A low-frequency induction furnace is a type of induction furnace that operates at lower frequencies, typically ranging from 50 Hz to 10 kHz. It is widely used in metal melting and heating applications due to its ability to handle large volumes of metal with high efficiency and minimal contamination. Unlike high-frequency induction furnaces, low-frequency models are better suited for melting bulkier materials and are often used in foundries for melting metals like iron, steel, copper, and aluminum. These furnaces leverage electromagnetic induction to generate heat within the metal, ensuring uniform heating and melting. They are known for their energy efficiency, reduced environmental impact, and precise control over temperature and composition.
Key Points Explained:
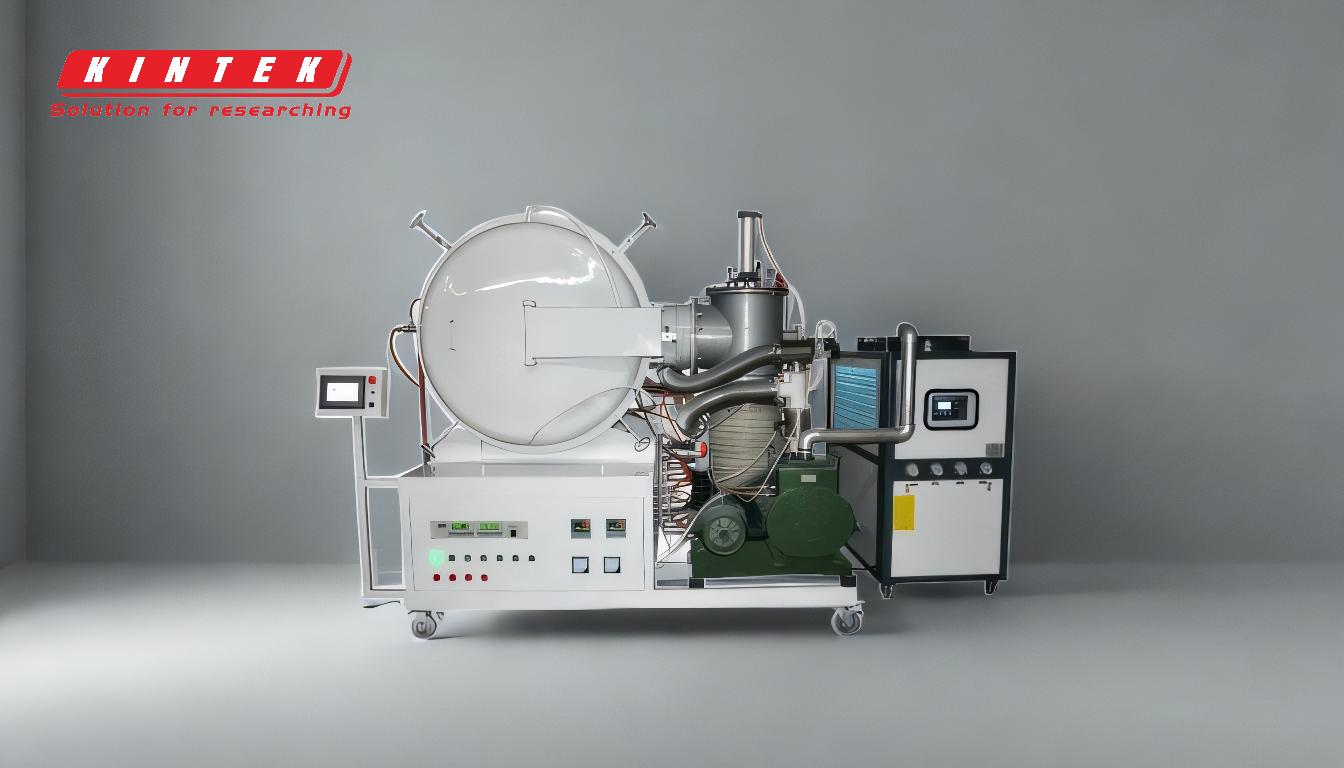
-
Definition and Working Principle:
- A low-frequency induction furnace operates by generating an alternating electromagnetic field, which induces eddy currents within the metal. These eddy currents produce heat due to the material's electrical resistance, leading to uniform heating and melting.
- The furnace's main components include an inductor, furnace body, power supply, capacitor, and control system. The inductor creates the electromagnetic field, while the control system ensures precise temperature regulation.
-
Frequency Range and Applications:
- Low-frequency induction furnaces typically operate between 50 Hz and 10 kHz. This lower frequency range makes them ideal for melting larger quantities of metal, such as iron, steel, copper, and aluminum.
- They are commonly used in foundries for casting applications, where molten metal is poured into molds to create finished products.
-
Advantages Over Other Furnace Types:
- Energy Efficiency: Low-frequency induction furnaces are highly efficient, with more than 95% effective output power. This reduces energy consumption and operational costs.
- Minimal Contamination: Unlike gas furnaces, induction furnaces produce less contamination, ensuring higher-quality molten metal.
- Environmental Impact: These furnaces emit less noise, smoke, gas, dust, and waste residue, making them more environmentally friendly.
- Precise Control: Advanced control systems allow for accurate temperature and composition regulation, ensuring consistent results.
-
Operational Features:
- Continuous Operation: Many low-frequency induction furnaces are designed for 24-hour continuous operation, making them suitable for high-volume production environments.
- Safety and Reliability: They come equipped with all-round protection features, including alarms for over-voltage, over-current, overheating, and water shortage, ensuring safe and reliable operation.
- User-Friendly Design: These furnaces are easy to operate, with powerful process automation capabilities that simplify the melting process.
-
Comparison with Medium and High-Frequency Induction Furnaces:
- Melting Speed: Low-frequency furnaces are generally slower than high-frequency models but are better suited for larger volumes of metal.
- Material Versatility: While medium and high-frequency furnaces can melt a wider range of materials, low-frequency furnaces excel in handling bulkier metals like iron and steel.
- Cost-Effectiveness: Low-frequency furnaces are often more cost-effective for large-scale operations due to their energy efficiency and lower operational costs.
-
Applications in Foundries:
- Low-frequency induction furnaces are extensively used in foundries for melting metals and creating castings. The molten metal is poured into molds, and after solidification, the finished product is removed.
- They are particularly advantageous for producing high-quality castings with minimal defects, thanks to the uniform heating and precise temperature control.
-
Technological Advancements:
- Modern low-frequency induction furnaces incorporate advanced technologies such as IGBT frequency conversion and power regulation. These features enhance efficiency, reliability, and miniaturization.
- The integration of automation and control systems has further improved their performance, making them a preferred choice for industrial applications.
In summary, low-frequency induction furnaces are a vital tool in metal melting and foundry operations, offering a combination of energy efficiency, environmental benefits, and precise control. Their ability to handle large volumes of metal with minimal contamination makes them indispensable in industries requiring high-quality castings and consistent production performance.
Summary Table:
Feature | Details |
---|---|
Frequency Range | 50 Hz to 10 kHz |
Key Applications | Melting iron, steel, copper, and aluminum in foundries |
Advantages | Energy efficiency (>95%), minimal contamination, eco-friendly, precise control |
Operational Features | 24-hour continuous operation, safety alarms, user-friendly automation |
Comparison with Others | Slower melting speed but better for large volumes and cost-effectiveness |
Technological Advances | IGBT frequency conversion, automation, and enhanced reliability |
Upgrade your metal melting process with a low-frequency induction furnace—contact us today to learn more!