Chemical Vapor Deposition (CVD) is a sophisticated process used to deposit thin, high-quality solid films onto substrates. It involves the use of volatile precursor materials that are vaporized and introduced into a reaction chamber under controlled conditions of temperature, pressure, and flow rate. These precursors undergo chemical reactions, either decomposition or surface reactions, to form a solid layer on the substrate. The process typically occurs in a vacuum environment, which ensures uniform deposition and minimizes contamination. By-products of the reaction are removed from the chamber, leaving behind a dense, chemically bonded film. CVD is widely used in industries requiring precise and high-performance coatings, such as semiconductors, optics, and protective coatings.
Key Points Explained:
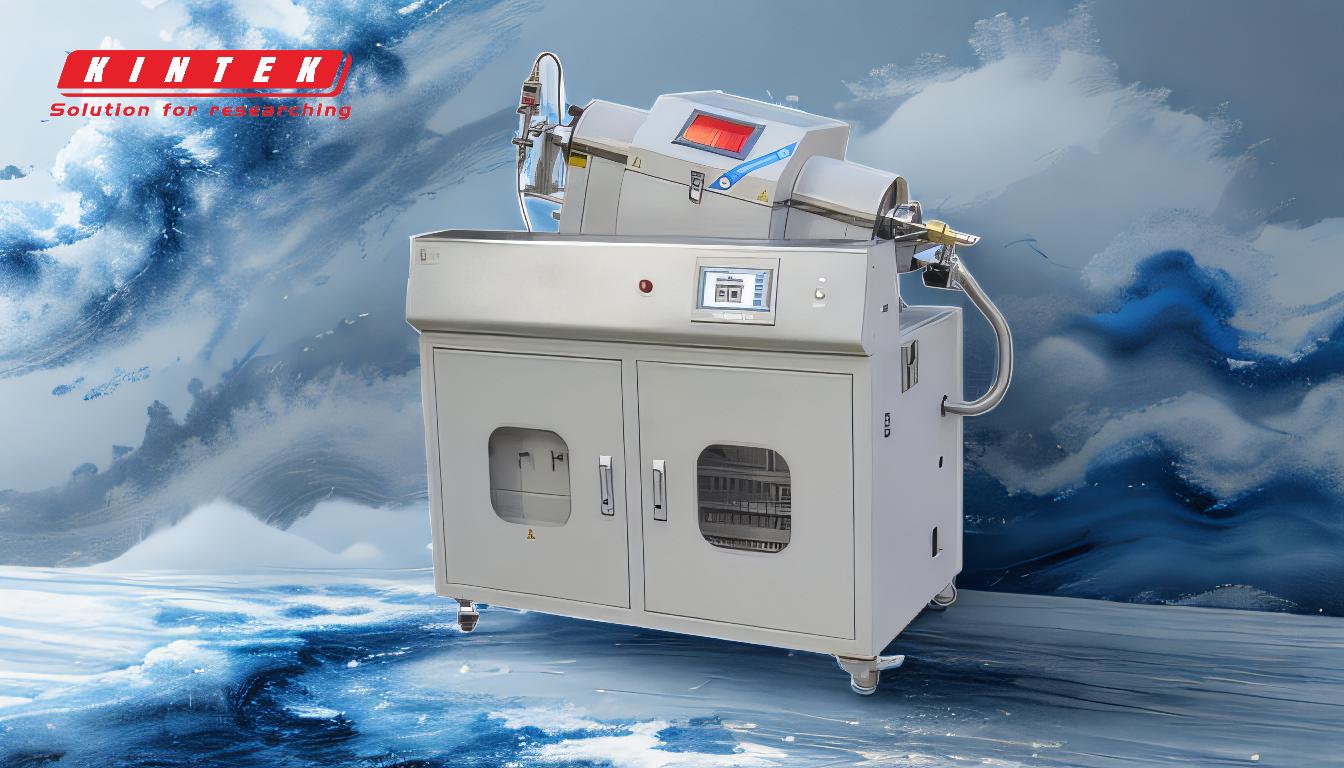
-
Introduction of Precursor Materials:
- CVD begins with the introduction of volatile precursor materials into a reaction chamber. These precursors are often in gaseous form and are chosen based on the desired material to be deposited.
- The precursors are typically mixed with carrier gases to facilitate their transport into the chamber.
-
Vaporization and Decomposition:
- Once inside the reaction chamber, the precursor materials are vaporized. This is usually achieved by heating the chamber to high temperatures, which causes the precursors to break down into their constituent atoms or molecules.
- The decomposition process is crucial as it releases the atoms that will eventually form the solid film on the substrate.
-
Chemical Reactions on the Substrate:
- The vaporized atoms or molecules then come into contact with the substrate, which is also heated to facilitate the chemical reactions.
- These reactions can take various forms, including surface reactions, where the atoms chemically bond with the substrate, or decomposition reactions, where the precursor molecules break down directly on the substrate surface.
-
Formation of the Thin Film:
- As the chemical reactions proceed, the atoms or molecules from the precursors begin to form a solid layer on the substrate. This layer grows atom by atom, resulting in a thin, uniform film.
- The film's properties, such as thickness, composition, and structure, can be precisely controlled by adjusting the process parameters, such as temperature, pressure, and flow rate of the precursors.
-
Removal of By-products:
- During the CVD process, volatile by-products are often generated as a result of the chemical reactions. These by-products need to be removed from the reaction chamber to prevent contamination and ensure the quality of the deposited film.
- This is typically achieved using vacuum pumps, which continuously evacuate the chamber, or by flowing inert gases through the chamber to carry away the by-products.
-
Variations in CVD Techniques:
- CVD can be performed using various techniques, depending on the specific requirements of the application. Some common variations include:
- Plasma-Enhanced CVD (PECVD): Uses plasma to enhance the chemical reactions, allowing for lower processing temperatures.
- Low-Pressure CVD (LPCVD): Operates at reduced pressures to improve film uniformity and reduce defects.
- Laser-Assisted CVD (LACVD): Uses laser irradiation to locally heat the substrate, enabling precise deposition in specific areas.
- Photochemical CVD: Utilizes light to initiate the chemical reactions, often at lower temperatures.
- CVD can be performed using various techniques, depending on the specific requirements of the application. Some common variations include:
-
Applications of CVD:
- CVD is widely used in various industries due to its ability to produce high-quality, high-performance materials. Some key applications include:
- Semiconductors: CVD is used to deposit thin films of silicon, silicon dioxide, and other materials in the fabrication of integrated circuits.
- Optics: CVD is employed to create anti-reflective coatings, mirrors, and other optical components.
- Protective Coatings: CVD is used to apply hard, wear-resistant coatings on tools and components.
- Energy: CVD is utilized in the production of solar cells, fuel cells, and batteries.
- CVD is widely used in various industries due to its ability to produce high-quality, high-performance materials. Some key applications include:
-
Advantages of CVD:
- High-Quality Films: CVD produces films with excellent purity, uniformity, and adhesion.
- Versatility: CVD can deposit a wide range of materials, including metals, ceramics, and polymers.
- Precision: The process allows for precise control over film thickness and composition.
- Scalability: CVD can be scaled up for large-area deposition, making it suitable for industrial applications.
-
Challenges and Considerations:
- High Temperatures: Many CVD processes require high temperatures, which can limit the types of substrates that can be used.
- Complexity: The process can be complex, requiring careful control of multiple parameters.
- Cost: CVD equipment and precursor materials can be expensive, making the process less suitable for low-cost applications.
In summary, CVD is a highly versatile and precise method for depositing thin films onto substrates. By carefully controlling the chemical reactions and process conditions, it is possible to produce high-quality materials with a wide range of applications. Despite some challenges, the benefits of CVD make it an essential tool in modern materials science and engineering.
Summary Table:
Key Aspect | Details |
---|---|
Process Overview | Deposits thin, high-quality solid films onto substrates using chemical reactions. |
Key Steps | 1. Introduction of precursor materials 2. Vaporization and decomposition 3. Chemical reactions on the substrate 4. Formation of thin film 5. Removal of by-products. |
Common CVD Techniques | Plasma-Enhanced CVD (PECVD), Low-Pressure CVD (LPCVD), Laser-Assisted CVD (LACVD), Photochemical CVD. |
Applications | Semiconductors, optics, protective coatings, energy (solar cells, fuel cells). |
Advantages | High-quality films, versatility, precision, scalability. |
Challenges | High temperatures, complexity, cost. |
Discover how CVD can enhance your material applications—contact our experts today for tailored solutions!