Ion sputtering is a physical vapor deposition (PVD) technique used to deposit thin films onto a substrate. It involves bombarding a target material with high-energy ions, typically from an inert gas like argon, which dislodges atoms from the target. These atoms are then deposited onto a nearby substrate, forming a thin film. The process is highly controlled and requires specialized equipment to manage heat, pressure, and energy transfer. Ion sputtering is particularly useful for materials with high melting points, such as carbon and silicon, and is widely used in industries like semiconductor manufacturing, optics, and surface coating.
Key Points Explained:
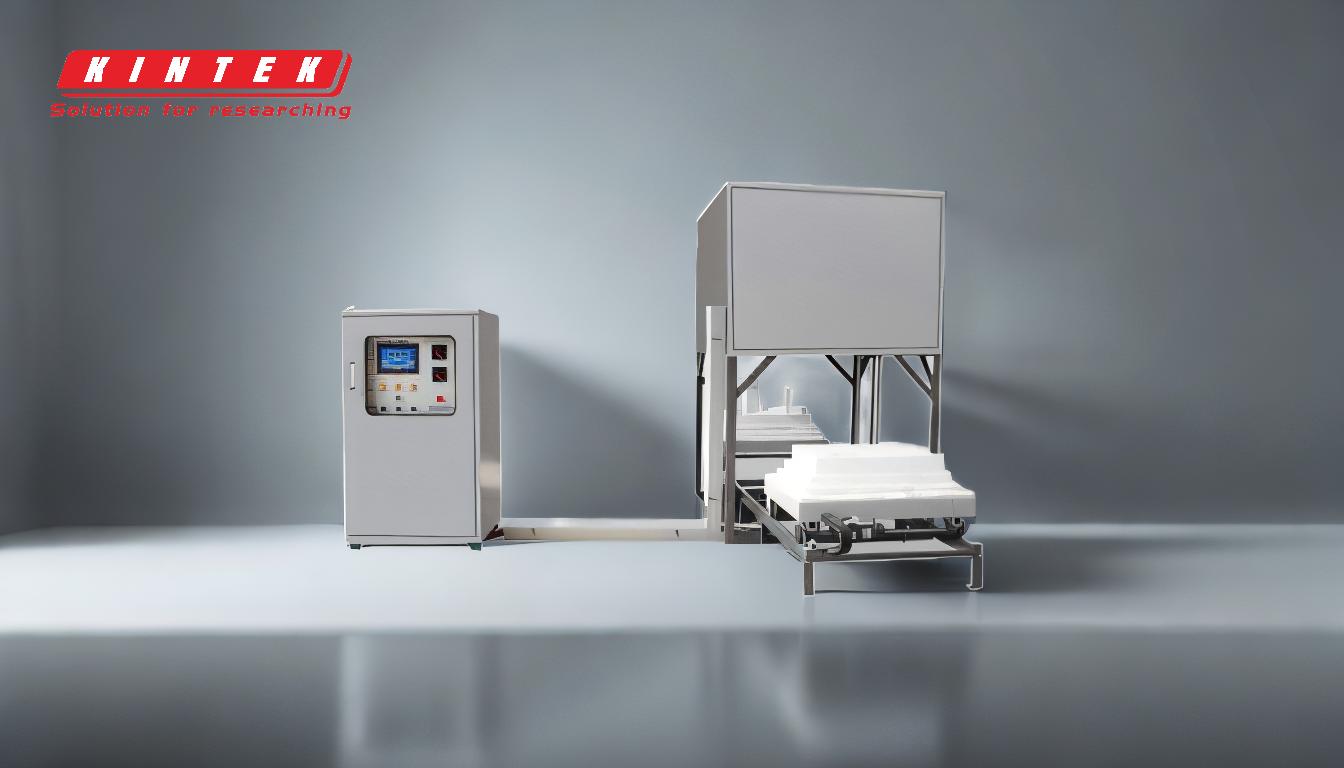
-
Definition of Ion Sputtering:
- Ion sputtering is a physical vapor deposition (PVD) process where high-energy ions bombard a target material, causing atoms to be ejected from the target and deposited onto a substrate as a thin film.
-
Mechanism of Ion Sputtering:
- The process begins with the generation of a plasma, typically using an inert gas like argon.
- High-energy ions from the plasma are accelerated toward the target material.
- When the ion energy exceeds the bond energy of the target material (typically around 4 times the bond energy, which is about 5 eV), atoms are dislodged from the target.
- These ejected atoms traverse through the vacuum chamber and deposit onto the substrate, forming a thin film.
-
Key Components and Requirements:
- Inert Gas: Argon is commonly used because it is chemically inert and does not react with the target or substrate.
- Vacuum Environment: The process requires a controlled vacuum environment to ensure the ions can travel unimpeded and to prevent contamination.
- Energy Source: For insulating materials, an RF (radio frequency) energy source is used to generate the plasma.
- Heat Management: Specialized chilling is often required to manage the heat generated during the process.
-
Applications of Ion Sputtering:
- Semiconductor Manufacturing: Used to deposit thin films of metals and insulators on silicon wafers.
- Optics: Coating lenses and mirrors to enhance their reflective or anti-reflective properties.
- Surface Coating: Applying wear-resistant or decorative coatings to various materials.
- High Melting Point Materials: Effective for depositing materials like carbon and silicon, which have extremely high melting points.
-
Advantages of Ion Sputtering:
- Precision: The process allows for highly controlled and uniform thin film deposition.
- Versatility: Can be used with a wide range of materials, including metals, alloys, and insulators.
- High-Quality Films: Produces films with excellent adhesion and minimal defects.
- Automation: Automated systems enhance efficiency and reduce the variability associated with manual methods.
-
Challenges and Considerations:
- Heat Generation: The process generates significant heat, requiring effective cooling systems.
- Pressure Control: Maintaining the correct vacuum pressure is crucial for the success of the process.
- Material Compatibility: Not all materials are suitable for sputtering, particularly those that may react with the inert gas or plasma.
By understanding these key points, one can appreciate the complexity and precision involved in ion sputtering, as well as its importance in various high-tech industries.
Summary Table:
Aspect | Details |
---|---|
Definition | A PVD process where high-energy ions dislodge atoms from a target material. |
Mechanism | Plasma generation, ion bombardment, and thin film deposition. |
Key Components | Inert gas (argon), vacuum environment, RF energy source, heat management. |
Applications | Semiconductor manufacturing, optics, surface coating, high-melting materials. |
Advantages | Precision, versatility, high-quality films, automation. |
Challenges | Heat generation, pressure control, material compatibility. |
Discover how ion sputtering can revolutionize your thin film processes—contact our experts today!