DLC (Diamond-Like Carbon) coatings are versatile and widely used across multiple industries due to their unique combination of properties, such as high hardness, wear resistance, low friction, chemical inertness, and biocompatibility. These coatings are applied to enhance the performance and durability of components in tribological systems, high-precision tools, medical devices, and decorative applications. They are also used in optical and sensing applications, where precise control of thickness and refractive index is required. DLC coatings are produced using techniques like PACVD (Plasma-Assisted Chemical Vapor Deposition) and PECVD (Plasma-Enhanced Chemical Vapor Deposition), which offer advantages such as low deposition temperatures and high deposition rates.
Key Points Explained:
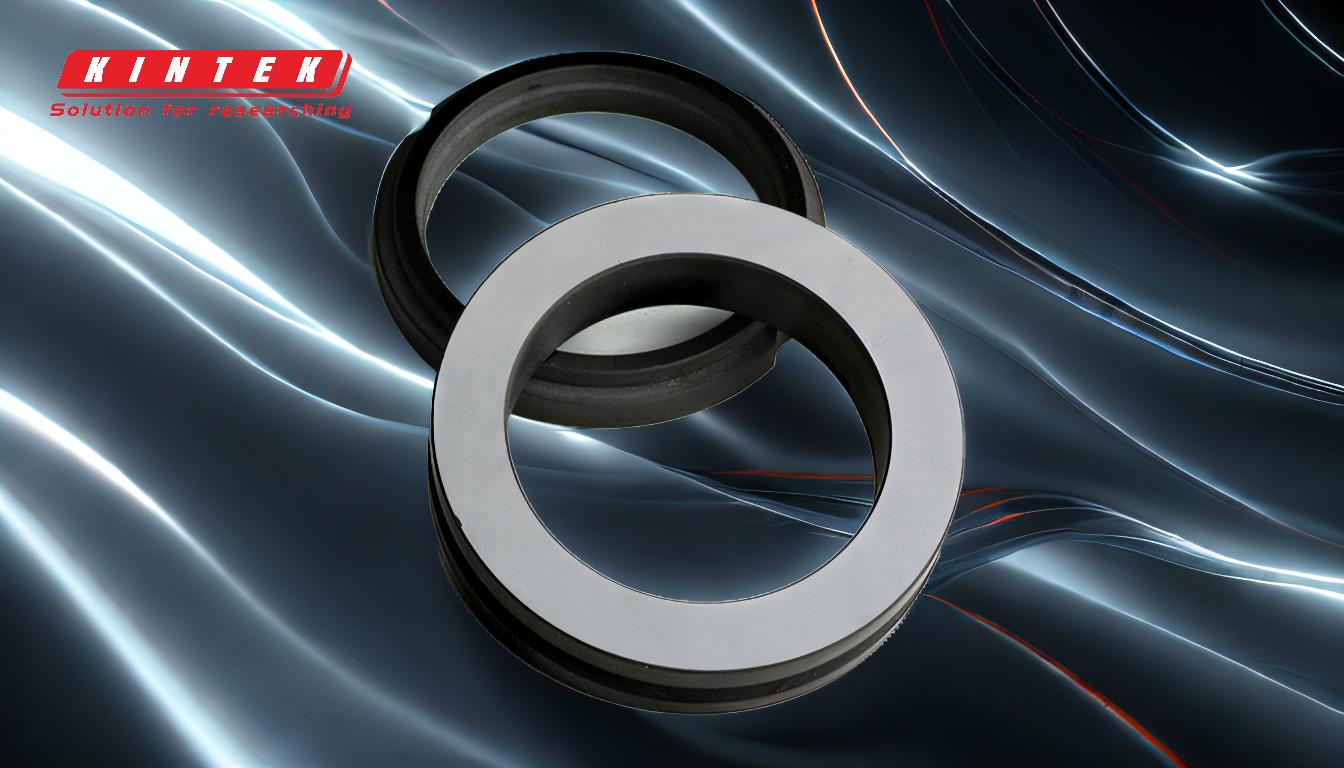
-
Tribological Systems in Engines and Machinery
- DLC coatings are ideal for components with sliding and rolling movements, such as engine parts, machine assemblies, and mechanical systems.
- Their excellent hardness, wear resistance, and low friction properties reduce wear and tear, extending the lifespan of these components.
- Examples include automobile pistons, bores, VCR heads, and textile machinery components.
-
High-Precision Injection Molding Tools
- DLC coatings are used on tools for injection molding to improve their durability and performance.
- The coatings reduce friction and wear, ensuring precise and consistent molding results over extended periods.
-
Decorative Applications
- DLC coatings are used for decorative purposes, particularly in black finishes, due to their aesthetic appeal and special hardness characteristics.
- These coatings are often applied to luxury items, watches, and other consumer products.
-
Medical Components and Implants
- The chemical inertness and biocompatibility of DLC coatings make them suitable for medical applications.
- They are used on surgical tools, implants, and prostheses to reduce wear, prevent corrosion, and ensure compatibility with human tissues.
-
Optical and Sensing Applications
- DLC coatings are used as antireflective coatings and in optical sensing applications.
- Their precise control over thickness and refractive index makes them ideal for enhancing the performance of optical components.
-
Wear-Protective Applications
- DLC coatings are applied to protect optical components, magnetic memory discs, and metalworking tools from wear and damage.
- Their high hardness and scratch resistance ensure long-lasting performance in demanding environments.
-
Barrier Packaging Films
- PECVD-produced DLC coatings are explored for use in barrier packaging films due to their chemical stability and good barrier properties.
- Challenges remain in scaling this technology for high-speed coating applications in the packaging industry.
-
Advantages of PECVD for DLC Coatings
- PECVD allows for low-temperature deposition, making it suitable for coating temperature-sensitive materials like polymers.
- It offers quick processing times, high deposition rates, and fewer toxic byproducts, making it an environmentally friendly option.
In summary, DLC coatings are a critical technology for improving the performance, durability, and functionality of components across a wide range of industries, from automotive and manufacturing to medical and optical applications. Their unique properties make them indispensable in modern engineering and design.
Summary Table:
Application | Key Benefits |
---|---|
Tribological Systems | High hardness, wear resistance, low friction, extended component lifespan |
High-Precision Tools | Reduced friction, improved durability, consistent molding results |
Decorative Applications | Aesthetic black finish, special hardness characteristics |
Medical Components | Biocompatibility, corrosion resistance, wear reduction |
Optical and Sensing | Precise thickness control, antireflective properties |
Wear-Protective Applications | Scratch resistance, long-lasting performance in demanding environments |
Barrier Packaging Films | Chemical stability, good barrier properties |
PECVD Advantages | Low-temperature deposition, high deposition rates, environmentally friendly |
Learn how DLC coatings can transform your industry—contact our experts today!