Frequency in induction hardening refers to the rate at which the alternating current (AC) oscillates within the induction coil, measured in Hertz (Hz). It plays a critical role in determining the depth of heating and hardening in the workpiece. Higher frequencies result in a thinner heating layer due to the skin effect, where current density is higher on the surface and decreases toward the interior. This allows for precise control over the hardened layer depth, making induction hardening a versatile and efficient heat treatment method for achieving surface hardening.
Key Points Explained:
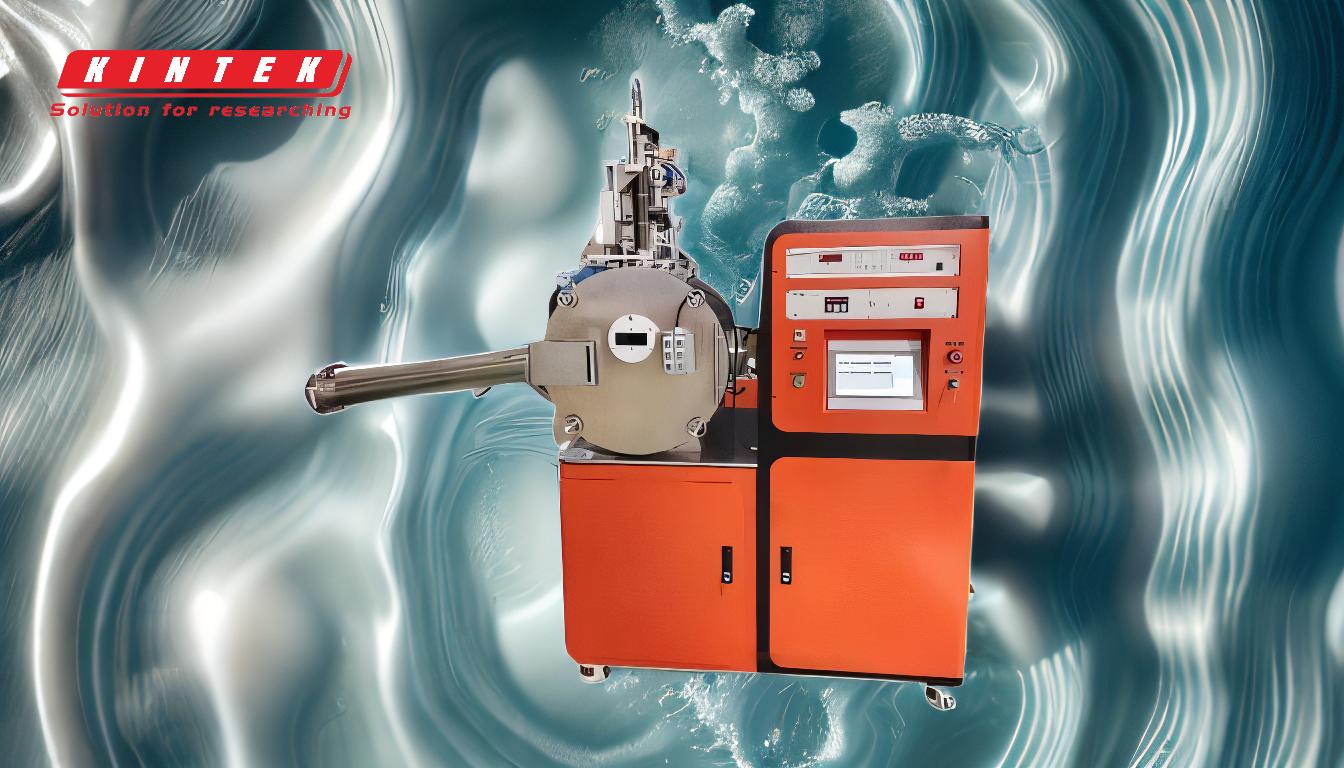
-
Definition of Frequency in Induction Hardening:
- Frequency refers to the oscillation rate of the alternating current (AC) used in the induction coil, measured in Hertz (Hz).
- It directly influences the depth of current penetration and heat generation in the workpiece.
-
Skin Effect and Current Density:
- The skin effect is a phenomenon where alternating current tends to flow near the surface of a conductor at higher frequencies.
- Higher frequencies result in a greater current density difference between the surface and the interior of the workpiece.
- This leads to a thinner heating layer on the surface, which is ideal for applications requiring shallow hardening.
-
Relationship Between Frequency and Heating Depth:
- Higher frequencies produce shallower heating depths, making them suitable for thin or small components.
- Lower frequencies allow deeper penetration, making them ideal for thicker or larger workpieces.
- This adjustability is a key advantage of induction hardening, as it allows precise control over the hardened layer depth.
-
Critical Temperature and Rapid Cooling:
- When the heating layer reaches the critical temperature (the point at which steel transforms into austenite), rapid cooling (quenching) is applied.
- This process locks in the hardened microstructure, resulting in a durable and wear-resistant surface.
-
Applications of Frequency Adjustment:
- High-frequency induction hardening is used for thin layers, such as gears, bearings, and small tools.
- Medium and low frequencies are employed for deeper hardening in larger components like shafts or heavy machinery parts.
-
Advantages of Induction Hardening:
- Precise control over hardening depth through frequency adjustment.
- Energy-efficient and localized heating, reducing distortion and energy consumption.
- Faster processing times compared to traditional heat treatment methods.
By understanding the role of frequency in induction hardening, manufacturers can optimize the process for specific applications, ensuring the desired hardness and durability of the workpiece surface.
Summary Table:
Aspect | Details |
---|---|
Frequency Definition | Oscillation rate of AC in the induction coil, measured in Hertz (Hz). |
Skin Effect | Higher frequencies create thinner heating layers due to surface current flow. |
Heating Depth Control | High frequency = shallow heating; low frequency = deeper penetration. |
Critical Temperature | Rapid cooling locks in hardened microstructure for wear resistance. |
Applications | High frequency: gears, bearings; low frequency: shafts, heavy machinery. |
Advantages | Precise control, energy efficiency, faster processing. |
Optimize your induction hardening process—contact our experts today for tailored solutions!