Physical Vapor Deposition (PVD) is a thin-film coating process where a solid material is vaporized in a vacuum environment and then deposited onto a substrate to form a thin, uniform layer. This process is widely used in industries to enhance the surface properties of materials, such as improving hardness, wear resistance, and corrosion resistance. PVD techniques include methods like sputtering, evaporation, and ion plating, each with its own advantages and applications. The process is highly controllable, allowing for precise thickness and composition of the coating, making it suitable for applications in electronics, optics, and tool manufacturing.
Key Points Explained:
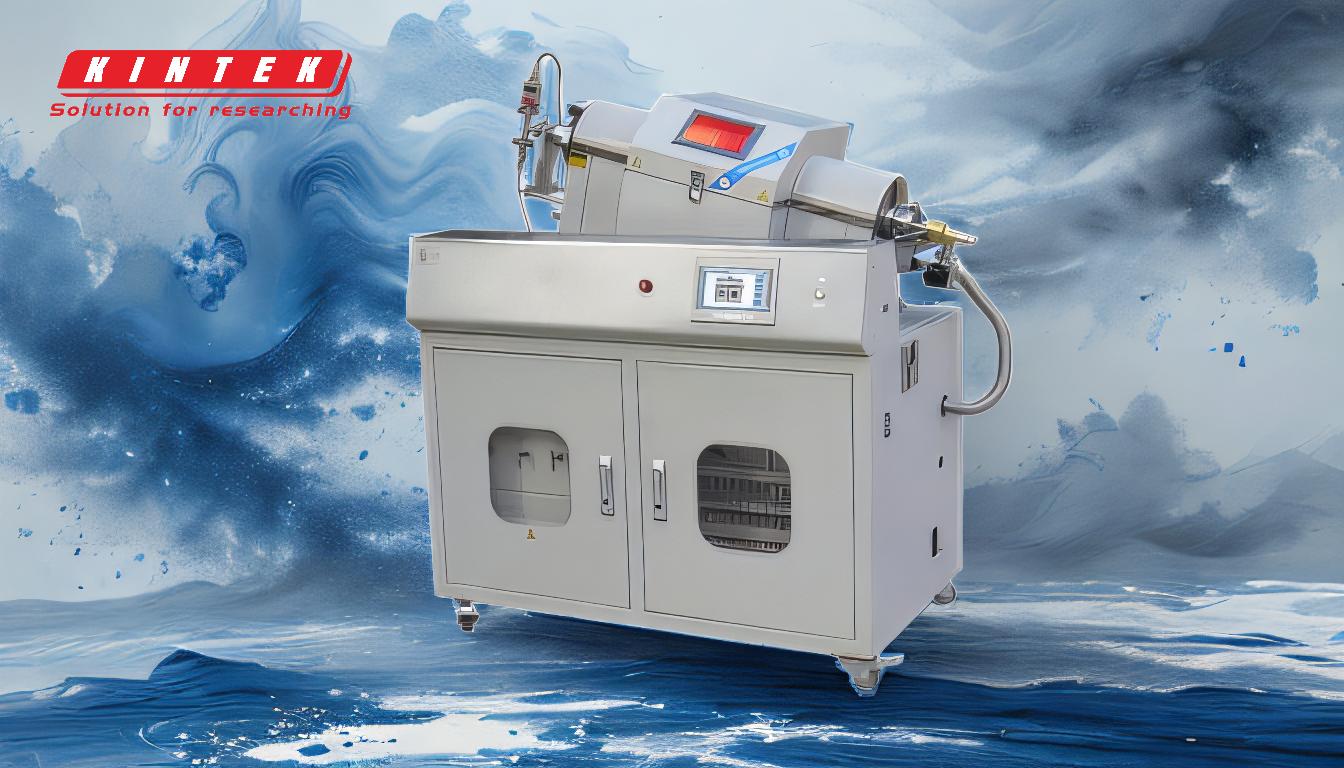
-
Definition and Overview of PVD:
- Physical Vapor Deposition (PVD) is a vacuum coating process where a solid material is vaporized and then condensed onto a substrate to form a thin film.
- This process is used to improve the surface properties of materials, such as hardness, wear resistance, and corrosion resistance.
-
Key Components of PVD:
- Vacuum Environment: PVD processes are conducted in a vacuum to prevent contamination and ensure high-quality coatings.
- Target Material: The material to be deposited, often in the form of a solid target, is vaporized using physical means such as heating or sputtering.
- Substrate: The surface onto which the vaporized material is deposited, which can be made of various materials including metals, ceramics, and polymers.
-
Common PVD Techniques:
- Sputtering: Involves bombarding a target material with high-energy ions, causing atoms to be ejected and deposited onto the substrate.
- Evaporation: The target material is heated until it vaporizes, and the vapor then condenses onto the substrate.
- Ion Plating: Combines evaporation with ion bombardment to enhance the adhesion and density of the coating.
-
Advantages of PVD:
- High-Quality Coatings: PVD produces coatings with excellent adhesion, uniformity, and purity.
- Versatility: Suitable for a wide range of materials and substrates.
- Environmental Friendliness: PVD processes are generally cleaner and produce less waste compared to other coating methods.
-
Applications of PVD:
- Electronics: Used for depositing conductive and insulating layers in semiconductor devices.
- Optics: Applied in the production of anti-reflective and reflective coatings for lenses and mirrors.
- Tool Manufacturing: Enhances the durability and performance of cutting tools and molds.
-
Process Control and Precision:
- PVD allows for precise control over the thickness and composition of the coatings, making it ideal for applications requiring high precision and repeatability.
- Advanced monitoring and control systems ensure consistent quality and performance of the coatings.
-
Future Trends in PVD:
- Development of new materials and techniques to further improve the properties and applications of PVD coatings.
- Increasing use of PVD in emerging fields such as renewable energy and biomedical devices.
By understanding these key points, one can appreciate the significance of PVD in modern manufacturing and its potential for future advancements.
Summary Table:
Aspect | Details |
---|---|
Definition | A vacuum coating process where solid material is vaporized and deposited. |
Key Components | Vacuum environment, target material, substrate. |
Common Techniques | Sputtering, evaporation, ion plating. |
Advantages | High-quality coatings, versatility, environmental friendliness. |
Applications | Electronics, optics, tool manufacturing. |
Process Control | Precise thickness and composition control. |
Future Trends | New materials, renewable energy, biomedical devices. |
Unlock the potential of PVD for your industry—contact our experts today to learn more!