Furnace calibration is a critical process that ensures the accuracy and reliability of temperature measurements within a furnace. It involves comparing the furnace's temperature readings to a known standard, typically using a calibrated reference thermometer or thermocouple. The goal is to identify and correct any discrepancies in the furnace's temperature control system, ensuring that it operates within the specified tolerances. Calibration is essential for maintaining consistency in processes such as heat treatment, material testing, and laboratory experiments, where precise temperature control is crucial. Regular calibration helps prevent errors, ensures compliance with industry standards, and extends the lifespan of the furnace.
Key Points Explained:
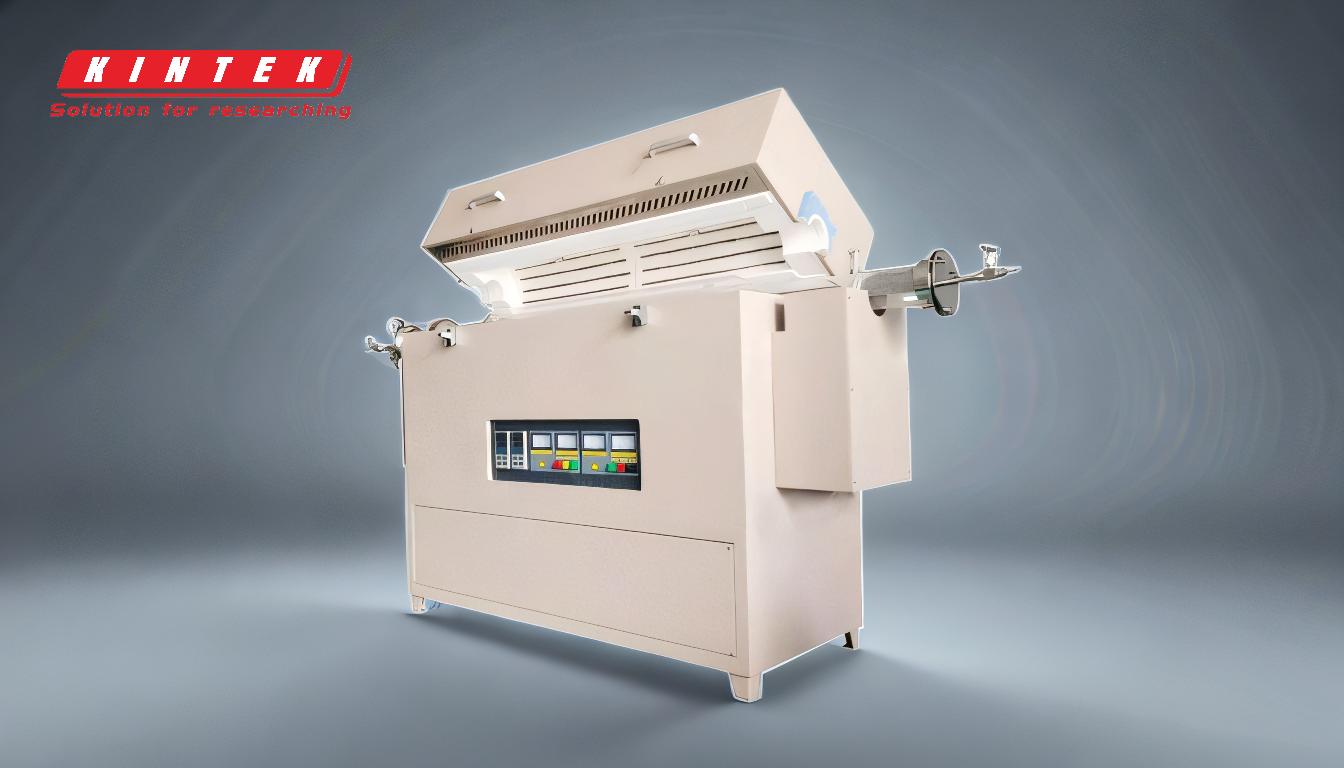
-
Definition of Furnace Calibration:
- Furnace calibration is the process of verifying and adjusting the temperature readings of a furnace to ensure they match a known standard. This involves using calibrated reference instruments, such as thermocouples or resistance temperature detectors (RTDs), to measure the actual temperature inside the furnace and compare it to the furnace's displayed or set temperature.
-
Importance of Furnace Calibration:
- Accuracy: Ensures that the furnace operates at the correct temperature, which is critical for processes like heat treatment, sintering, or annealing.
- Consistency: Maintains uniform temperature distribution within the furnace, preventing variations that could affect the quality of the output.
- Compliance: Meets industry standards and regulatory requirements, such as ISO 9001 or ASTM E220, which mandate regular calibration of equipment.
- Prevention of Errors: Reduces the risk of underheating or overheating, which can lead to product defects or equipment damage.
-
Steps Involved in Furnace Calibration:
- Preparation: Ensure the furnace is clean and free of debris. Select appropriate reference instruments with a known calibration status.
- Measurement Placement: Insert the reference thermometer or thermocouple into the furnace at the same location where the furnace's temperature sensor is placed.
- Temperature Comparison: Heat the furnace to specific setpoints and compare the readings from the reference instrument to the furnace's display or control system.
- Adjustment: If discrepancies are found, adjust the furnace's temperature control system to align with the reference instrument's readings.
- Documentation: Record the calibration results, including any adjustments made, for future reference and compliance purposes.
-
Frequency of Calibration:
- The frequency of furnace calibration depends on several factors, including the type of furnace, its usage intensity, and the criticality of the processes it supports. High-use furnaces or those used in precision applications may require calibration monthly or quarterly, while less critical applications may only need annual calibration.
-
Tools and Equipment Used:
- Reference Thermometers: High-precision instruments used to measure the actual temperature inside the furnace.
- Thermocouples: Temperature sensors that provide real-time readings and can be placed at multiple points within the furnace to check for uniformity.
- Data Loggers: Devices that record temperature data over time, useful for identifying trends or inconsistencies.
-
Challenges in Furnace Calibration:
- Temperature Uniformity: Ensuring that the entire furnace chamber reaches and maintains the target temperature uniformly.
- Sensor Placement: Proper placement of reference sensors is crucial to obtain accurate readings.
- Environmental Factors: External conditions, such as ambient temperature or airflow, can affect calibration results.
-
Benefits of Regular Calibration:
- Improved Product Quality: Ensures that materials are processed at the correct temperatures, leading to better-quality outputs.
- Cost Savings: Prevents costly errors and reduces the need for rework or scrapped materials.
- Extended Equipment Life: Regular maintenance and calibration can prolong the lifespan of the furnace by preventing overheating or other operational issues.
By understanding and implementing proper furnace calibration practices, users can ensure the reliability and accuracy of their equipment, leading to better outcomes and compliance with industry standards.
Summary Table:
Aspect | Details |
---|---|
Definition | Verifying and adjusting furnace temperature readings to match known standards. |
Importance | Ensures accuracy, consistency, compliance, and prevents errors. |
Steps | Preparation, measurement placement, temperature comparison, adjustment, and documentation. |
Frequency | Monthly/quarterly for high-use furnaces; annually for less critical applications. |
Tools Used | Reference thermometers, thermocouples, and data loggers. |
Challenges | Temperature uniformity, sensor placement, and environmental factors. |
Benefits | Improved product quality, cost savings, and extended equipment life. |
Ensure your furnace operates at peak performance—contact our experts today for calibration services!