Evaporation and sputtering are two widely used physical vapor deposition (PVD) techniques for creating thin films on substrates. Evaporation involves heating a material in a vacuum until it vaporizes, allowing the vapor to condense on a substrate. Sputtering, on the other hand, uses high-energy ions to bombard a target material, ejecting atoms that then deposit onto the substrate. Both methods are essential in industries like semiconductors, optics, and solar panels, but they differ significantly in their mechanisms, advantages, and applications.
Key Points Explained:
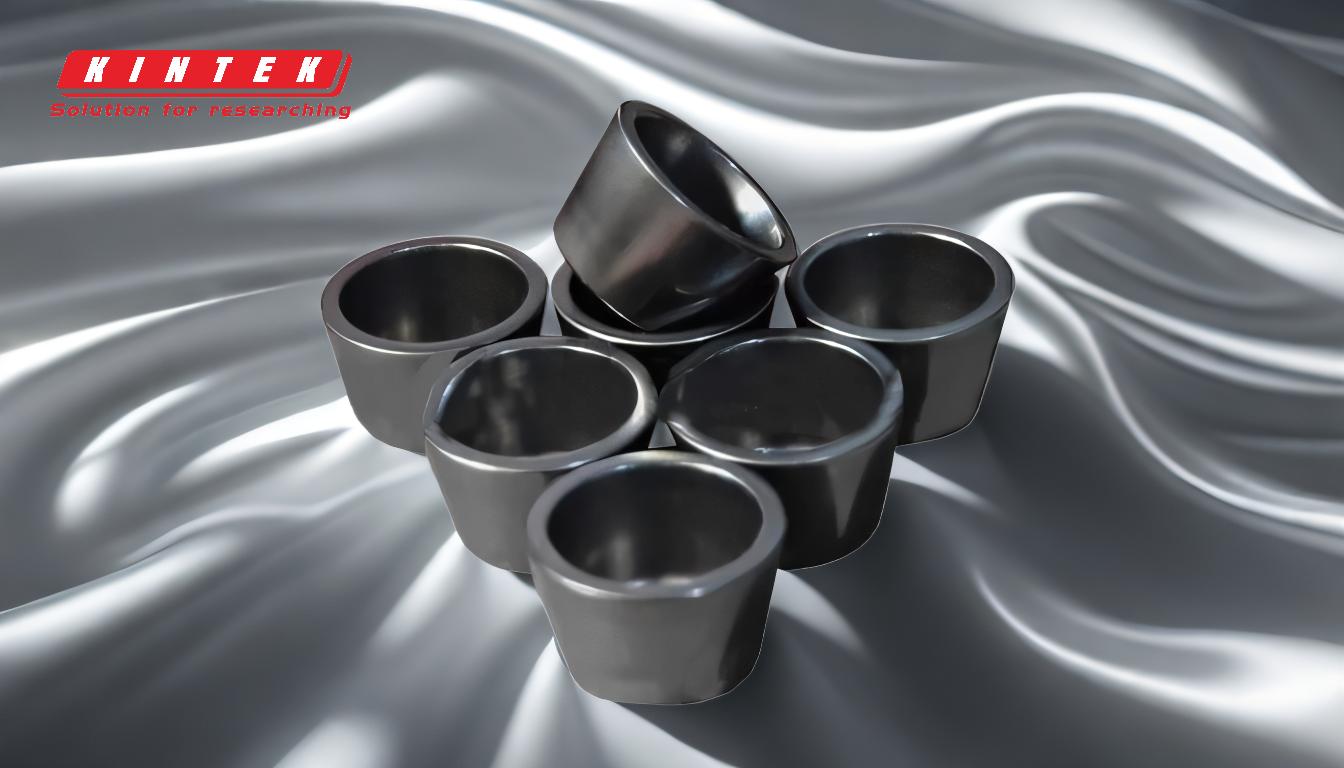
-
Mechanism of Evaporation:
- Evaporation relies on heating a material in a vacuum until it reaches its vaporization point.
- The vaporized material travels through the vacuum and condenses on the substrate, forming a thin film.
- This method is typically used for materials with low melting points and is known for its high deposition rates.
-
Mechanism of Sputtering:
- Sputtering involves bombarding a target material with high-energy ions, usually from an inert gas like argon.
- The collision between ions and the target ejects atoms from the target, which then deposit onto the substrate.
- This process occurs in a vacuum chamber with a controlled atmosphere, often involving a plasma discharge.
-
Vacuum Requirements:
- Evaporation requires a high vacuum to minimize contamination and ensure efficient vapor travel.
- Sputtering operates at lower vacuum levels, making it more versatile for certain applications.
-
Deposition Rate:
- Evaporation generally offers higher deposition rates, making it suitable for applications requiring thick coatings.
- Sputtering has a lower deposition rate, except for pure metals, but provides better control over film thickness.
-
Film Quality and Adhesion:
- Sputtering produces films with better adhesion and homogeneity due to the high energy of deposited atoms.
- Evaporation films may have lower adhesion and less uniformity but are often smoother.
-
Energy of Deposited Species:
- Sputtered atoms have higher kinetic energy, leading to denser films and better step coverage.
- Evaporated atoms have lower energy, which can result in less dense films and poorer step coverage.
-
Grain Size and Film Structure:
- Sputtering typically results in smaller grain sizes, which can enhance film properties like hardness and wear resistance.
- Evaporation tends to produce larger grain sizes, which may be beneficial for certain optical or electrical applications.
-
Applications:
- Evaporation is commonly used for optical coatings, decorative finishes, and some semiconductor applications.
- Sputtering is preferred for applications requiring high adhesion, uniform coatings, and precise control, such as in microelectronics and solar panels.
-
Advantages of Sputtering:
- Better adhesion and film uniformity.
- Ability to deposit a wide range of materials, including alloys and compounds.
- Lower deposition temperatures, reducing thermal stress on substrates.
-
Advantages of Evaporation:
- High deposition rates for faster processing.
- Simplicity and cost-effectiveness for certain materials.
- Suitable for materials with low melting points.
-
Challenges:
- Sputtering can be more complex and expensive due to the need for plasma generation and precise control.
- Evaporation may struggle with step coverage and adhesion for complex geometries.
By understanding these key differences, equipment and consumable purchasers can make informed decisions about which technique best suits their specific application needs.
Summary Table:
Aspect | Evaporation | Sputtering |
---|---|---|
Mechanism | Heating material in a vacuum until it vaporizes and condenses on a substrate. | Bombarding target material with high-energy ions to eject and deposit atoms. |
Vacuum Level | High vacuum required. | Lower vacuum levels, more versatile. |
Deposition Rate | Higher rates, suitable for thick coatings. | Lower rates, except for pure metals; better thickness control. |
Film Quality | Smoother films, lower adhesion and uniformity. | Better adhesion, homogeneity, and denser films. |
Energy of Atoms | Lower energy, less dense films, poorer step coverage. | Higher energy, denser films, better step coverage. |
Grain Size | Larger grains, beneficial for optical/electrical applications. | Smaller grains, enhancing hardness and wear resistance. |
Applications | Optical coatings, decorative finishes, some semiconductors. | Microelectronics, solar panels, applications requiring precise control. |
Advantages | High deposition rates, cost-effective, suitable for low melting point materials. | Better adhesion, uniformity, lower deposition temperatures, versatile material use. |
Challenges | Poor step coverage, lower adhesion for complex geometries. | Complex and expensive setup, requires precise control. |
Need help choosing between evaporation and sputtering for your application? Contact our experts today!