CVD (Chemical Vapor Deposition) and PVD (Physical Vapor Deposition) are two advanced techniques used to create diamond coatings or films, each with distinct processes and characteristics. CVD diamonds are synthetic diamonds formed through chemical reactions between gases and a substrate, resulting in high-purity Type IIA diamonds that are rare in nature. PVD, on the other hand, involves the physical vaporization of solid materials, which then condense onto a substrate to form thin, durable coatings. While CVD allows for thicker and rougher coatings suitable for a wide range of materials, PVD produces smoother, thinner films ideal for high-temperature applications. The choice between CVD and PVD depends on the specific requirements of the application, such as coating thickness, material compatibility, and temperature tolerance.
Key Points Explained:
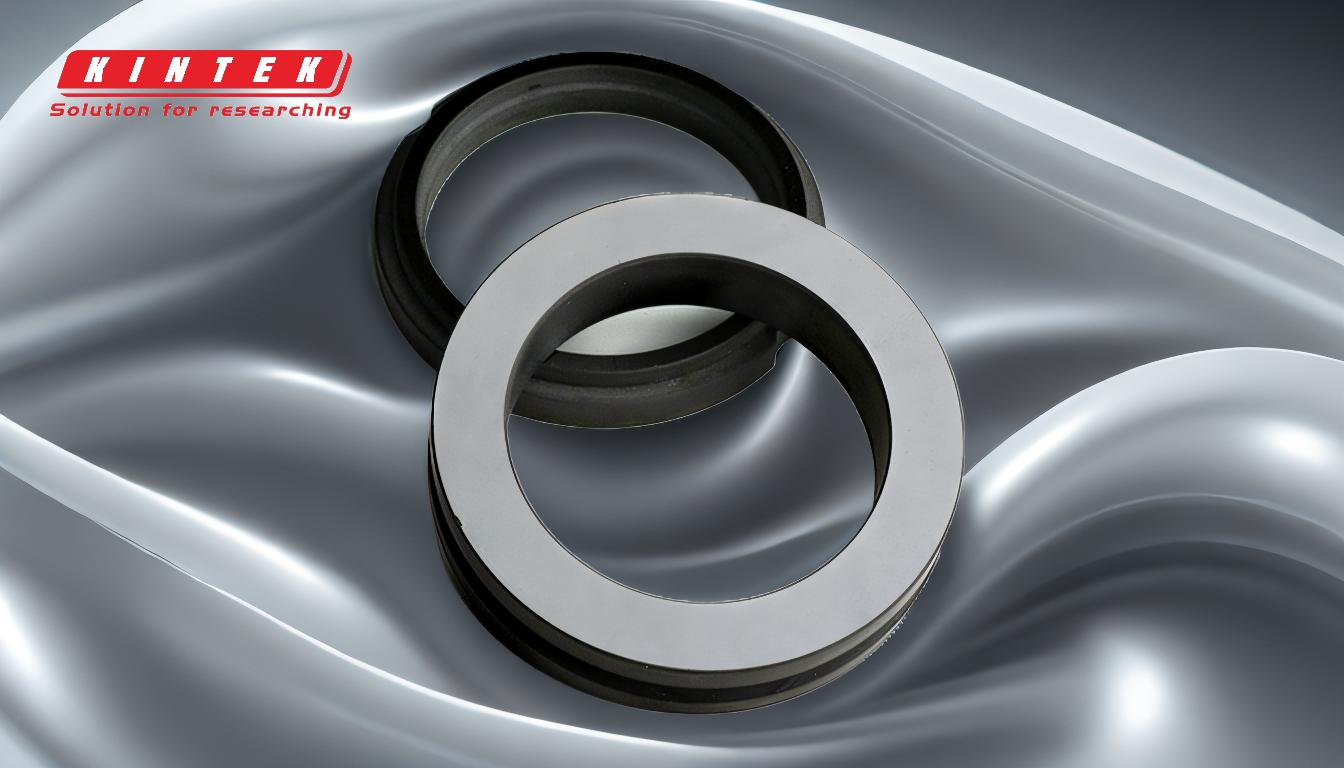
-
Nature of Deposition Process:
- CVD: Involves a chemical reaction between gaseous molecules and the substrate. The process is multidirectional, meaning the coating forms uniformly around the substrate. This method is ideal for creating thicker coatings and is suitable for a wide range of materials.
- PVD: Relies on the physical vaporization of solid materials, which are then deposited onto the substrate in a line-of-sight manner. This results in thinner, smoother coatings that are highly durable and resistant to high temperatures.
-
Material Characteristics:
- CVD Diamonds: These are synthetic diamonds classified as Type IIA, which are extremely rare in nature. They lack nitrogen and boron impurities, making them highly pure. CVD diamonds may exhibit unique features like strain lines or fluorescence under UV light, though these are not always visible to the naked eye.
- PVD Coatings: These coatings are typically thin, smooth, and highly durable. They are ideal for applications requiring high-temperature resistance and precision, such as in the aerospace and electronics industries.
-
Temperature Requirements:
- CVD: Operates at higher temperatures, typically between 450°C to 1050°C. This high-temperature environment facilitates the chemical reactions necessary for diamond formation.
- PVD: Works at lower temperatures, ranging from 250°C to 450°C. This makes it suitable for substrates that cannot withstand the high temperatures required for CVD.
-
Applications:
- CVD: Commonly used in applications requiring thicker, rougher coatings, such as in the manufacturing of cutting tools, wear-resistant coatings, and electronic components.
- PVD: Preferred for applications needing thin, smooth, and durable coatings, such as in the production of optical lenses, medical devices, and decorative finishes.
-
Advantages and Limitations:
- CVD Advantages: Capable of producing high-purity diamonds, suitable for a wide range of materials, and allows for thicker coatings.
- CVD Limitations: Requires high temperatures, which may not be suitable for all substrates, and the coatings can be rougher.
- PVD Advantages: Operates at lower temperatures, produces smooth and durable coatings, and is ideal for precision applications.
- PVD Limitations: Limited to line-of-sight deposition, which may result in uneven coatings on complex geometries, and typically produces thinner coatings compared to CVD.
By understanding these key differences, purchasers can make informed decisions when selecting between CVD and PVD diamond coatings based on their specific application needs.
Summary Table:
Aspect | CVD Diamond | PVD Diamond |
---|---|---|
Process | Chemical reaction between gases and substrate (multidirectional coating) | Physical vaporization of solid materials (line-of-sight deposition) |
Material Characteristics | High-purity Type IIA synthetic diamonds, rare in nature, no impurities | Thin, smooth, and durable coatings, ideal for high-temperature applications |
Temperature Range | 450°C to 1050°C | 250°C to 450°C |
Applications | Cutting tools, wear-resistant coatings, electronic components | Optical lenses, medical devices, decorative finishes |
Advantages | High-purity diamonds, thicker coatings, suitable for various materials | Smooth, durable coatings, lower temperature operation, ideal for precision |
Limitations | High temperatures, rougher coatings | Line-of-sight deposition, thinner coatings, uneven on complex geometries |
Need help choosing between CVD and PVD diamond coatings? Contact our experts today for tailored solutions!