Hot isostatic pressing (HIP) is a manufacturing process that combines high temperature and isostatic pressure to densify materials, eliminate defects, and improve mechanical properties. It is widely used in industries such as aerospace, automotive, and medical devices to produce high-performance components with superior structural integrity. The process involves placing materials in a high-pressure vessel filled with an inert gas, typically argon, and subjecting them to uniform pressure from all directions while heating. This results in dense, void-free products with enhanced properties like hardness, wear resistance, and fatigue resistance. HIP is particularly effective for consolidating powders, bonding dissimilar materials, and addressing issues in cast and 3D-printed parts.
Key Points Explained:
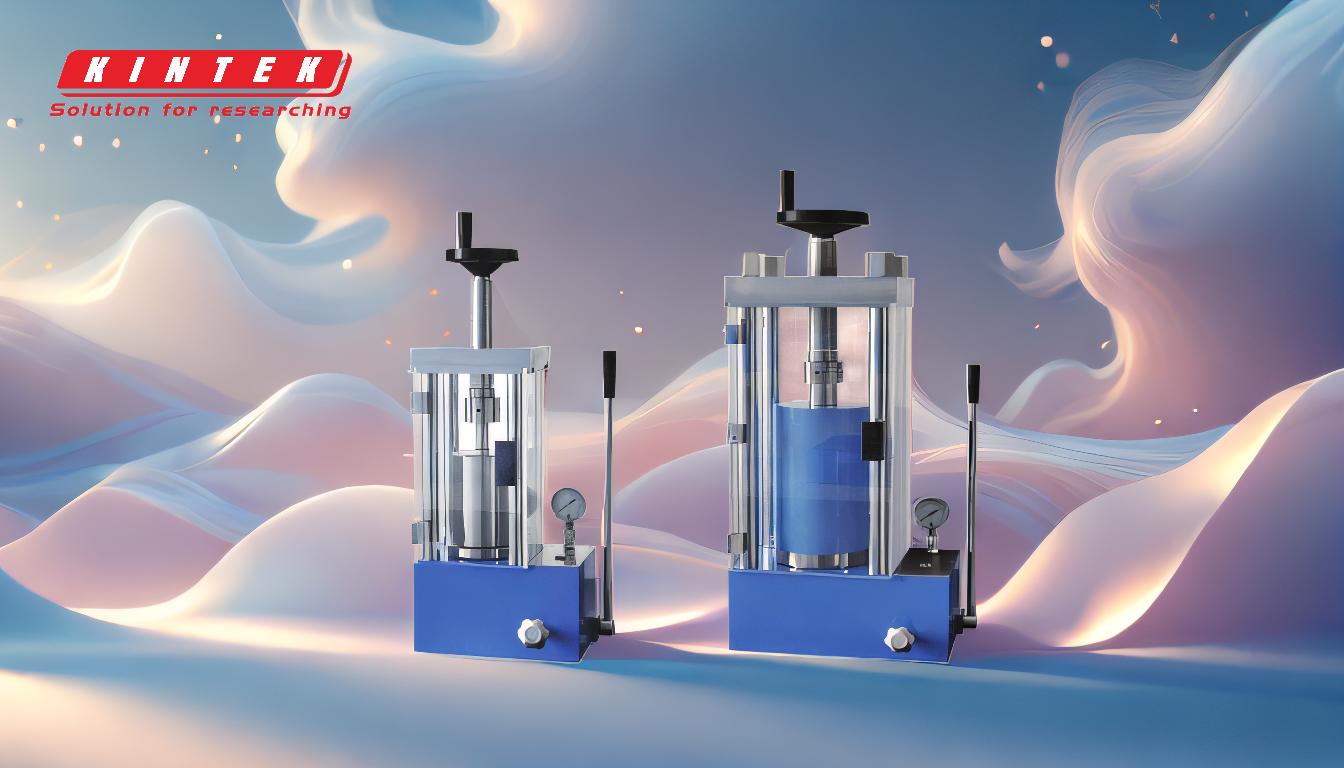
-
Definition and Process Overview:
- Hot isostatic pressing (HIP) is a technique that applies high temperature and uniform pressure in three dimensions to densify materials or bond components.
- The process involves placing the material in a sealed container or flexible mold, which is then subjected to high pressure (typically using an inert gas like argon) and elevated temperatures.
- This combination of heat and pressure eliminates voids, microshrinkage, and porosity, resulting in dense, high-performance materials.
-
Key Components of HIP:
- High-Pressure Vessel: The core of the HIP system, capable of withstanding extreme pressures and temperatures.
- Inert Gas (Argon): Used as the pressure transfer medium to ensure uniform pressure distribution and prevent oxidation or contamination.
- Heating System: Provides the necessary thermal energy to facilitate sintering, diffusion bonding, or densification.
-
Primary Applications:
- Elimination of Defects in Castings: HIP is widely used to remove microshrinkage and porosity in metal castings, improving their mechanical properties.
- Powder Consolidation: The process is effective for compacting powdered materials into dense, uniform components with complex geometries.
- Diffusion Bonding (Cladding): HIP enables the bonding of dissimilar materials, creating strong, durable joints without the need for additional adhesives or fasteners.
- Enhancing Additively Manufactured Parts: For 3D-printed components, HIP addresses issues like porosity and poor layer adhesion, resulting in a uniform microstructure and improved performance.
-
Advantages of HIP:
- Superior Material Properties: HIP enhances density, ductility, fatigue resistance, and thermal stability, making it ideal for high-stress applications.
- Complex Shapes: The process can produce intricate and complex shapes that are difficult to achieve with traditional manufacturing methods.
- Reduced Production Time: HIP consolidates multiple manufacturing steps, such as heat treatment and aging, into a single process, streamlining production.
-
Industrial Applications:
- Aerospace: HIP is used to manufacture turbine blades, engine components, and other critical parts that require high strength and reliability.
- Medical Devices: The process is employed to produce biocompatible implants and surgical instruments with excellent mechanical properties.
- Automotive: HIP improves the performance and durability of engine components, transmission parts, and other high-stress automotive parts.
- Energy: HIP is utilized in the production of components for nuclear reactors, oil and gas equipment, and renewable energy systems.
-
Comparison with Conventional Processes:
- Unlike traditional pressing methods, which apply pressure in a single direction, HIP ensures uniform pressure distribution, resulting in isotropic properties.
- HIP achieves higher densities and better material properties at lower sintering temperatures compared to conventional sintering.
-
Future Trends and Innovations:
- Integration with Additive Manufacturing: HIP is increasingly being used to enhance the properties of 3D-printed parts, addressing challenges like porosity and anisotropy.
- Advanced Materials: The process is being adapted for new materials, such as ceramics and composites, to expand its applications.
- Automation and Process Optimization: Advances in automation and control systems are improving the efficiency and repeatability of HIP processes.
In summary, hot isostatic pressing is a versatile and powerful manufacturing technique that enhances material properties, eliminates defects, and enables the production of complex, high-performance components. Its applications span a wide range of industries, and ongoing innovations continue to expand its capabilities and efficiency.
Summary Table:
Aspect | Details |
---|---|
Process Overview | Combines high temperature and uniform pressure to densify materials. |
Key Components | High-pressure vessel, inert gas (argon), and heating system. |
Primary Applications | Defect elimination in castings, powder consolidation, diffusion bonding. |
Advantages | Superior material properties, complex shapes, reduced production time. |
Industrial Uses | Aerospace, medical devices, automotive, energy. |
Future Trends | Integration with additive manufacturing, advanced materials, automation. |
Learn how hot isostatic pressing can transform your manufacturing process—contact us today!