E-beam evaporation is a versatile and highly efficient thin-film deposition technique widely used in various industries. It involves using a focused electron beam to heat and evaporate a source material, which then condenses onto a substrate to form a thin film. This method is particularly valued for its high deposition rates, excellent film purity, and ability to deposit a wide range of materials. It is commonly employed in applications such as laser optics, solar panels, eyeglasses, architectural glass, and precision optical coatings. Despite its limitations, such as being a line-of-sight process and potential energy loss due to secondary electron emission, e-beam evaporation remains a preferred choice for high-quality, high-throughput thin-film production.
Key Points Explained:
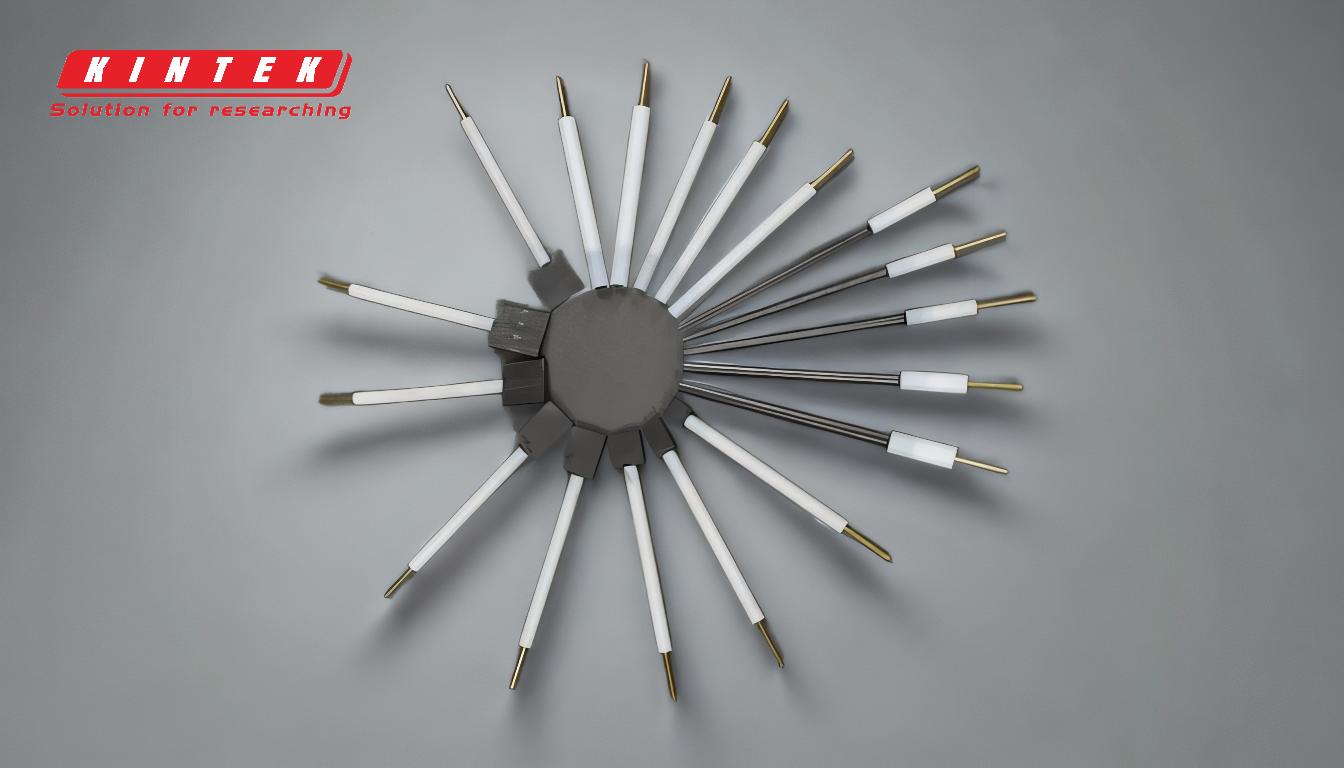
-
High Deposition Rates:
- E-beam evaporation offers rapid vapor deposition rates, ranging from 0.1 μm/min to 100 μm/min. This makes it highly efficient for applications requiring quick and consistent film formation, such as in high-volume batch production.
-
High-Purity Films:
- The process minimizes contamination risks, resulting in high-purity films. This is crucial for applications like precision optical coatings and laser optics, where even minor impurities can significantly affect performance.
-
Multi-Layer Deposition:
- E-beam evaporation allows for multi-layer deposition without the need for venting the vacuum chamber. This capability is essential for creating complex, multi-functional coatings in applications such as solar panels and architectural glass.
-
Material Compatibility:
- The technique is compatible with a wide variety of materials, including metals, ceramics, and semiconductors. This versatility makes it suitable for diverse applications, from metallization to lift-off processes.
-
High Material Utilization Efficiency:
- E-beam evaporation is known for its high material utilization efficiency, ensuring that a significant portion of the source material is effectively deposited onto the substrate. This reduces waste and lowers production costs.
-
Line-of-Sight Limitation:
- As a line-of-sight deposition method, e-beam evaporation is unsuitable for coating the inner surfaces of complex geometries. This limitation must be considered when designing components for specific applications.
-
Energy Loss and Filament Degradation:
- The process can lead to energy loss due to secondary electron emission and X-ray production. Additionally, filament degradation over time can cause inconsistent evaporation rates, necessitating regular maintenance and monitoring.
-
Special Films for Optical Components:
- E-beam evaporation can add special films onto optical components, adapting the substrate's properties to meet specific requirements. This is particularly useful in the production of eyeglasses and other optical devices.
-
System Components:
- The e-beam evaporation system consists of a vacuum chamber, an electron beam source, and a crucible to hold the source material. The electron beam source, typically made from tungsten, is heated to over 2,000 degrees Celsius to generate electrons. Magnets focus these electrons into a beam directed at the crucible, which is water-cooled to prevent melting and contamination.
-
Benefits of E-beam Evaporation:
- The technique offers several benefits, including low impurity levels, good directionality, high deposition rates, high throughput, and excellent uniformity when using masks and planetary systems. These advantages make it a preferred method for various industrial applications.
-
Common Applications:
- Common uses of e-beam evaporation include applications in laser optics, solar panels, eyeglasses, architectural glass, high-volume batch production, metallization, lift-off, and precision optical coatings. Each of these applications benefits from the unique advantages offered by e-beam evaporation.
By understanding these key points, equipment and consumable purchasers can make informed decisions about when and how to utilize e-beam evaporation technology to meet their specific needs.
Summary Table:
Key Aspect | Details |
---|---|
High Deposition Rates | 0.1–100 μm/min, ideal for high-volume batch production. |
High-Purity Films | Minimal contamination, crucial for precision optical coatings. |
Multi-Layer Deposition | No venting required, suitable for solar panels and architectural glass. |
Material Compatibility | Works with metals, ceramics, and semiconductors. |
Applications | Laser optics, solar panels, eyeglasses, architectural glass, and more. |
Limitations | Line-of-sight process, energy loss, and filament degradation. |
Interested in leveraging e-beam evaporation for your projects? Contact our experts today to learn more!