness of isostatic press technology in modern manufacturing. Whether for producing advanced ceramics or complex metal components, CIP offers a reliable and efficient solution for achieving high-density, uniform products.
Summary Table:
Key Aspect | Details |
---|---|
Process | Applies uniform hydrostatic pressure from all directions using liquid/gas. |
Techniques | Wet-Bag (mold submerged) vs. Dry-Bag (mold fixed). |
Pressure | Up to 100,000 psi for uniform compaction. |
Density Achievements | ~100% for metals, ~95% for ceramics. |
Advantages | Uniform compaction, complex geometries, material versatility. |
Applications | Advanced ceramics, refractory materials, electrical insulators. |
Learn how cold isostatic pressing can enhance your manufacturing process—contact us today!