Hot sintering, also known as hot press sintering, is a specialized manufacturing process used to produce dense, high-performance materials, particularly ceramics and metals. It combines heat and pressure to compact and fuse powdered materials into a solid mass without melting them completely. This process is widely used in industries requiring materials with exceptional strength, thermal stability, and complex geometries. Hot sintering enhances material properties such as density, mechanical strength, and microstructure homogeneity while reducing oxidation and contamination. It is particularly effective for materials with high melting points and is used in applications ranging from industrial components to advanced ceramics.
Key Points Explained:
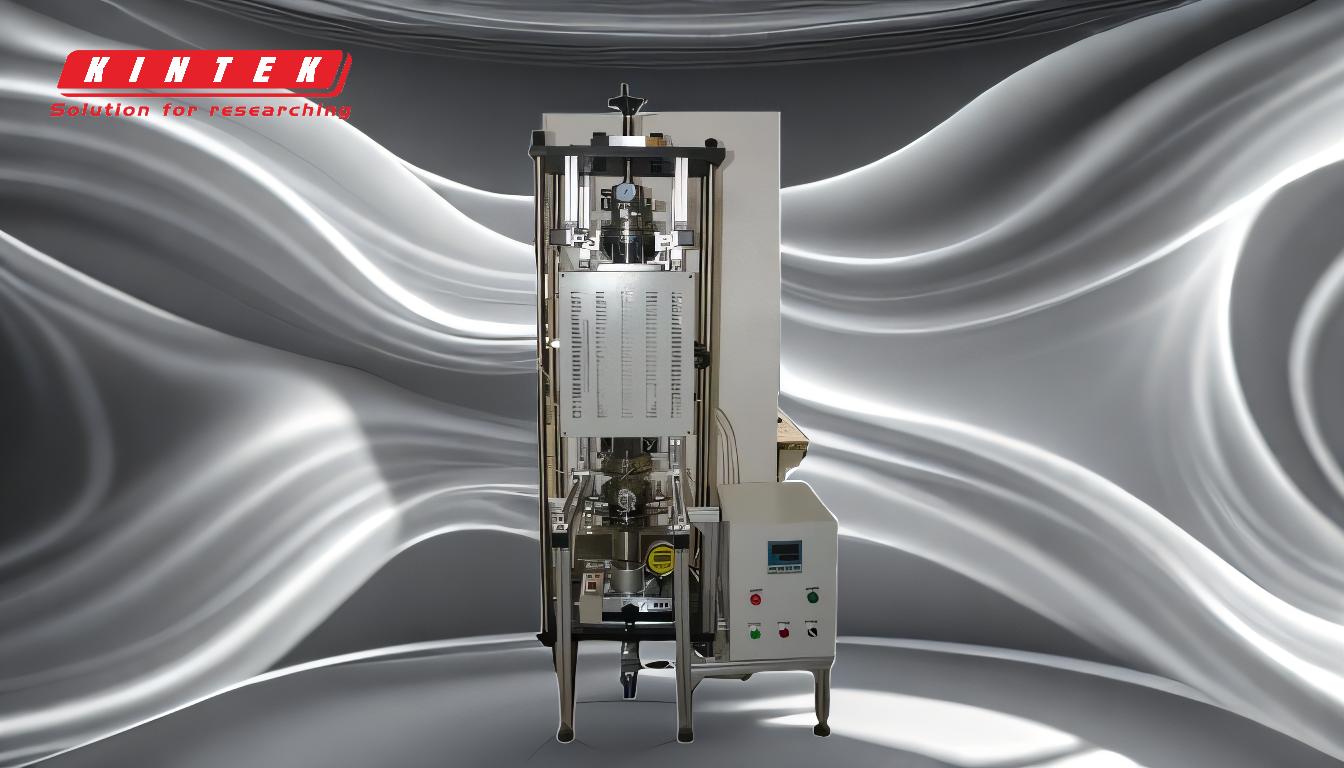
-
Definition and Purpose of Hot Sintering
- Hot sintering is a process that applies both heat and pressure to compact powdered materials into a dense, solid structure.
- It is used to enhance material properties such as strength, density, and thermal stability.
- The process is particularly beneficial for materials with high melting points, such as tungsten, molybdenum, and ceramics.
-
How Hot Sintering Works
- The process involves several key steps:
- Charging: Loading the powdered material into a mold or furnace.
- Vacuuming: Removing gases and impurities by creating a vacuum environment.
- Heating: Raising the temperature to a point where the particles begin to fuse.
- Pressurization: Applying external pressure to compact the material into a dense structure.
- Cooling: Gradually cooling the material to room temperature to stabilize its structure.
- The combination of heat and pressure accelerates the diffusion of atoms across particle boundaries, resulting in a solid, homogeneous material.
- The process involves several key steps:
-
Advantages of Hot Sintering
- Improved Material Properties: Hot sintering enhances density, mechanical strength, and thermal/electrical conductivity.
- Reduced Oxidation and Contamination: The vacuum environment minimizes exposure to oxygen and other contaminants.
- Complex Geometries: The process can produce materials with intricate shapes and fine microstructures.
- Efficiency: Hot sintering offers shorter processing times compared to traditional sintering methods.
-
Applications of Hot Sintering
- Industrial Components: Used to manufacture bearings, heat pipes, and other high-performance parts.
- Advanced Ceramics: Produces ceramics with high strength and chemical stability for use in electronics, aerospace, and medical devices.
- Metals: Ideal for sintering high-melting-point metals like tungsten and molybdenum.
- Jewelry and Consumer Goods: Creates durable and intricate designs for jewelry and other products.
-
Comparison to Other Sintering Methods
- Hot Isostatic Pressing (HIP): Similar to hot sintering but uses uniform pressure from all directions, resulting in materials with homogeneous microstructures and complete density.
- Traditional Sintering: Relies on heat alone, requiring higher temperatures and longer processing times compared to hot sintering.
- Hot sintering achieves densification at lower temperatures (100℃~150℃ lower than traditional methods) due to the added pressure, which provides a driving force 20~100 times greater.
-
Equipment Used in Hot Sintering
- A hot press sintering furnace is the primary equipment, consisting of:
- Furnace Body: Houses the material and maintains the required environment.
- Heater: Provides the necessary heat for sintering.
- Pressure System: Applies external pressure to compact the material.
- Vacuum System: Creates a vacuum to remove impurities and prevent oxidation.
- A hot press sintering furnace is the primary equipment, consisting of:
-
Material Considerations
- Hot sintering is ideal for materials that are difficult to process using traditional methods, such as those with high melting points or requiring high density.
- The process can be tailored to achieve specific material properties, such as porosity or translucency, depending on the application.
-
Challenges and Limitations
- Cost: The equipment and energy requirements for hot sintering can be expensive.
- Complexity: The process requires precise control of temperature, pressure, and vacuum conditions.
- Material Limitations: Not all materials are suitable for hot sintering, particularly those that decompose or react under high temperatures and pressures.
In summary, hot sintering is a highly effective process for producing dense, high-performance materials with enhanced properties. Its ability to combine heat and pressure in a controlled environment makes it a preferred method for manufacturing advanced ceramics, metals, and industrial components. While it has some limitations, its advantages in terms of material quality, efficiency, and versatility make it a valuable technique in modern manufacturing.
Summary Table:
Aspect | Details |
---|---|
Definition | Combines heat and pressure to compact powdered materials into dense solids. |
Key Steps | Charging, Vacuuming, Heating, Pressurization, Cooling. |
Advantages | Enhanced density, strength, and efficiency; reduced oxidation. |
Applications | Industrial components, advanced ceramics, metals, jewelry. |
Comparison to HIP | Uses unidirectional pressure; achieves densification at lower temperatures. |
Equipment | Hot press sintering furnace with heating, pressure, and vacuum systems. |
Material Considerations | Ideal for high-melting-point materials requiring high density. |
Challenges | High cost, complexity, and material limitations. |
Learn how hot sintering can transform your manufacturing process—contact our experts today!