The CVD (Chemical Vapor Deposition) process is a sophisticated technique used to deposit thin films onto a substrate through chemical reactions in the vapor phase. This method involves exposing a substrate to volatile precursors that react or decompose on its surface, forming a solid deposit. Key parameters such as deposition temperature, precursor flow rates, and pressure significantly influence the quality and characteristics of the deposited film. CVD can be performed at both atmospheric and low pressures, offering versatility in applications ranging from semiconductor manufacturing to protective coatings. Additionally, the short path vacuum distillation process, while distinct from CVD, shares the use of vacuum conditions to lower boiling points, which is crucial for handling heat-sensitive materials.
Key Points Explained:
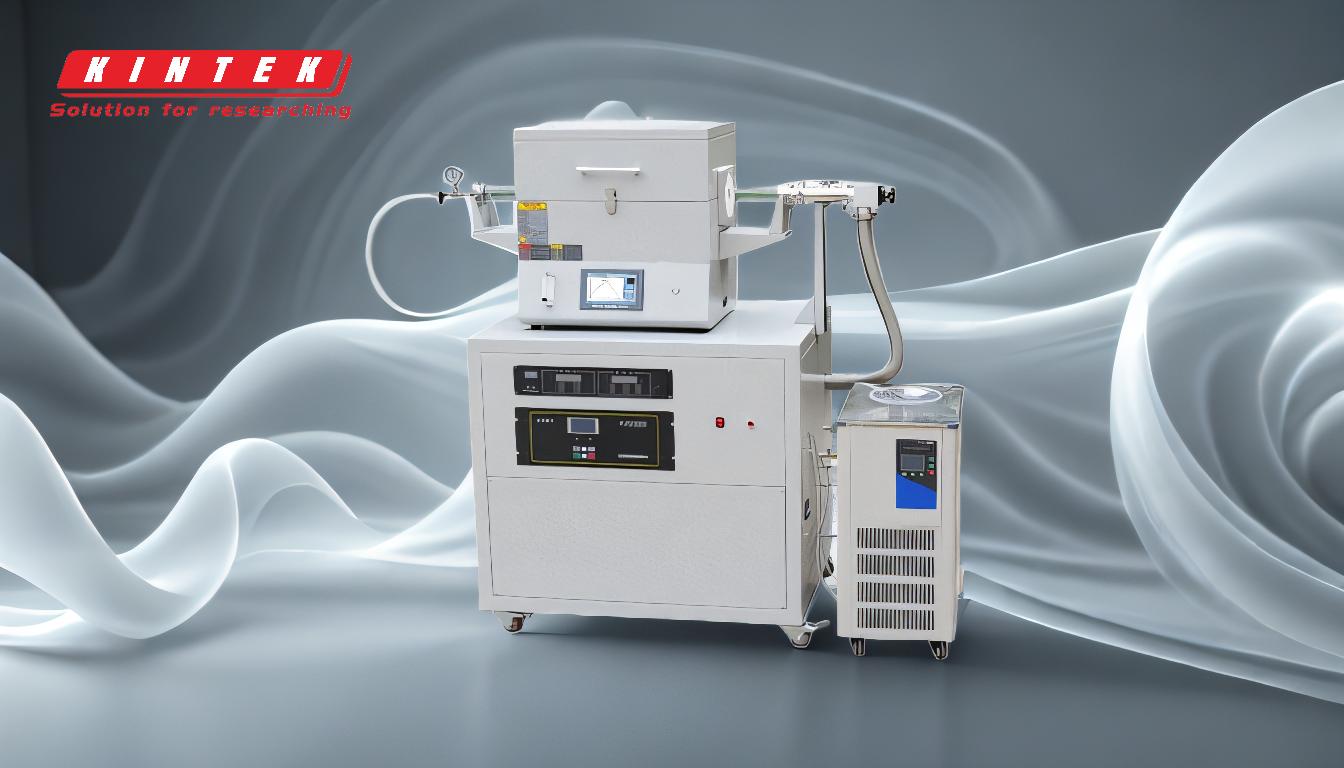
-
Fundamentals of CVD Process:
- CVD involves the deposition of thin films through chemical reactions in the vapor phase. Precursors in gaseous form react or decompose on the substrate surface, forming a solid deposit.
- The process can produce coatings, powders, or single-crystal materials, depending on the application and conditions.
- CVD is widely used in industries such as semiconductors, optics, and protective coatings due to its ability to produce high-purity and high-performance materials.
-
Key Parameters in CVD:
- Deposition Temperature: The temperature of the substrate plays a critical role in determining the reaction kinetics and the quality of the deposited film.
- Precursor Flow Rates: The rate at which precursors are introduced into the reaction chamber affects the uniformity and thickness of the deposited film.
- Pressure: CVD can be performed at atmospheric or low pressures. Low-pressure CVD (LPCVD) is often used for better control over film properties and uniformity.
-
Applications of CVD:
- Semiconductors: CVD is essential for producing thin films in integrated circuits and microelectronics.
- Optical Coatings: CVD is used to deposit anti-reflective and protective coatings on lenses and mirrors.
- Protective Coatings: CVD coatings are applied to tools and components to enhance durability and resistance to wear and corrosion.
-
Comparison with Short Path Vacuum Distillation:
- While CVD focuses on thin film deposition, short path vacuum distillation is a separation technique used for purifying heat-sensitive materials.
- Both processes utilize vacuum conditions to lower boiling points, but their objectives differ. CVD aims to deposit materials, whereas short path distillation focuses on isolating and purifying compounds.
-
Advantages of CVD:
- High Purity: CVD produces films with exceptional purity and uniformity.
- Versatility: The process can deposit a wide range of materials, including metals, ceramics, and polymers.
- Scalability: CVD is suitable for both small-scale laboratory research and large-scale industrial production.
-
Challenges in CVD:
- Complexity: The process requires precise control over parameters such as temperature, pressure, and precursor flow rates.
- Cost: CVD equipment and precursors can be expensive, making the process less accessible for some applications.
- Safety: Handling volatile and reactive precursors requires stringent safety measures.
By understanding the CVD process and its key parameters, one can appreciate its significance in modern technology and its distinction from other processes like short path vacuum distillation. Both techniques, however, demonstrate the importance of controlled environments in achieving desired outcomes in material science and chemical engineering.
Summary Table:
Aspect | Details |
---|---|
Fundamentals | Deposition of thin films via chemical reactions in the vapor phase. |
Key Parameters | Deposition temperature, precursor flow rates, and pressure. |
Applications | Semiconductors, optical coatings, and protective coatings. |
Advantages | High purity, versatility, and scalability. |
Challenges | Complexity, high cost, and safety concerns. |
Comparison with SPVD | CVD deposits materials; SPVD purifies heat-sensitive compounds. |
Discover how the CVD process can revolutionize your material applications—contact our experts today!