Firing and sintering are heat treatment processes used to compact and solidify materials, particularly ceramics and metals. While both involve heating materials to high temperatures, they differ in complexity, energy requirements, and applications. Firing is typically used for complex processes, such as traditional clay ceramics, where undefined parameters influence the final product. Sintering, on the other hand, is a more controlled process that occurs at lower temperatures than melting, relying on atomic diffusion to fuse particles without liquefaction. It is commonly used for materials with high melting points, such as tungsten and molybdenum. Both processes aim to create solid, durable materials, but their mechanisms and applications vary significantly.
Key Points Explained:
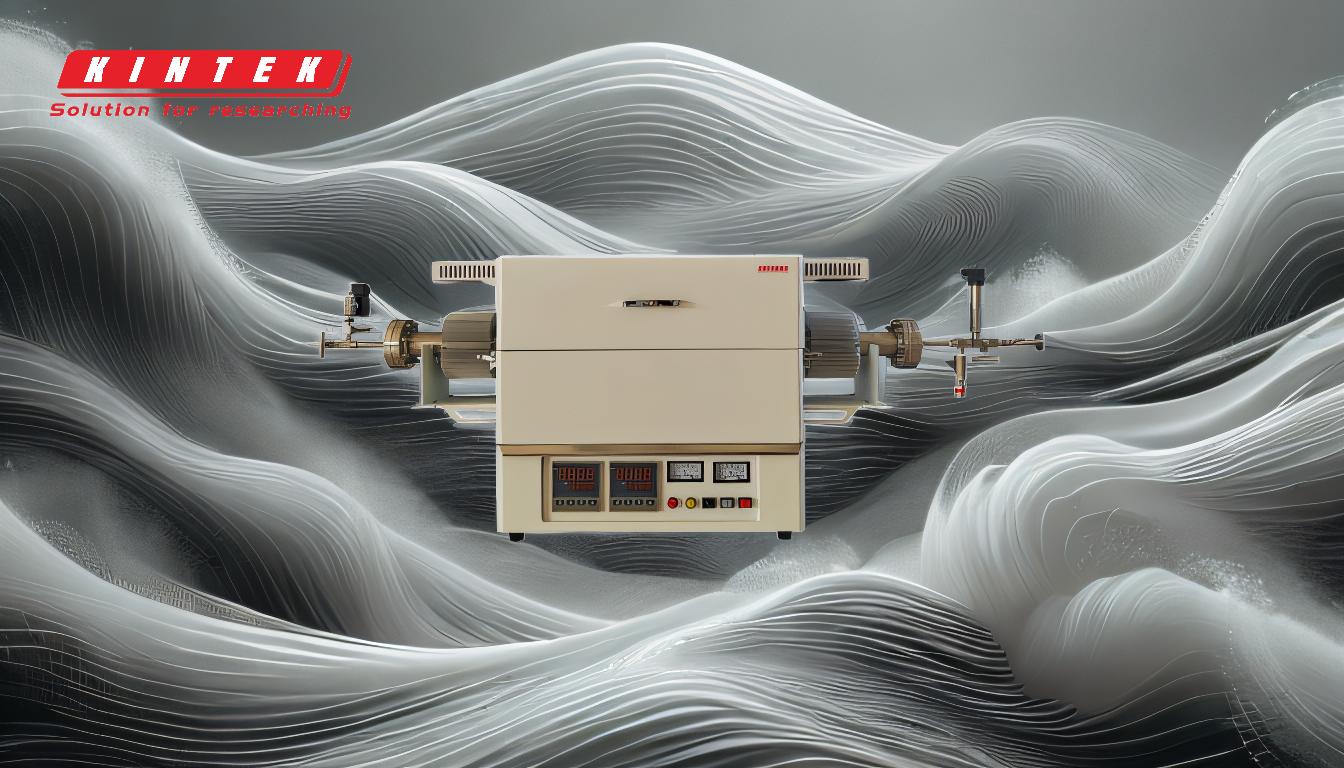
-
Definition and Purpose of Firing and Sintering:
- Firing: A heat treatment process used primarily for ceramics, where complex chemical and physical changes occur during heating. It is often applied to traditional clay ceramics or materials with undefined parameters affecting the final product.
- Sintering: A process that compacts and forms solid materials by heating or applying pressure without reaching the melting point. It relies on atomic diffusion to fuse particles, making it suitable for materials with high melting points.
-
Mechanisms of Firing and Sintering:
- Firing: Involves multiple stages, starting with the formation of neck connections between powder particles and ending with the elimination of small pores. The diffusion of atoms drives the disappearance of interfaces between particles.
- Sintering: Occurs at lower temperatures than melting, making it energy-efficient. Atoms diffuse across particle boundaries, fusing them into a single solid piece without liquefaction.
-
Applications of Firing and Sintering:
- Firing: Commonly used in traditional ceramics, pottery, and complex material processing where the final properties are influenced by numerous factors.
- Sintering: Ideal for materials with extremely high melting points, such as tungsten, molybdenum, and advanced ceramics. It is also used in powder metallurgy to create durable metal components.
-
Energy Requirements:
- Firing: Typically requires higher energy due to the complex and often undefined nature of the processes involved.
- Sintering: Consumes less energy because it operates at lower temperatures and involves more controlled conditions.
-
Process Complexity:
- Firing: Characterized by complex and often undefined parameters, making it less predictable and more challenging to control.
- Sintering: Features clearly defined and controllable parameters, making it a more straightforward and predictable process.
-
Material Suitability:
- Firing: Best suited for materials that undergo significant chemical and physical transformations during heating, such as clay-based ceramics.
- Sintering: Ideal for materials that require solidification without melting, particularly those with high melting points or in powder metallurgy applications.
By understanding these key points, equipment and consumable purchasers can make informed decisions about which process is best suited for their specific material and application needs.
Summary Table:
Aspect | Firing | Sintering |
---|---|---|
Definition | Heat treatment for ceramics with complex chemical changes. | Compacts materials without melting, relying on atomic diffusion. |
Mechanism | Multiple stages, including neck formation and pore elimination. | Lower temperatures, energy-efficient, fuses particles without liquefaction. |
Applications | Traditional ceramics, pottery, complex material processing. | High-melting-point materials (e.g., tungsten, molybdenum), powder metallurgy. |
Energy Requirements | Higher energy due to complex processes. | Lower energy due to controlled conditions and lower temperatures. |
Process Complexity | Complex, undefined parameters, less predictable. | Controlled, defined parameters, straightforward. |
Material Suitability | Best for clay-based ceramics with significant transformations. | Ideal for high-melting-point materials and powder metallurgy. |
Need help choosing the right process for your materials? Contact our experts today!