Sintered glass refers to a type of glass material that has been processed using the sintering method, which involves compacting and heating glass particles below their melting point to form a solid, durable mass. This process enhances the material's strength, durability, and resistance to various environmental factors. Sintered glass is commonly used in applications requiring high thermal and chemical resistance, such as filtration systems, laboratory equipment, and industrial components. The sintering process bonds glass particles at a molecular level, creating a dense and uniform structure without melting the material entirely.
Key Points Explained:
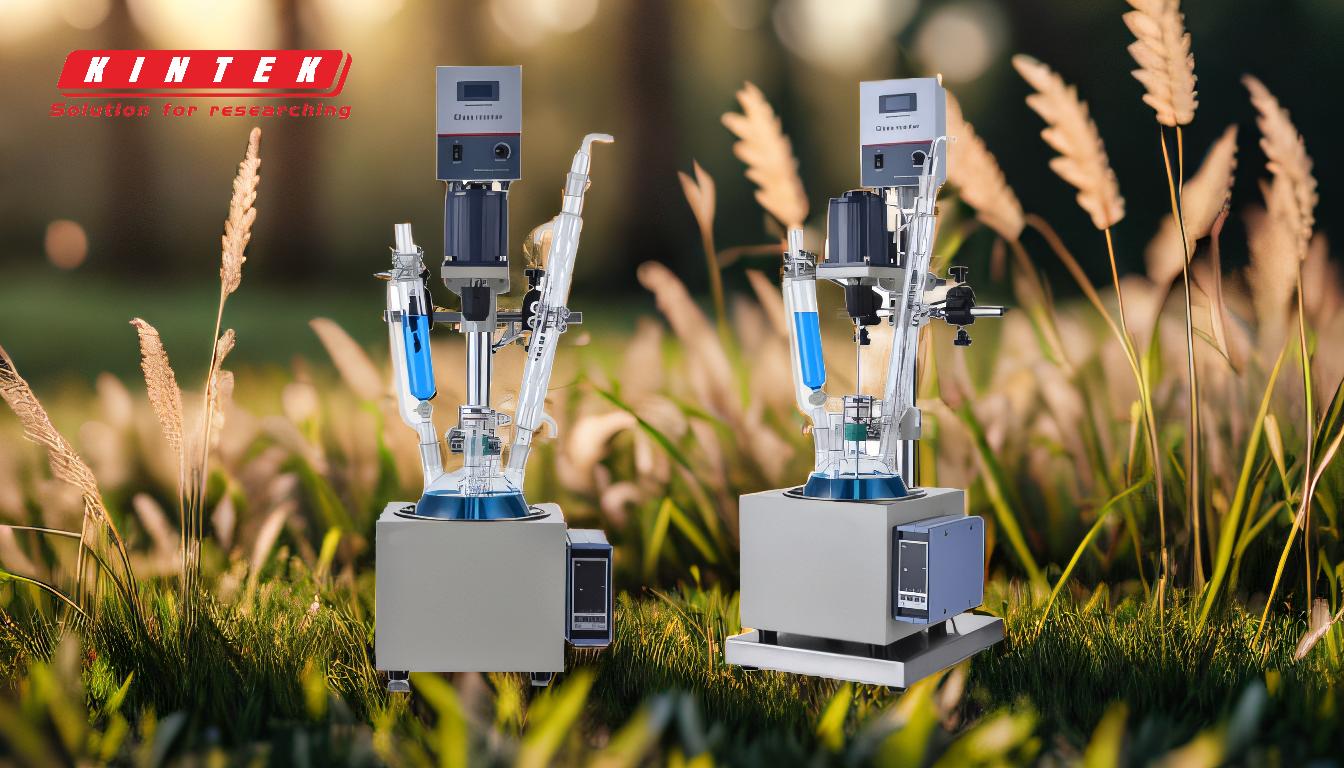
-
Definition of Sintered Glass:
- Sintered glass is a material created by compacting and heating glass particles below their melting point. This process allows the particles to bond at a molecular level, forming a solid and durable mass.
- Unlike traditional glass manufacturing, sintering does not involve liquefying the material, which preserves its structural integrity and enhances its properties.
-
The Sintering Process:
- Compaction: Glass particles are pressed into a desired shape or form.
- Heating: The compacted material is heated in a controlled environment at temperatures below the glass's melting point.
- Bonding: During heating, atoms diffuse across particle boundaries, fusing them together to create a dense and uniform structure.
-
Properties of Sintered Glass:
- Durability: The sintering process creates a strong, hard material resistant to wear and tear.
- Thermal Resistance: Sintered glass can withstand extreme temperatures without deforming or breaking.
- Chemical Resistance: It is highly resistant to chemical reactions, making it suitable for use in harsh environments.
- Porosity Control: The process allows for precise control over the material's porosity, which is useful in filtration applications.
-
Applications of Sintered Glass:
- Filtration Systems: Sintered glass is widely used in filters for liquids and gases due to its controlled porosity and chemical resistance.
- Laboratory Equipment: It is used in lab apparatus like crucibles, fritted discs, and chromatography columns.
- Industrial Components: Sintered glass is employed in high-temperature and corrosive environments, such as in the chemical and pharmaceutical industries.
-
Advantages of Sintered Glass:
- Enhanced Strength: The sintering process results in a material that is stronger and more durable than traditional glass.
- Customizability: The process allows for the creation of complex shapes and sizes with controlled porosity.
- Cost-Effectiveness: Sintering is a relatively low-cost manufacturing process compared to other methods of producing high-performance glass materials.
-
Comparison with Other Sintered Materials:
- Sintered Ceramics: Like sintered glass, sintered ceramics are highly durable and resistant to environmental factors. However, ceramics are typically made from clay or other natural materials, whereas glass is made from silica-based compounds.
- Sintered Metals: Sintered metals are created using a similar process but involve metal powders. The resulting materials are used in applications requiring high strength and wear resistance, such as automotive parts and tools.
In summary, sintered glass is a versatile and durable material created through the sintering process, offering unique properties that make it suitable for a wide range of applications. Its ability to withstand extreme conditions and its customizable nature make it a valuable material in various industries.
Summary Table:
Aspect | Details |
---|---|
Definition | Glass particles compacted and heated below melting point to form a solid mass. |
Process | Compaction, heating, and bonding of glass particles. |
Properties | Durability, thermal resistance, chemical resistance, and porosity control. |
Applications | Filtration systems, laboratory equipment, and industrial components. |
Advantages | Enhanced strength, customizability, and cost-effectiveness. |
Interested in learning how sintered glass can benefit your industry? Contact us today for expert advice!