A Chemical Vapor Deposition (CVD) chamber is a specialized enclosure designed to facilitate the CVD process, which involves the deposition of a solid material onto a substrate through chemical reactions in the vapor phase. This process is widely used in industries such as semiconductor manufacturing, optics, and coatings due to its ability to produce high-quality, uniform, and durable thin films. The CVD chamber is a critical component of the CVD system, providing the controlled environment necessary for the chemical reactions to occur. It typically includes systems for gas delivery, temperature control, vacuum, and exhaust management to ensure precise and efficient deposition.
Key Points Explained:
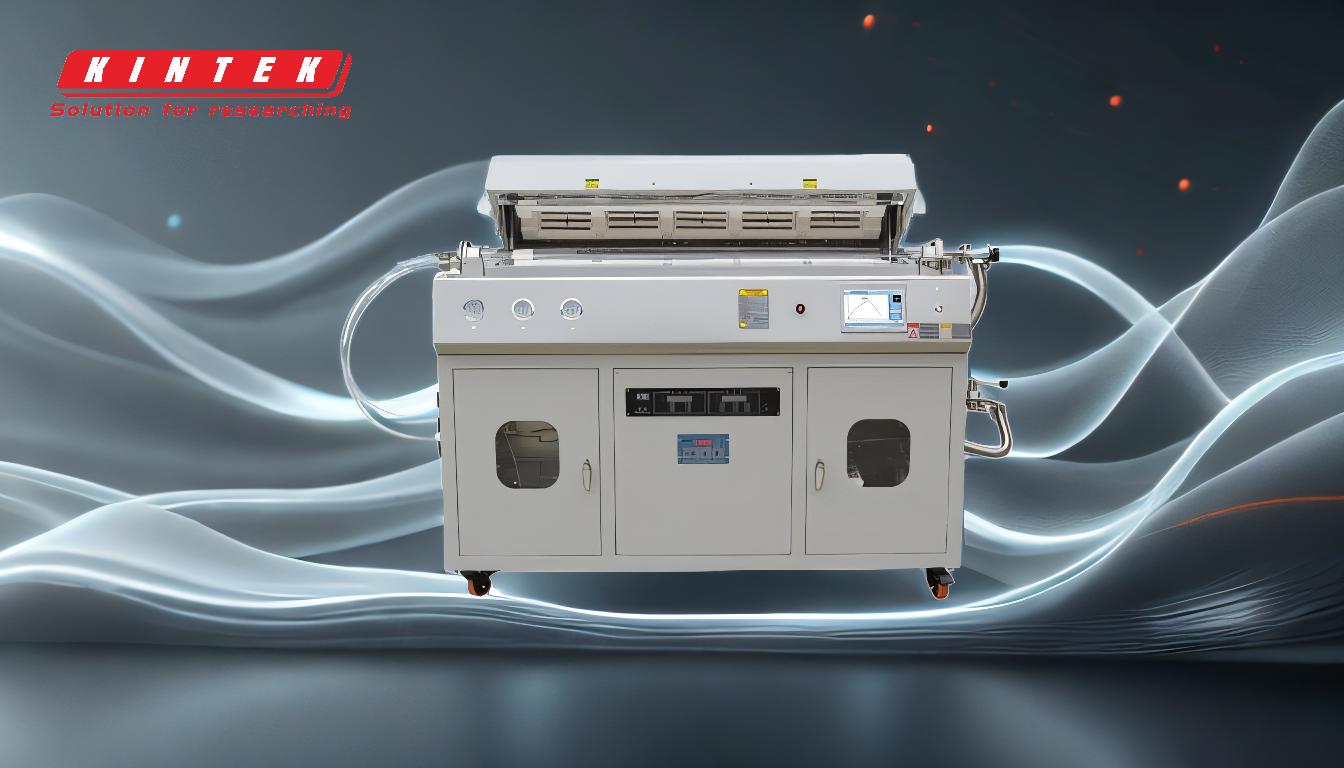
-
Definition and Purpose of a CVD Chamber:
- A chemical vapor deposition chamber is an enclosed space where the CVD process takes place. It is designed to create a controlled environment for the chemical reactions that deposit thin films onto substrates.
- The primary purpose of the chamber is to ensure uniform deposition, precise control over reaction conditions, and the ability to handle a wide range of materials and gases.
-
Components of a CVD Chamber:
- Gas Delivery System: Delivers precursor gases and reaction gases into the chamber in precise quantities.
- Reaction Chamber/Reactor: The core component where the substrate is placed and the chemical reactions occur.
- Loading/Unloading System: Facilitates the introduction and removal of substrates without disrupting the chamber's controlled environment.
- Energy Source: Provides the necessary heat or plasma energy to initiate and sustain the chemical reactions.
- Vacuum System: Maintains the required low-pressure environment to optimize the deposition process.
- Process Control System: Automates and monitors the process parameters such as temperature, pressure, and gas flow rates.
- Exhaust Gas Treatment System: Safely removes and treats byproducts and unused gases to prevent contamination and environmental harm.
-
How CVD Chambers Work:
- The process begins with the introduction of precursor gases into the chamber. These gases react or decompose when exposed to heat or plasma energy, forming a solid material that deposits onto the substrate.
- The chamber's controlled environment ensures that the deposition occurs uniformly and adheres well to the substrate, even on complex or precision surfaces.
-
Advantages of CVD Chambers:
- Versatility: CVD chambers can deposit coatings on a wide range of materials, including ceramics, metals, and glass.
- Precision: They enable the creation of ultra-thin, uniform layers, making them ideal for applications like semiconductor manufacturing and optical coatings.
- Durability: Coatings produced in CVD chambers are highly durable and can withstand extreme temperatures and stress environments.
- Customization: Gases and process parameters can be optimized for specific properties such as corrosion resistance, abrasion resistance, or high purity.
-
Applications of CVD Chambers:
- Semiconductor Industry: Used for depositing thin films in the production of electrical circuits and microelectronics.
- Optics: Applied in the manufacturing of anti-reflective coatings and optical filters.
- Coatings: Used to enhance the durability, friction resistance, and thermal properties of various materials.
- Advanced Materials: Enables the production of specialized materials like graphene and carbon nanotubes.
-
Types of CVD Chambers:
- Thermal CVD Chambers: Utilize heat to initiate chemical reactions.
- Plasma-Enhanced CVD (PECVD) Chambers: Use plasma energy to lower the required reaction temperature, making them suitable for temperature-sensitive substrates.
- Low-Pressure CVD (LPCVD) Chambers: Operate under reduced pressure to improve film uniformity and reduce contamination.
-
Challenges and Considerations:
- Cost: CVD chambers and their associated systems can be expensive to purchase and maintain.
- Complexity: The process requires precise control over multiple parameters, which can be technically challenging.
- Safety: Handling reactive gases and byproducts requires robust safety measures to prevent accidents and environmental harm.
In summary, a CVD chamber is a sophisticated piece of equipment that plays a vital role in the CVD process. Its ability to create high-quality, durable, and precise coatings makes it indispensable in industries requiring advanced material deposition. Understanding its components, working principles, and applications is essential for anyone involved in materials science, semiconductor manufacturing, or related fields.
Summary Table:
Aspect | Details |
---|---|
Purpose | Facilitates chemical vapor deposition (CVD) for thin film creation. |
Key Components | Gas delivery, reaction chamber, vacuum system, energy source, and more. |
Advantages | Versatile, precise, durable, and customizable for various applications. |
Applications | Semiconductors, optics, coatings, and advanced materials like graphene. |
Types | Thermal CVD, Plasma-Enhanced CVD (PECVD), Low-Pressure CVD (LPCVD). |
Challenges | High cost, technical complexity, and safety considerations. |
Ready to explore how a CVD chamber can enhance your processes? Contact us today for expert guidance!