Low Pressure Chemical Vapor Deposition (LPCVD) is a specialized form of Chemical Vapor Deposition (CVD) that operates at reduced pressures, typically between 0.1 to 10 Torr, and at temperatures ranging from 200 to 800°C. This method is widely used in the semiconductor industry and for manufacturing microelectromechanical systems (MEMS), resistors, capacitor dielectrics, and anti-reflective coatings. LPCVD involves introducing reactant gases into a chamber through a specialized precursor delivery system, where they react on a heated substrate to form a thin film. The process is highly controlled, allowing for the deposition of high-purity, uniform films with precise chemical and physical properties. By operating at low pressures, LPCVD minimizes unwanted gas-phase reactions, ensuring better film quality and uniformity.
Key Points Explained:
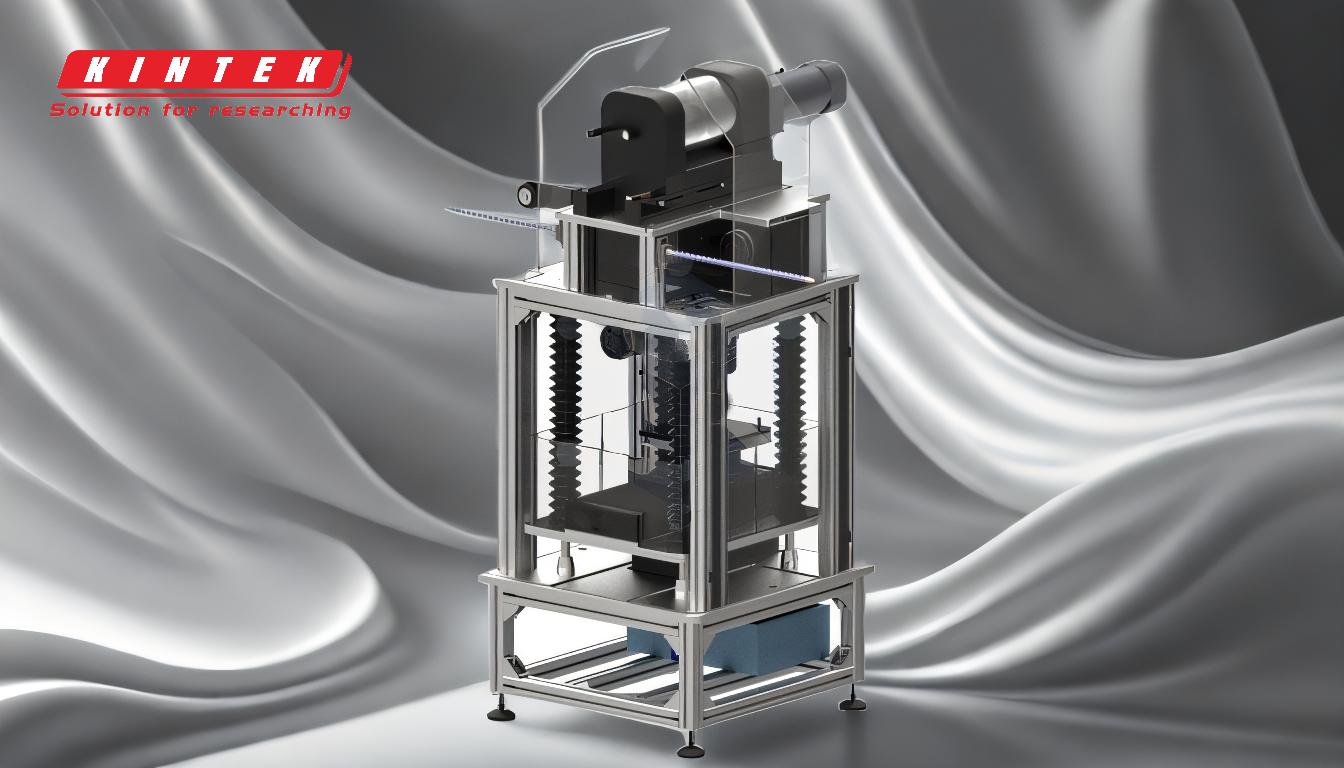
-
Definition and Process of LPCVD:
- LPCVD is a variant of CVD that operates under low-pressure conditions (0.1 – 10 Torr) and moderate temperatures (200 – 800°C).
- Reactant gases are introduced into a chamber via a precursor delivery system, often a showerhead, to ensure even distribution.
- The substrate is heated to promote heterogeneous surface reactions, where the gases react or decompose to form a thin film on the substrate.
- By-products of the reaction are removed using vacuum pumps, maintaining the low-pressure environment.
-
Advantages of LPCVD:
- High Purity and Uniformity: The low-pressure environment minimizes gas-phase reactions, leading to high-purity films with excellent uniformity.
- Controlled Deposition: Parameters such as temperature, pressure, gas flow rate, and gas concentration can be precisely controlled, allowing for tailored film properties.
- Versatility: LPCVD can deposit a wide range of materials, including polycrystalline and amorphous films, making it suitable for various applications.
-
Applications of LPCVD:
- Semiconductor Industry: LPCVD is used to deposit thin films for resistors, capacitor dielectrics, and anti-reflective coatings in semiconductor devices.
- MEMS Fabrication: The process is critical for creating microelectromechanical systems, where precise and uniform thin films are essential.
- Optical Coatings: LPCVD is employed to produce anti-reflective coatings and other optical layers with controlled thickness and properties.
-
Comparison with Other CVD Techniques:
- Atmospheric Pressure CVD (APCVD): Unlike LPCVD, APCVD operates at atmospheric pressure, which can lead to less uniform films due to increased gas-phase reactions.
- Plasma-Enhanced CVD (PECVD): PECVD uses plasma to enhance chemical reactions at lower temperatures, but it may not achieve the same level of film purity as LPCVD.
- Optical LCVD: Optical LCVD uses laser energy to induce reactions, which is different from the thermal activation used in LPCVD.
-
Key Process Parameters:
- Temperature: The substrate temperature is critical for controlling the reaction kinetics and film properties.
- Pressure: Operating at low pressures reduces unwanted gas-phase reactions and improves film uniformity.
- Gas Flow Rate: Precise control of gas flow ensures even distribution of reactants and consistent film deposition.
- Gas Concentration: The ratio of reactant gases can be adjusted to achieve desired film composition and properties.
-
Challenges and Considerations:
- Equipment Complexity: LPCVD systems require specialized equipment, including vacuum pumps and precise temperature control systems.
- Process Optimization: Achieving the desired film properties often requires careful optimization of process parameters.
- Cost: The need for high-purity gases and advanced equipment can make LPCVD more expensive than other deposition methods.
In summary, LPCVD is a highly controlled and versatile thin-film deposition technique that offers significant advantages in terms of film purity, uniformity, and process control. Its applications span across the semiconductor, MEMS, and optical industries, making it a critical tool in modern manufacturing and nanotechnology.
Summary Table:
Aspect | Details |
---|---|
Definition | A CVD variant operating at low pressures (0.1–10 Torr) and moderate temperatures (200–800°C). |
Process | Reactant gases react on a heated substrate to form thin films, with by-products removed via vacuum pumps. |
Advantages | High purity, uniformity, controlled deposition, and versatility in material deposition. |
Applications | Semiconductor devices, MEMS fabrication, and optical coatings. |
Key Parameters | Temperature, pressure, gas flow rate, and gas concentration. |
Challenges | Equipment complexity, process optimization, and higher costs. |
Discover how LPCVD can enhance your manufacturing processes—contact our experts today!