Medical device coatings are specialized layers applied to medical tools and implants to enhance their performance, safety, and longevity. These coatings serve multiple purposes, such as reducing friction, ensuring biocompatibility, providing antimicrobial properties, and acting as chemical barriers. They are often applied using advanced techniques like Physical Vapor Deposition (PVD), which ensures durability and precision. For example, black titanium nitride coatings are increasingly used in medical tools due to their ability to reduce friction, prevent infections, and protect against chemical sensitivities like nickel allergies. These coatings not only improve the functional aspects of medical devices but also enhance their aesthetic appeal.
Key Points Explained:
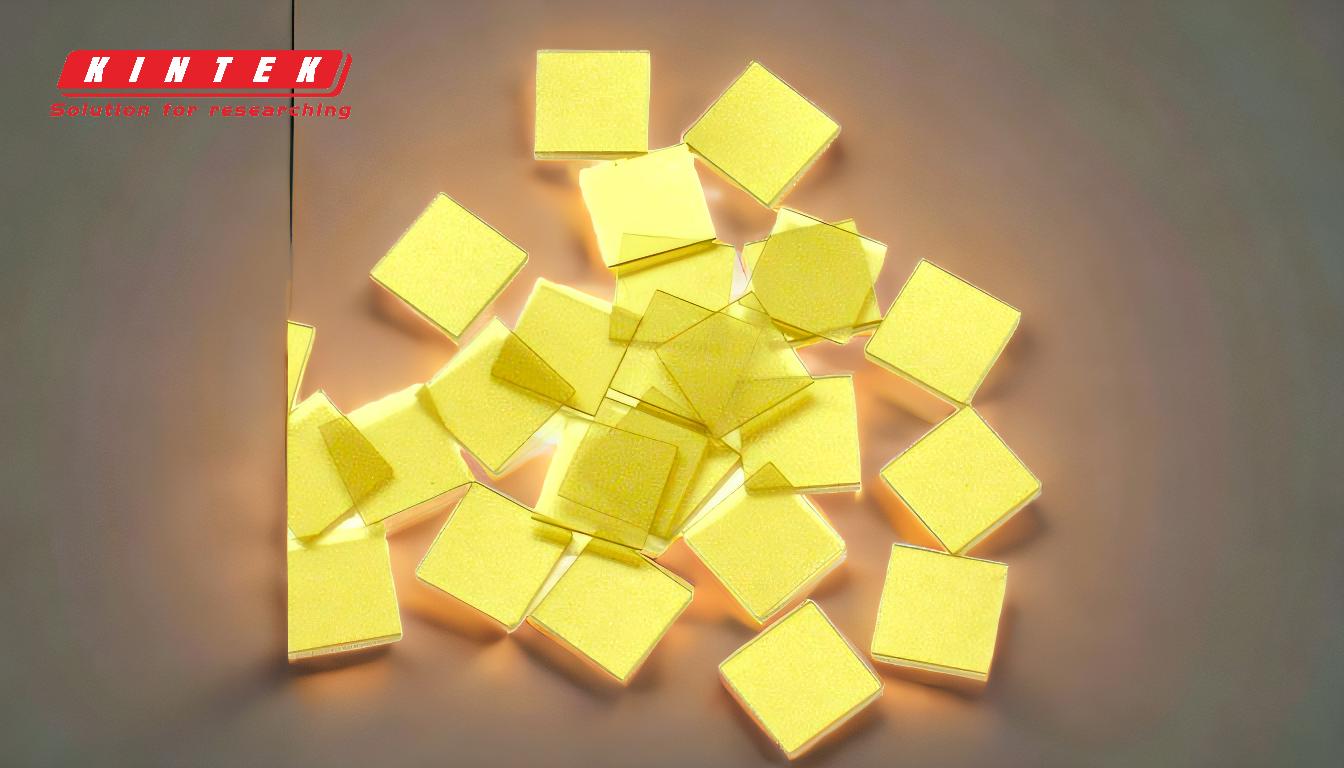
-
Definition and Purpose of Medical Device Coatings:
- Medical device coatings are specialized layers applied to medical tools and implants to improve their functionality and safety.
- They serve multiple purposes, including reducing friction, ensuring biocompatibility, providing antimicrobial properties, and acting as chemical barriers.
-
Types of Coatings:
- Vacuum Coatings: Applied using techniques like Physical Vapor Deposition (PVD), these coatings are known for their durability and precision.
- Black Titanium Nitride: A specific type of vacuum coating that is becoming standard for medical tools due to its excellent properties.
-
Benefits of Medical Device Coatings:
- Reduced Friction: Coatings like black titanium nitride significantly reduce friction, making medical tools easier to use and less likely to cause tissue damage.
- Biocompatibility: Essential for implants, these coatings ensure that the device is compatible with the human body, reducing the risk of adverse reactions.
- Antimicrobial Properties: Coatings can help prevent infections by inhibiting the growth of bacteria and other pathogens on the device surface.
- Chemical Barrier: For patients sensitive to certain materials like nickel, coatings provide a protective barrier, reducing the risk of allergic reactions.
- Aesthetic Improvement: Beyond functionality, these coatings can also enhance the visual appeal of medical tools, making them more attractive to both medical professionals and patients.
-
Application Techniques:
- Physical Vapor Deposition (PVD): A common method for applying vacuum coatings, PVD ensures a thin, uniform layer that adheres strongly to the substrate.
- Precision and Durability: PVD coatings are known for their precision and durability, making them ideal for medical applications where reliability is crucial.
-
Examples and Applications:
- Surgical Instruments: Tools like scalpels and forceps often have coatings to reduce friction and prevent infections.
- Implants: Coatings on implants ensure biocompatibility and reduce the risk of rejection or adverse reactions.
- Sensitive Patients: For patients with nickel allergies, coatings provide a necessary chemical barrier, making medical devices safer to use.
-
Future Trends:
- Increased Use of Advanced Coatings: As technology advances, more sophisticated coatings with enhanced properties are likely to become standard in medical devices.
- Focus on Infection Control: With the rise of antibiotic-resistant bacteria, antimicrobial coatings will become increasingly important in preventing hospital-acquired infections.
- Customization for Patient Needs: Future coatings may be tailored to meet the specific needs of individual patients, such as those with unique allergies or sensitivities.
In summary, medical device coatings are essential for enhancing the performance, safety, and longevity of medical tools and implants. Techniques like PVD allow for the application of durable, precise coatings such as black titanium nitride, which offer benefits like reduced friction, biocompatibility, antimicrobial properties, and chemical barriers. These coatings not only improve the functional aspects of medical devices but also contribute to their aesthetic appeal, making them a crucial component in modern medical technology.
Summary Table:
Aspect | Details |
---|---|
Purpose | Enhance performance, safety, and longevity of medical tools and implants. |
Types | Vacuum coatings (e.g., PVD), black titanium nitride. |
Benefits | Reduced friction, biocompatibility, antimicrobial properties, chemical barriers, aesthetic improvement. |
Application Techniques | Physical Vapor Deposition (PVD) for precision and durability. |
Examples | Surgical instruments, implants, tools for sensitive patients. |
Future Trends | Advanced coatings, infection control, customization for patient needs. |
Learn how medical device coatings can revolutionize your tools—contact us today for expert advice!