Atomic Layer Deposition (ALD) and Chemical Vapor Deposition (CVD) are both advanced techniques used to deposit thin films, but they differ significantly in their mechanisms, precision, and applications. ALD is a highly controlled process that deposits films layer by layer, offering exceptional uniformity and conformality, especially on complex geometries. It operates at lower temperatures and is ideal for applications requiring precise thickness control, such as in semiconductor manufacturing. CVD, on the other hand, relies on chemical reactions to deposit films in a more continuous manner, often at higher temperatures. It is widely used for creating thicker films and is suitable for applications like protective coatings and insulating layers. While ALD excels in precision and uniformity, CVD is more versatile for bulk film deposition.
Key Points Explained:
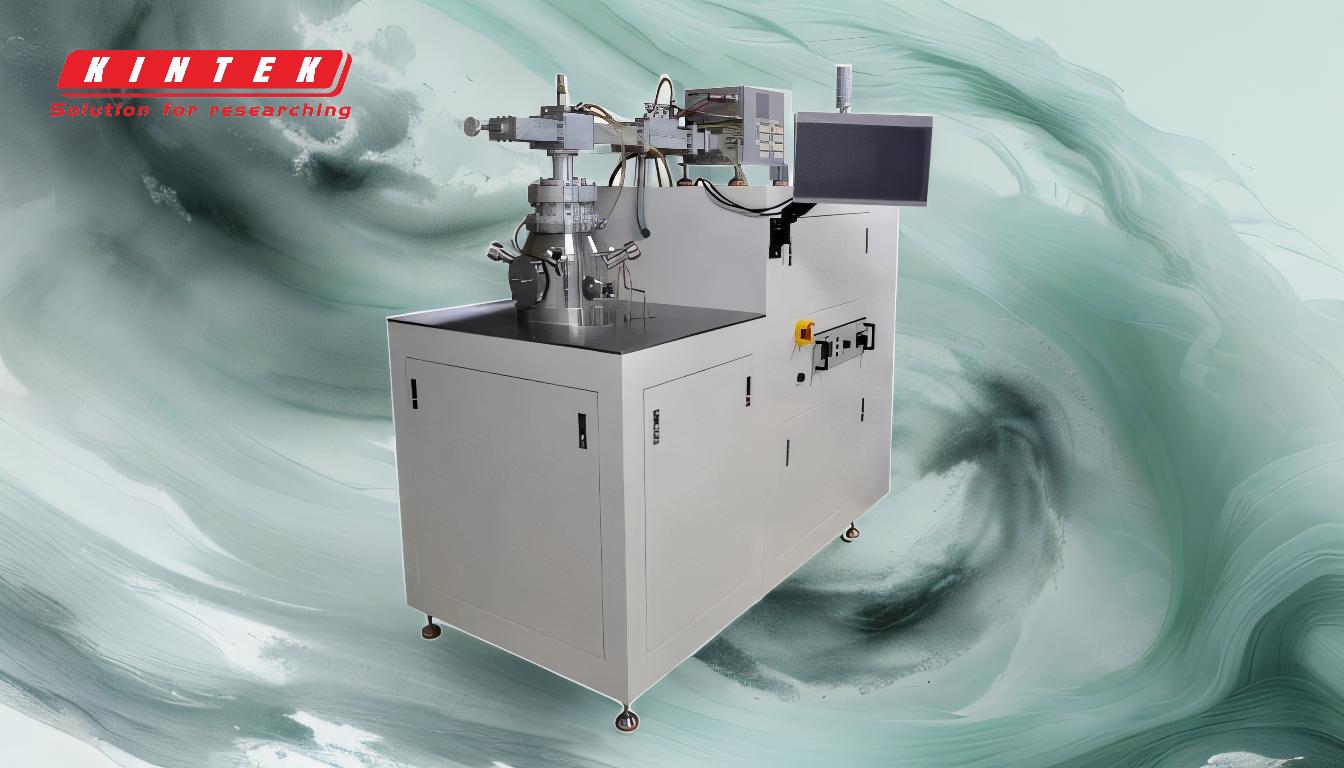
-
Mechanism of Deposition:
- ALD: ALD is a sequential process where thin films are deposited one atomic layer at a time. Each cycle involves exposing the substrate to a precursor gas, which chemically reacts with the surface, followed by a purge to remove excess reactants. This cycle is repeated to build up the film layer by layer, ensuring precise control over thickness and uniformity.
- CVD: CVD involves the continuous flow of precursor gases over the substrate, where they react and deposit a film. The process is driven by thermal, plasma, or light energy, and the film grows as a result of chemical reactions occurring on the substrate surface. It is less precise than ALD but can deposit thicker films more quickly.
-
Temperature Requirements:
- ALD: ALD typically operates at lower temperatures, making it suitable for temperature-sensitive substrates. This is particularly advantageous in semiconductor and nanotechnology applications where high temperatures could damage delicate components.
- CVD: CVD often requires higher temperatures to facilitate the chemical reactions necessary for film deposition. However, plasma-enhanced CVD (PECVD) allows for lower temperature operations by using plasma to energize the precursor gases.
-
Uniformity and Conformality:
- ALD: ALD is renowned for its ability to produce highly uniform and conformal films, even on complex geometries, curved surfaces, and nanoparticles. This makes it ideal for applications requiring precise film thickness and coverage, such as transistor gate dielectric layers.
- CVD: While CVD can produce uniform films, it is less effective at achieving the same level of conformality as ALD, especially on highly complex or three-dimensional structures.
-
Applications:
- ALD: ALD is primarily used in applications requiring ultra-thin, precise, and uniform films, such as in semiconductor manufacturing, nanotechnology, and advanced materials science. It is particularly valuable for creating multi-layer structures and coatings on intricate surfaces.
- CVD: CVD is more versatile and is used in a wide range of applications, including protective coatings, insulating films, and wiring layers. It is suitable for depositing thicker films and is commonly used in industries like electronics, optics, and energy.
-
Process Complexity and Control:
- ALD: ALD is a highly controlled process that requires careful monitoring and expertise. The sequential nature of the process allows for precise control over film thickness and composition, but it can be slower and more complex to implement.
- CVD: CVD is generally simpler and faster than ALD, making it more suitable for large-scale production. However, it offers less control over film thickness and uniformity compared to ALD.
-
Material Compatibility:
- ALD: ALD is compatible with a wide range of materials, including metals, oxides, and nitrides. Its ability to deposit films at low temperatures makes it suitable for temperature-sensitive materials.
- CVD: CVD is also compatible with a broad range of materials, but the higher temperatures required for some CVD processes may limit its use with certain substrates.
In summary, ALD and CVD are complementary techniques, each with its own strengths and limitations. ALD excels in precision and uniformity, making it ideal for advanced applications requiring ultra-thin films, while CVD offers versatility and speed, making it suitable for a broader range of industrial applications.
Summary Table:
Aspect | ALD | CVD |
---|---|---|
Deposition Mechanism | Sequential, layer-by-layer deposition | Continuous, chemical reaction-driven deposition |
Temperature | Lower temperatures, suitable for sensitive substrates | Higher temperatures (except PECVD) |
Uniformity | Exceptional uniformity and conformality on complex geometries | Uniform but less conformal on complex structures |
Applications | Semiconductor manufacturing, nanotechnology, precise thin films | Protective coatings, insulating layers, thicker films |
Process Control | Highly controlled, precise thickness and composition | Simpler and faster, less precise |
Material Compatibility | Wide range, including metals, oxides, and nitrides | Broad range but limited by higher temperatures in some cases |
Need help choosing between ALD and CVD for your application? Contact our experts today!