Forging in a hydraulic press involves shaping metal using compressive forces generated by a hydraulic system. This process is widely used in industries to produce high-strength components with precise dimensions. Hydraulic presses are versatile and can handle both small-scale and large-scale manufacturing tasks, making them essential in various applications, including industrial XRF, laboratory sample manipulation, and polymer processing.
Key Points Explained:
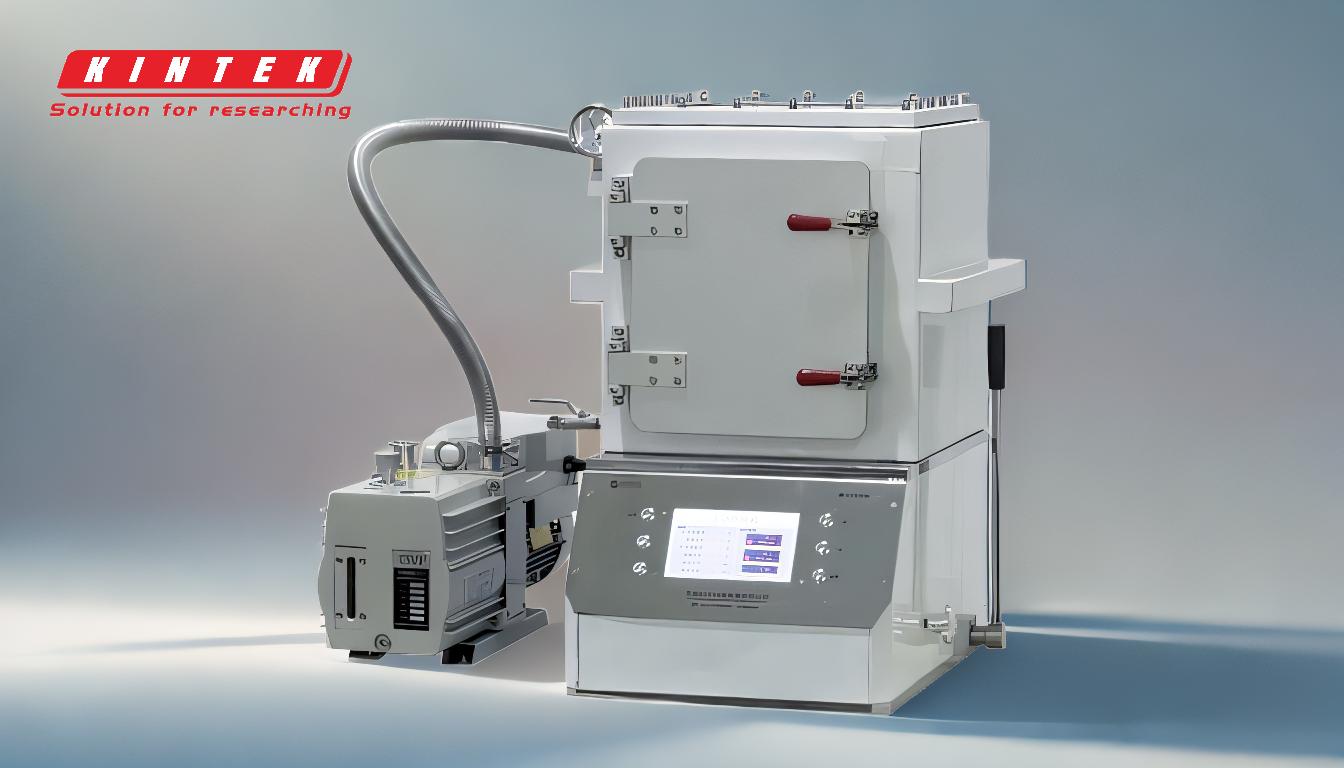
-
What is Forging in a Hydraulic Press?
- Forging is a manufacturing process where metal is shaped using compressive forces. In a hydraulic press, these forces are generated by a hydraulic system, which uses fluid pressure to move a piston and apply force to the workpiece.
- The process is typically performed at high temperatures (hot forging) to make the metal more malleable, but it can also be done at room temperature (cold forging) for certain materials.
-
Applications of Hydraulic Presses in Forging
- Hydraulic presses are used in various industries for forging operations. They are particularly effective in producing high-strength components with precise dimensions.
- Common applications include:
- Industrial XRF Applications: Used for preparing samples for X-ray fluorescence analysis.
- Laboratory Sample Manipulation: Ideal for creating uniform samples for testing and analysis.
- Hot Embossing and Laminating: Used in the production of thin films and laminated materials.
- Melting Polymers: Suitable for processing polymers into thin films or other shapes.
-
Advantages of Using a Hydraulic Hot Press Machine
- Precision and Control: Hydraulic presses offer precise control over the force and speed of the press, ensuring consistent results.
- Versatility: They can handle a wide range of materials and applications, from metals to polymers.
- Scalability: Suitable for both small-scale laboratory work and large-scale industrial production.
- Durability: Hydraulic systems are robust and can withstand high pressures, making them ideal for demanding forging operations.
-
How Hydraulic Presses Work in Forging
- The hydraulic press consists of a cylinder filled with hydraulic fluid, a piston, and a ram. When hydraulic pressure is applied, the piston moves, driving the ram to apply force to the workpiece.
- The force can be adjusted by controlling the pressure of the hydraulic fluid, allowing for precise control over the forging process.
- In hot forging, the workpiece is heated to a high temperature to reduce its strength and increase its malleability, making it easier to shape.
-
Considerations for Purchasing a Hydraulic Hot Press Machine
- Capacity: Ensure the press has the necessary force capacity for your specific forging needs.
- Temperature Control: For hot forging, the press should have reliable temperature control mechanisms.
- Size and Footprint: Consider the space available in your facility and choose a press that fits comfortably.
- Maintenance and Durability: Look for a machine with a robust design and easy maintenance features to ensure long-term reliability.
For more detailed information on hydraulic hot press machine, you can explore its applications and benefits in various industries.
Summary Table:
Aspect | Details |
---|---|
Process | Shaping metal using compressive forces generated by a hydraulic system. |
Applications | Industrial XRF, lab sample manipulation, hot embossing, polymer processing. |
Advantages | Precision, versatility, scalability, and durability. |
Key Considerations | Capacity, temperature control, size, maintenance, and durability. |
Ready to enhance your forging processes? Contact us today to find the perfect hydraulic press for your needs!