CVD metal refers to metals deposited through the Chemical Vapor Deposition (CVD) process, a technique widely used in industries such as semiconductors, electronics, and protective coatings. CVD involves the chemical reaction of gaseous precursors with a substrate to form thin, uniform, and high-purity metal films. This method is distinct from Physical Vapor Deposition (PVD) as it is a non-line-of-sight process, allowing for the coating of complex geometries, including threads and internal surfaces. CVD metals are known for their excellent adhesion, uniformity, and versatility, making them ideal for applications in electronics, optics, and tool coatings.
Key Points Explained:
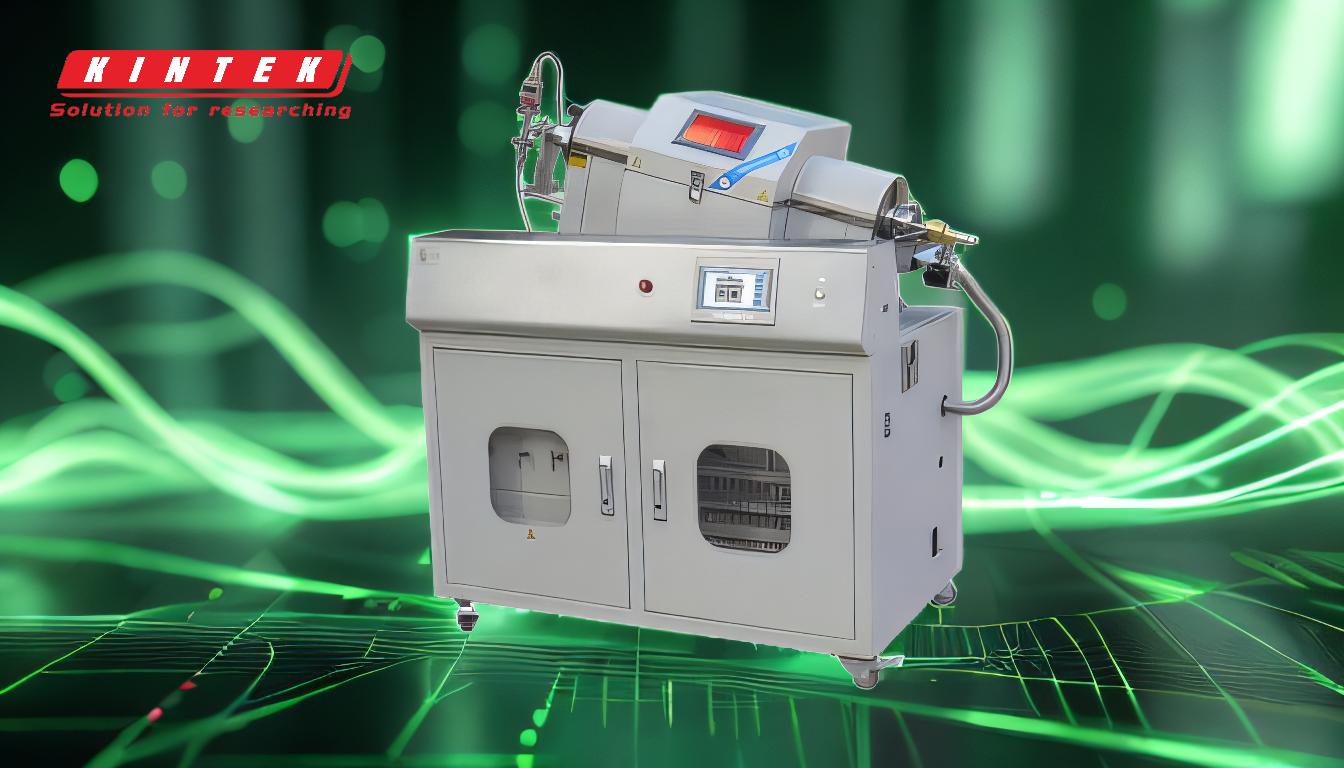
-
Definition of CVD Metal:
- CVD metal refers to metals deposited using the Chemical Vapor Deposition process. This involves the reaction of gaseous precursors with a substrate to form thin, high-purity metal films. The process occurs at high temperatures (around 1000 °C), ensuring strong adhesion and uniformity.
-
How CVD Works:
- CVD uses gaseous precursors that chemically react with the substrate surface to form a solid metal layer. This is different from PVD, which relies on physical vaporization and condensation of solid materials. CVD is a non-line-of-sight process, meaning it can coat complex geometries, including internal surfaces and blind holes.
-
Advantages of CVD Metals:
- High Purity and Uniformity: CVD produces films with excellent purity and uniformity, making them suitable for precision applications like semiconductors.
- Superior Adhesion: The chemical bonding during CVD ensures stronger adhesion compared to PVD or spray coatings.
- Versatility: CVD can be used to deposit a wide range of materials, including metals, insulators, and alloys.
-
Applications of CVD Metals:
- Semiconductors: CVD is extensively used in the semiconductor industry to deposit insulating, metallic, and alloy materials for chip manufacturing.
- Protective Coatings: CVD metals are used to create durable, wear-resistant coatings on tools and components.
- Optical and Barrier Layers: CVD is used to apply optical coatings on glass and plastics, as well as gas-tight barrier layers.
- Synthetic Diamond Layers: CVD is employed to deposit synthetic diamond layers on tools for enhanced durability.
-
Comparison with PVD:
- CVD differs from PVD in several ways:
- Process: CVD involves chemical reactions, while PVD relies on physical vaporization and condensation.
- Coating Coverage: CVD is non-line-of-sight, enabling it to coat complex geometries, whereas PVD is line-of-sight and limited to exposed surfaces.
- Adhesion: CVD coatings have superior adhesion due to chemical bonding.
- CVD differs from PVD in several ways:
-
Industrial Significance:
- CVD is a cornerstone technology in industries requiring high-precision coatings, such as electronics, optics, and tool manufacturing. Its ability to produce uniform, high-quality films makes it indispensable for applications like transistor structures, conductor gap filling, and protective layers.
In summary, CVD metal is a critical material in modern manufacturing, offering unparalleled purity, adhesion, and versatility. Its applications span across high-tech industries, making it a key enabler of advanced technologies in electronics, optics, and beyond.
Summary Table:
Key Aspect | Details |
---|---|
Definition | Metals deposited via Chemical Vapor Deposition (CVD) process. |
Process | Chemical reaction of gaseous precursors with a substrate at high temperatures. |
Advantages | High purity, uniformity, superior adhesion, and versatility. |
Applications | Semiconductors, protective coatings, optical layers, synthetic diamond tools. |
Comparison with PVD | Non-line-of-sight, superior adhesion, and ability to coat complex geometries. |
Interested in CVD metal solutions? Contact us today to learn how we can meet your industrial needs!