Magnetron sputtering is a highly versatile and widely used physical vapor deposition (PVD) technique that involves the ejection of atoms from a target material onto a substrate to form a thin film. This process is driven by the bombardment of the target material with high-energy ions in a vacuum environment, facilitated by a magnetic field. The method is known for its ability to produce uniform, dense, and high-quality coatings at relatively low temperatures, making it suitable for a wide range of industrial applications. These applications span across electronics, optics, medical devices, and more, where precise control over film thickness, composition, and properties is essential.
Key Points Explained:
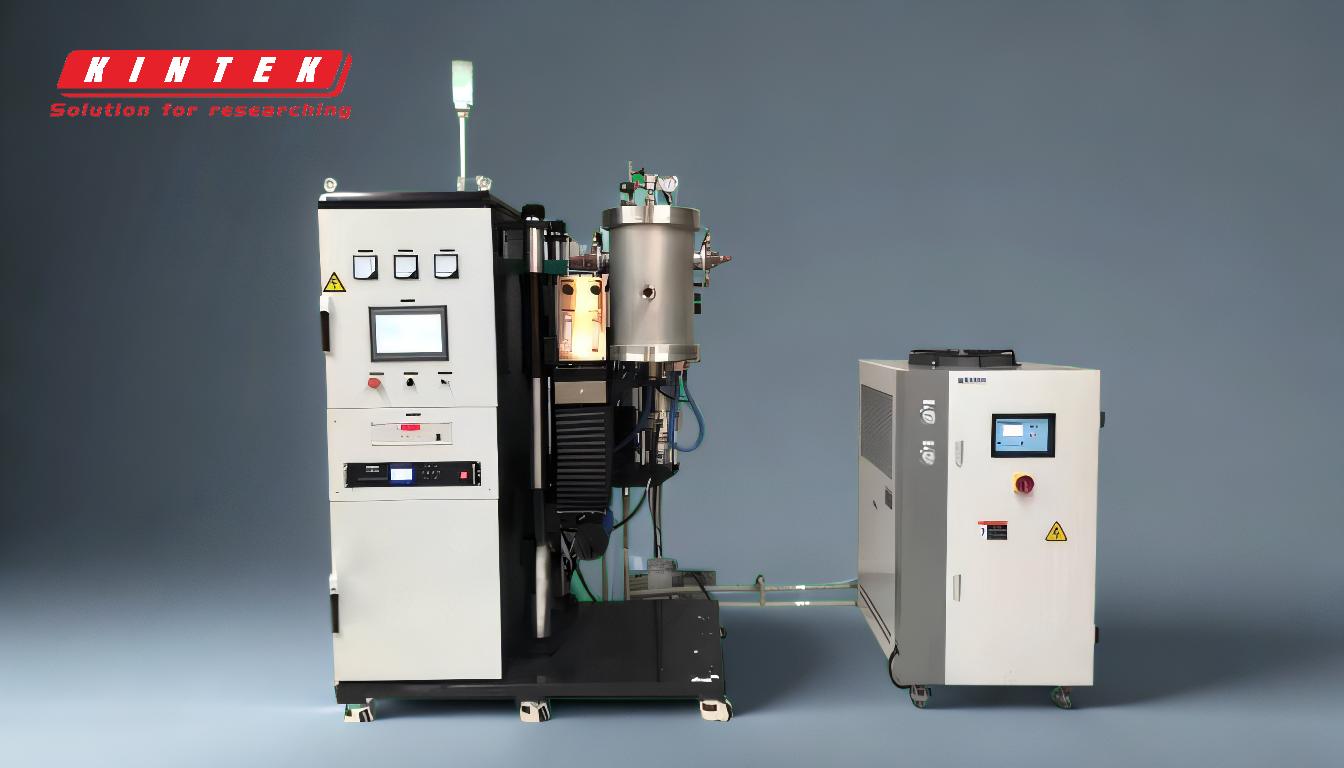
-
Definition and Process of Magnetron Sputtering:
- Magnetron sputtering is a PVD process that uses a magnetic field to enhance the efficiency of sputtering.
- The process involves introducing an inert gas, typically argon, into a vacuum chamber. A high voltage is applied to create a plasma, which ionizes the argon gas.
- The positively charged argon ions are accelerated towards a negatively charged target (the material to be sputtered). Upon impact, atoms are ejected from the target and deposited onto a substrate, forming a thin film.
-
Role of Magnetic Fields:
- Magnetic fields are crucial in magnetron sputtering as they trap electrons near the target surface, increasing the ionization of the gas and enhancing the sputtering rate.
- This magnetic confinement reduces the energy loss of electrons and increases the density of the plasma, leading to faster and more efficient deposition.
-
Advantages of Magnetron Sputtering:
- Low Deposition Temperature: Suitable for temperature-sensitive substrates.
- High-Quality Films: Produces uniform, dense, and adherent coatings.
- Versatility: Compatible with a wide range of materials, including metals, alloys, and compounds.
- Precision Control: Allows for precise control over film thickness, composition, and properties.
-
Industrial Applications:
- Electronics: Used in the manufacture of gate dielectrics, passive thin-film components, interlayer dielectrics, sensors, printed circuit boards, and surface acoustic wave devices.
- Optics: Applied in the production of anti-reflective coatings, mirrors, filters, and optical components for lasers and spectroscopy.
- Medical Devices: Utilized in the fabrication of angioplasty devices, anti-rejection coatings, radiation capsules, and dental implants.
- Energy and Coatings: Employed in thin-film solar cells, thin-film batteries, solar control coatings on glass, and wear-resistant or low-friction coatings on machine parts.
-
Process Steps in Detail:
- Gas Introduction: Inert gas (argon) is introduced into the vacuum chamber.
- Plasma Creation: High voltage ionizes the gas, creating a plasma containing argon ions and free electrons.
- Ion Bombardment: Positively charged argon ions are attracted to the negatively charged target, ejecting target atoms upon impact.
- Film Formation: Ejected atoms travel through the vacuum and deposit onto the substrate, forming a thin film.
-
Material Compatibility:
- Magnetron sputtering is compatible with a wide range of materials, including metals, alloys, and compounds. This versatility allows for the deposition of films with specific properties tailored to the application.
-
Benefits in Specific Applications:
- Electronics: Enhances the durability and performance of electronic components.
- Optics: Enables precise control over optical properties such as refractive index and thickness, crucial for high-performance optical coatings.
- Medical Devices: Provides biocompatible and anti-rejection coatings, improving the safety and effectiveness of medical implants.
Magnetron sputtering is a cornerstone technology in modern material science and engineering, offering unmatched precision and versatility in thin-film deposition. Its applications are vast and critical to advancements in electronics, optics, energy, and medical technology.
Summary Table:
Key Aspect | Details |
---|---|
Definition | PVD process using magnetic fields to enhance sputtering efficiency. |
Process | Inert gas ionized in a vacuum, target atoms ejected, deposited on substrate. |
Role of Magnetic Fields | Traps electrons, increases plasma density, and boosts sputtering rate. |
Advantages | Low temperature, high-quality films, versatile materials, precise control. |
Applications | Electronics, optics, medical devices, energy, and coatings. |
Discover how magnetron sputtering can revolutionize your applications—contact our experts today!