Chemical Vapor Deposition (CVD) is a manufacturing process used to produce high-quality, high-performance solid materials, typically in the form of thin films. The process involves the chemical reaction of gaseous precursors on a substrate surface, leading to the deposition of a solid material. CVD is widely used in various industries, including semiconductor manufacturing, optics, and coatings, due to its ability to produce materials with precise control over composition, thickness, and structure. The process can be conducted under different conditions, including vacuum, which helps in controlling the deposition environment and improving the quality of the deposited material.
Key Points Explained:
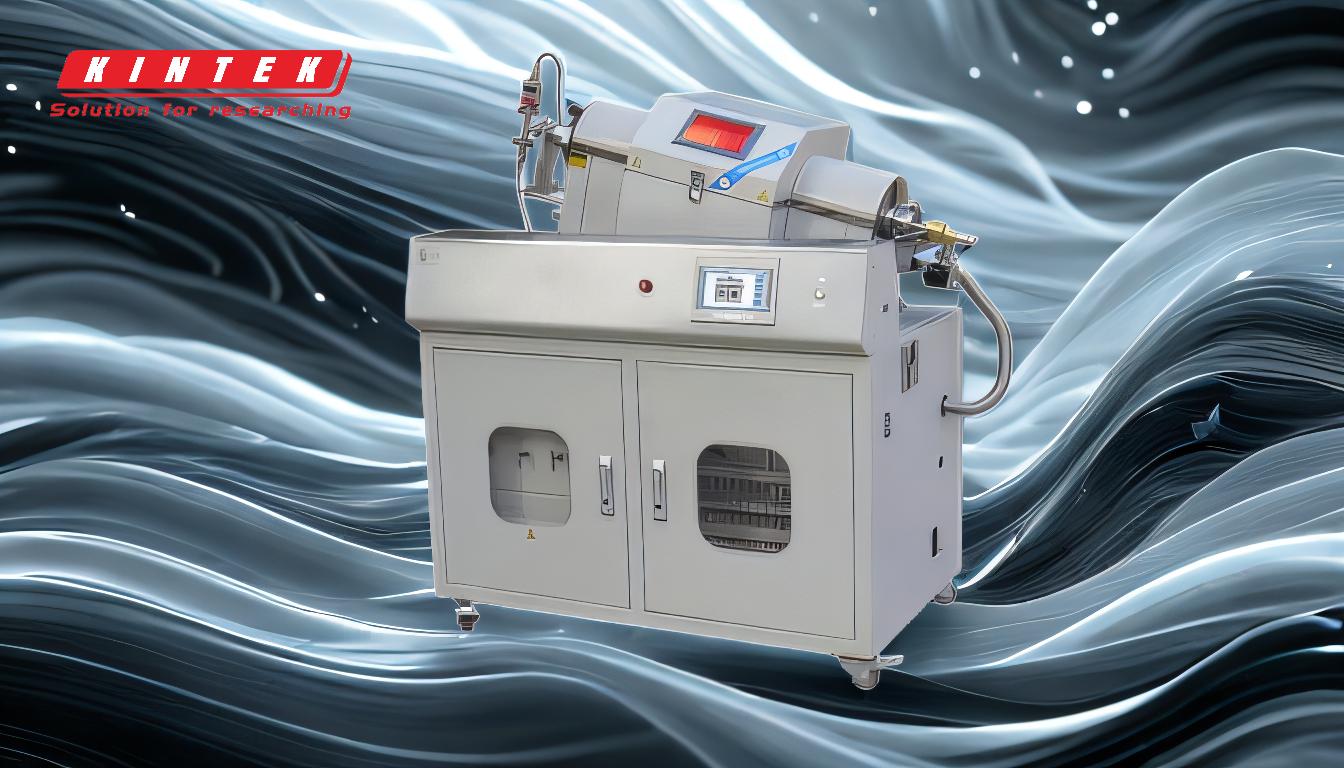
-
Definition of CVD:
- CVD stands for Chemical Vapor Deposition, a process where gaseous reactants are introduced into a reaction chamber and react on a heated substrate to form a solid material. This technique is essential for creating thin films and coatings with specific properties.
-
Role of Vacuum in CVD:
- In CVD, vacuum conditions can be employed to control the pressure within the reaction chamber. This is crucial for several reasons:
- Reduced Contamination: Lower pressure reduces the likelihood of contaminants entering the chamber, leading to purer deposits.
- Enhanced Control: Vacuum allows for better control over the deposition rate and the uniformity of the film.
- Lower Temperature Operation: Similar to short path vacuum distillation, reducing pressure can lower the required temperature for the deposition process, which is beneficial for heat-sensitive materials.
- In CVD, vacuum conditions can be employed to control the pressure within the reaction chamber. This is crucial for several reasons:
-
Comparison with Short Path Vacuum Distillation:
- Both CVD and short path vacuum distillation utilize vacuum conditions to enhance process efficiency:
- Pressure Reduction: In both processes, reducing the pressure lowers the boiling or reaction temperatures, which is advantageous for handling sensitive materials.
- Efficiency: Vacuum conditions facilitate faster and more efficient separation or deposition by drawing vapors towards the desired location (condenser in distillation, substrate in CVD).
- Both CVD and short path vacuum distillation utilize vacuum conditions to enhance process efficiency:
-
Applications of CVD:
- CVD is used in a variety of applications, including:
- Semiconductor Fabrication: For depositing thin films of silicon, silicon dioxide, and other materials used in integrated circuits.
- Optical Coatings: For creating anti-reflective coatings on lenses and mirrors.
- Protective Coatings: For applying wear-resistant and corrosion-resistant layers on tools and components.
- CVD is used in a variety of applications, including:
-
Advantages of CVD:
- High Purity: The process can produce extremely pure materials.
- Uniformity: CVD allows for the deposition of uniform thin films over large areas.
- Versatility: It can be used to deposit a wide range of materials, including metals, semiconductors, and ceramics.
-
Challenges in CVD:
- Complexity: The process can be complex and requires precise control over various parameters such as temperature, pressure, and gas flow rates.
- Cost: Equipment and operational costs can be high, especially for high-vacuum systems.
- Safety: Handling of reactive gases and high temperatures requires stringent safety measures.
In summary, CVD is a versatile and powerful manufacturing technique that leverages chemical reactions under controlled conditions to deposit high-quality materials. The use of vacuum, as seen in short path vacuum distillation, plays a critical role in optimizing the process, particularly for applications requiring high purity and precision.
Summary Table:
Aspect | Details |
---|---|
Definition | A process using gaseous reactants to deposit solid materials on a substrate. |
Role of Vacuum | Reduces contamination, enhances control, and lowers operating temperatures. |
Applications | Semiconductor fabrication, optical coatings, and protective coatings. |
Advantages | High purity, uniformity, and versatility in material deposition. |
Challenges | Complexity, high costs, and safety concerns. |
Discover how CVD can revolutionize your manufacturing process—contact our experts today!