Induction heating for brazing is a highly efficient and precise method used to join metal components by heating them to a specific temperature without melting the base materials. This process involves using electromagnetic induction to generate heat directly within the workpiece, ensuring localized and controlled heating. Induction brazing is particularly advantageous for its speed, consistency, and ability to produce high-quality joints with minimal oxidation. It is widely used in industries such as automotive, aerospace, and electronics, where precision and reliability are critical.
Key Points Explained:
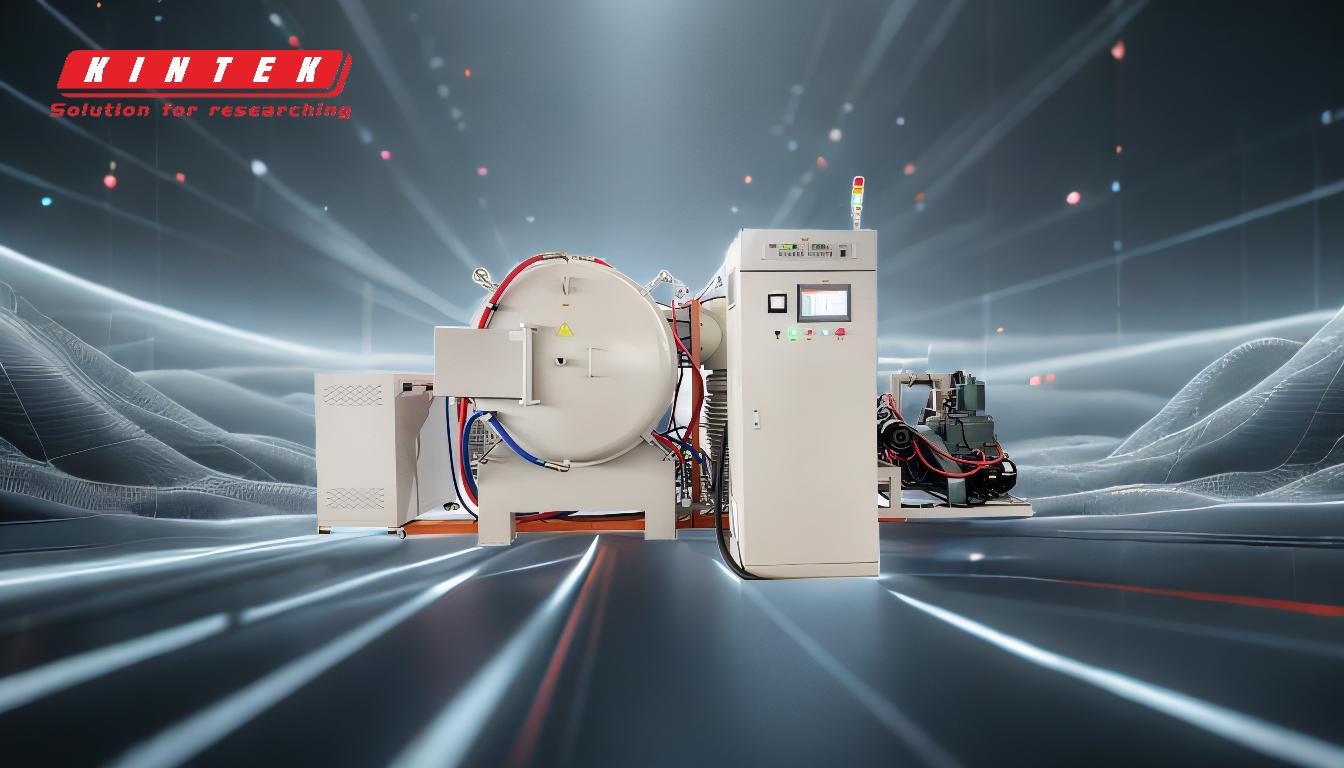
-
What is Induction Heating?
- Induction heating is a process where an alternating electromagnetic field induces eddy currents within a conductive material, generating heat due to electrical resistance. This method allows for rapid and localized heating, making it ideal for applications like brazing.
- Unlike traditional heating methods, induction heating does not require direct contact with a flame or external heat source, reducing contamination risks.
-
How Induction Heating is Applied to Brazing:
- In induction brazing, the workpiece is placed within or near an induction coil. When an alternating current passes through the coil, it creates a magnetic field that induces currents in the workpiece, heating it to the desired temperature.
- The heat is concentrated at the joint area, ensuring that the base materials remain unaffected while the filler metal melts and flows into the joint.
-
Advantages of Induction Brazing:
- Precision and Control: Induction heating allows for precise temperature control, ensuring consistent and repeatable results.
- Speed: The process is faster than traditional methods, reducing production time.
- Cleanliness: Since induction brazing is often performed in a controlled environment, it minimizes oxidation and contamination, leading to stronger and more reliable joints.
- Energy Efficiency: Induction heating is highly efficient, as energy is directly transferred to the workpiece with minimal loss.
-
Applications of Induction Brazing:
- Automotive Industry: Used for joining components like sensors, fuel injectors, and transmission parts.
- Aerospace Industry: Ideal for brazing turbine blades, heat exchangers, and other critical components.
- Electronics: Employed in assembling circuit boards, connectors, and other precision parts.
-
Comparison with Vacuum Brazing:
- While vacuum brazing is performed in a low-pressure environment to eliminate oxidation and contaminants, induction brazing achieves similar results through localized heating and controlled atmospheres.
- Induction brazing is often preferred for smaller components or when rapid heating is required, whereas vacuum brazing is better suited for larger or more complex assemblies.
-
Key Considerations for Induction Brazing:
- Material Compatibility: The workpiece and filler metal must be compatible with induction heating.
- Coil Design: The shape and size of the induction coil must match the workpiece to ensure even heating.
- Temperature Control: Precise monitoring is essential to avoid overheating or underheating the joint.
Induction heating for brazing is a versatile and efficient technique that offers significant advantages in terms of precision, speed, and cleanliness. Its ability to produce high-quality joints makes it a preferred choice in various industries, particularly where reliability and performance are paramount.
Summary Table:
Aspect | Details |
---|---|
Process | Uses electromagnetic induction to heat conductive materials directly. |
Key Advantages | Precision, speed, cleanliness, and energy efficiency. |
Applications | Automotive, aerospace, and electronics industries. |
Comparison | Faster and more localized than vacuum brazing for smaller components. |
Considerations | Material compatibility, coil design, and precise temperature control. |
Ready to enhance your brazing process? Contact us today to learn more about induction heating solutions!