Controlled pyrolysis is a thermal decomposition process that occurs in the absence of oxygen, where organic materials such as biomass, plastics, or tires are heated to high temperatures (typically 400-900°C) to break them down into valuable byproducts like syngas, bio-oil, and bio-char. This process is carefully managed to optimize the yield and quality of the end products while ensuring safety and efficiency. The pyrolysis reactor is the core component where this transformation occurs, and its design and operation are critical to the success of the process. Controlled pyrolysis is used in various applications, including waste management, renewable energy production, and material recovery.
Key Points Explained:
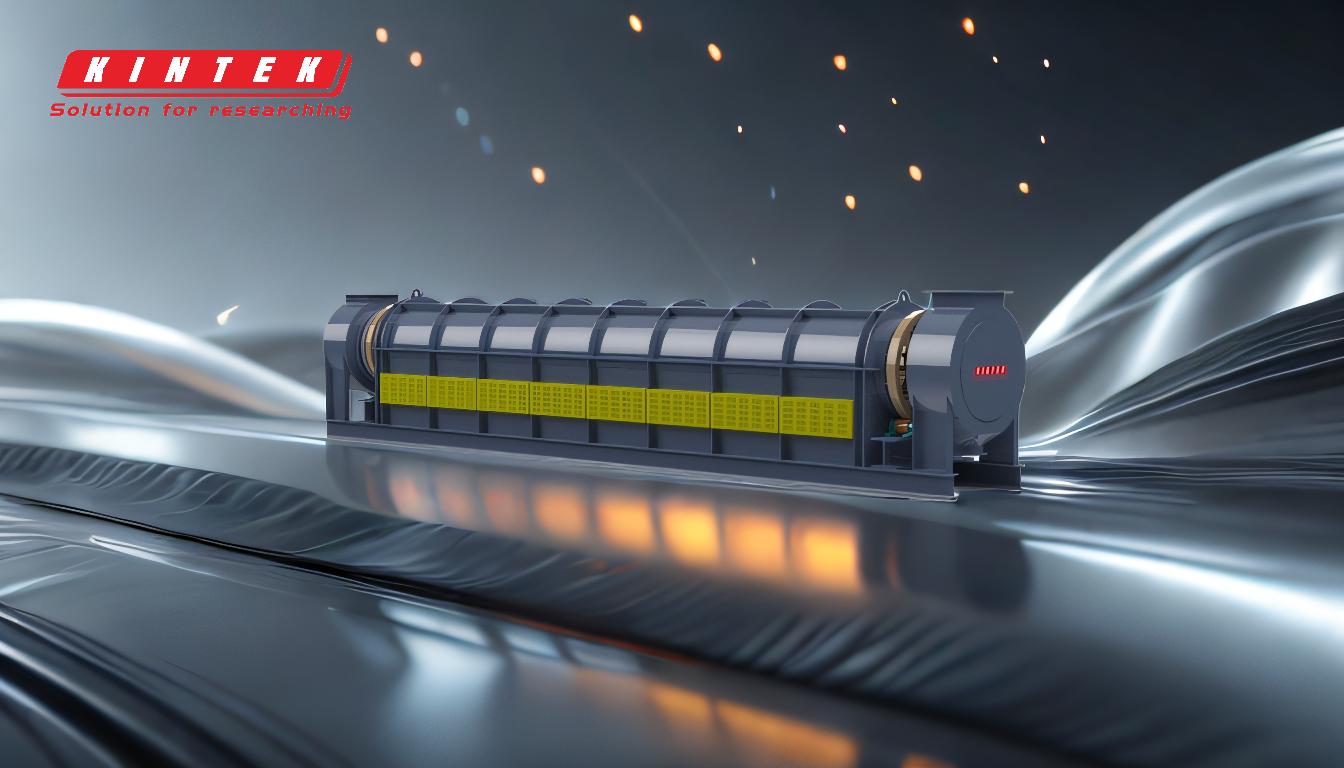
-
Definition and Purpose of Controlled Pyrolysis:
- Controlled pyrolysis is a process that thermally decomposes organic materials in an oxygen-free environment to produce syngas, bio-oil, and bio-char.
- The process is carefully regulated to ensure optimal conditions for decomposition, maximizing the yield and quality of the byproducts.
- It is widely used in industries such as waste management, renewable energy, and material recovery.
-
Role of the Pyrolysis Reactor:
- The pyrolysis reactor is the central component where the thermal decomposition of materials takes place.
- It is designed to handle high temperatures (400-900°C) and ensure uniform heat distribution for efficient decomposition.
- Different types of reactors, such as fixed-bed, continuous, and ablative reactors, are used depending on the feedstock and desired output.
-
Types of Pyrolysis Reactors:
- Fixed-Bed Reactor: A simple design where the substrate is introduced at the bottom, and heat is applied from the walls. Heat transfer occurs consistently, leading to thermal decomposition.
- Continuous Reactor: Used in processes like tire pyrolysis, where materials are continuously fed into the reactor, and the byproducts are collected in stages.
- Ablative Reactor: A pressure-driven system where the substrate is pressed against heated walls, causing it to melt and decompose.
-
Process Steps in Controlled Pyrolysis:
- Feeding: Materials like biomass, plastics, or tires are introduced into the reactor.
- Heating: The materials are heated to high temperatures in the absence of oxygen, causing thermal decomposition.
- Cooling: The generated oil gas is cooled to obtain liquid byproducts like bio-oil.
- Recycling: Non-condensable gases are recycled to heat the reactor, improving energy efficiency.
- Collection: Solid byproducts like bio-char or carbon black are collected for further use.
-
Applications of Controlled Pyrolysis:
- Waste Management: Converts waste materials like tires and plastics into useful products, reducing landfill dependency.
- Renewable Energy: Produces syngas and bio-oil, which can be used as alternative fuels.
- Material Recovery: Generates bio-char, which can be used as a soil amendment or feedstock for activated carbon production.
-
Safety and Control Systems:
- Controlled pyrolysis plants are equipped with advanced safety and control systems to monitor temperature, pressure, and gas composition.
- These systems ensure efficient operation and prevent hazards such as overheating or gas leaks.
-
Advantages of Controlled Pyrolysis:
- Sustainability: Converts waste into valuable resources, promoting a circular economy.
- Energy Efficiency: Recycling non-condensable gases reduces energy consumption.
- Versatility: Can process a wide range of organic materials, making it adaptable to various industries.
By understanding the principles and components of controlled pyrolysis, industries can effectively harness this technology to manage waste, produce renewable energy, and recover valuable materials. The pyrolysis reactor plays a pivotal role in ensuring the success of this process, making it a critical focus for equipment and consumable purchasers.
Summary Table:
Aspect | Details |
---|---|
Process | Thermal decomposition in an oxygen-free environment (400-900°C). |
Byproducts | Syngas, bio-oil, bio-char. |
Key Component | Pyrolysis reactor (fixed-bed, continuous, or ablative). |
Applications | Waste management, renewable energy, material recovery. |
Advantages | Sustainability, energy efficiency, versatility. |
Discover how controlled pyrolysis can transform your waste into valuable resources—contact us today!