A controlled atmosphere furnace is a specialized heating device designed to provide precise temperature control and a tightly sealed environment, enabling the creation of protective or reactive atmospheres. These furnaces are essential for processes like sintering, brazing, heat treatment, and material research, where maintaining specific atmospheric conditions is critical to achieving desired material properties. They are widely used in industries such as ceramics, metallurgy, electronics, and chemical processing, as well as in academic and research institutions. Key features include excellent sealing, uniform atmosphere flow, advanced safety mechanisms, and energy-efficient operation, making them indispensable for high-temperature applications requiring controlled environments.
Key Points Explained:
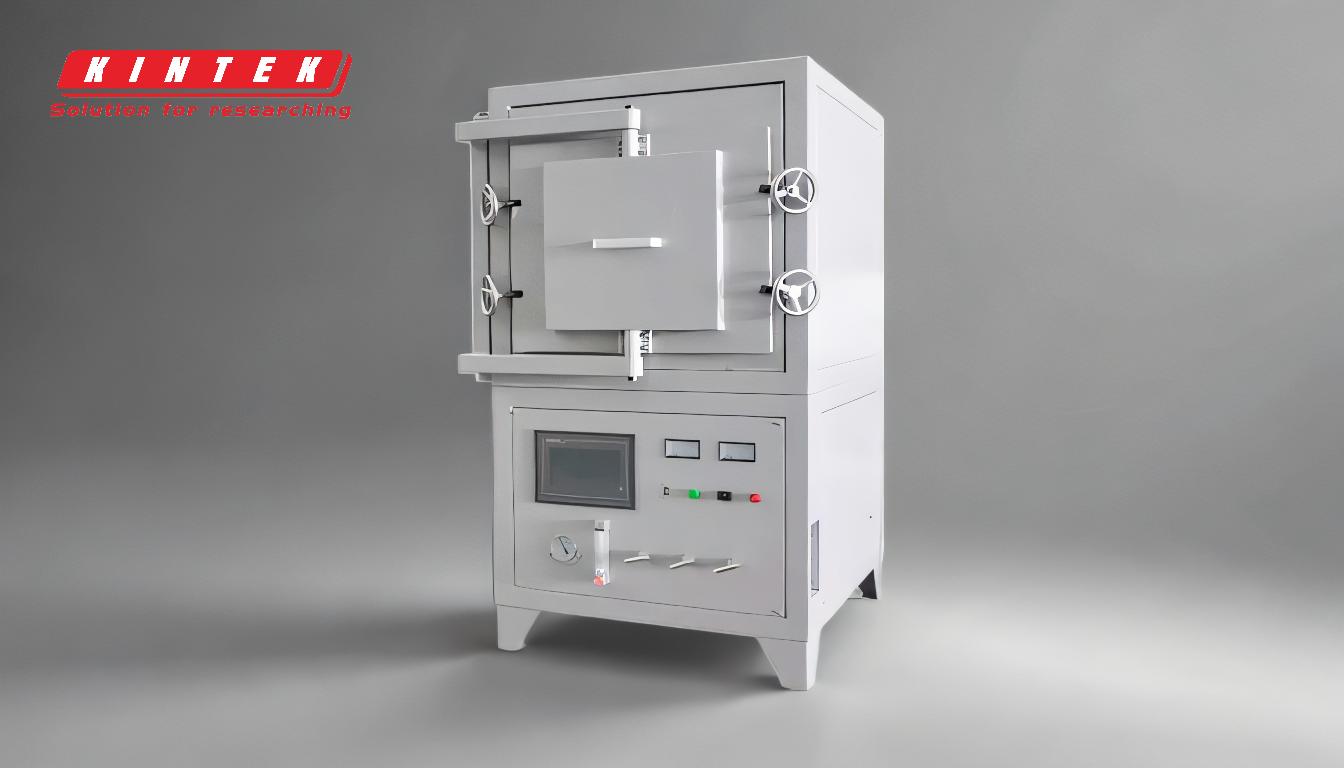
-
Definition and Purpose:
- A controlled atmosphere furnace is a furnace designed to maintain a specific atmospheric environment during heating processes. This environment can be protective (e.g., inert gases like nitrogen or argon) or reactive (e.g., hydrogen or carbon monoxide), depending on the application.
- The primary purpose is to prevent oxidation, contamination, or unwanted chemical reactions, ensuring the desired material properties are achieved during processes like sintering, brazing, or heat treatment.
-
Key Features:
- Tight Sealing: The furnace chamber or muffle is tightly sealed to prevent external air infiltration, which could disrupt the controlled atmosphere.
- Uniform Atmosphere Flow: Ensures consistent distribution of gases within the chamber, critical for uniform material processing.
- Heating Elements: Designed to withstand high temperatures and specific atmospheres, ensuring durability and performance.
- Safety Mechanisms: Includes explosion protection devices and safety systems for handling potentially hazardous gases.
-
Applications:
- Material Research: Used in laboratories for high-temperature experiments, sintering, and material treatment.
- Industrial Processes: Applied in metallurgy, ceramics, electronics, and chemical industries for processes like annealing, brazing, and powder roasting.
- Academic Use: Commonly found in universities and research institutes for teaching and experimental purposes.
-
Advantages:
- Energy Efficiency: Designed to minimize energy consumption while maintaining high performance.
- Precision Control: Allows for precise adjustment of temperature, time, and atmospheric conditions, ensuring optimal results.
- Versatility: Suitable for processing parts of various shapes and sizes, making it adaptable to diverse applications.
- Safety and Environmental Friendliness: Equipped with safety devices and designed to reduce emissions, ensuring safe and eco-friendly operation.
-
Industries and Fields:
- Ceramics and Metallurgy: For sintering and heat treatment of metals and ceramics.
- Electronics and Glass: Used in the production of electronic components and glass materials.
- Chemical and Mechanical Industries: For processes like flue gas treatment and material annealing.
- Research and Education: Widely used in universities and research institutes for experimental and teaching purposes.
-
Operational Considerations:
- Atmosphere Control: Requires careful selection and management of gases to achieve the desired results.
- Temperature Management: Precise temperature control is critical for processes like brazing and sintering.
- Safety Protocols: Proper handling of gases and adherence to safety guidelines are essential to prevent accidents.
By combining these features and capabilities, a controlled atmosphere furnace offers a reliable and efficient solution for high-temperature processes that require precise environmental control. Its versatility and advanced design make it a valuable tool across various industries and research fields.
Summary Table:
Aspect | Details |
---|---|
Purpose | Maintains specific atmospheric conditions to prevent oxidation or contamination. |
Key Features | Tight sealing, uniform atmosphere flow, durable heating elements, safety mechanisms. |
Applications | Material research, industrial processes (metallurgy, ceramics, electronics), academic use. |
Advantages | Energy efficiency, precision control, versatility, safety, and eco-friendliness. |
Industries | Ceramics, metallurgy, electronics, chemical processing, research, and education. |
Operational Considerations | Atmosphere control, temperature management, and safety protocols. |
Need a controlled atmosphere furnace for your lab or industry? Contact us today to find the perfect solution!