A medium frequency induction furnace is a type of electric furnace that uses electromagnetic induction to heat and melt conductive materials, such as metals. It operates at medium frequencies, typically ranging from 1 kHz to 10 kHz, and is widely used in industries like metal casting, forging, and heat treatment. The furnace is known for its high efficiency, fast heating and melting speeds, precise temperature control, and energy-saving capabilities. It is equipped with advanced protection systems, making it reliable and safe for various industrial applications. The use of IGBT induction furnace technology further enhances its performance by providing stable and efficient power output.
Key Points Explained:
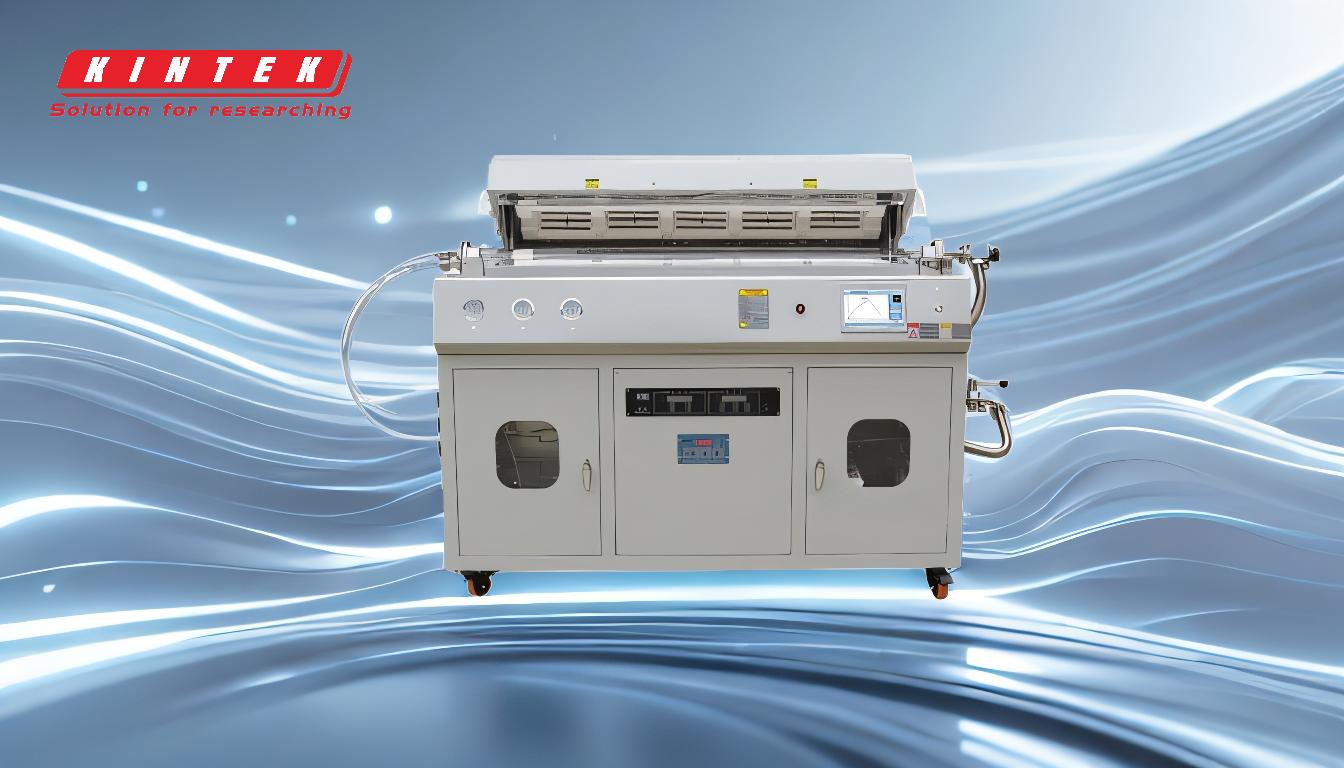
-
Working Principle of Medium Frequency Induction Furnace:
- The furnace operates on the principle of electromagnetic induction. An alternating current passes through a coil, creating a rapidly changing magnetic field.
- When a conductive material (workpiece) is placed in this field, eddy currents are induced within the material. These currents generate heat due to the material's resistance, a phenomenon known as Joule heating.
- In ferromagnetic materials, additional heat is produced through magnetic hysteresis losses. This dual heating mechanism ensures efficient and rapid heating or melting of the material.
-
Advantages of Medium Frequency Induction Furnace:
- High Efficiency: The furnace converts electrical energy into thermal energy with minimal losses, making it highly efficient.
- Fast Heating and Melting: The medium frequency range allows for rapid heating and melting, reducing processing time.
- Precise Temperature Control: Operators can easily control the furnace temperature, ensuring consistent results and high-quality output.
- Energy Saving: The furnace consumes less power compared to traditional heating methods, offering significant energy savings.
- Compact Design: Its small size and lightweight construction make it easy to install and operate in various industrial settings.
- Environmental Benefits: The furnace produces minimal pollution and reduces the burning loss of alloy elements, making it environmentally friendly.
-
Applications in Industry:
- Metal Casting: The furnace is ideal for melting metals like steel, iron, and aluminum, ensuring precise control over the composition and temperature of the molten metal.
- Forging: It is used to heat metals to the required temperature for forging processes, improving material properties and reducing defects.
- Heat Treatment: The furnace is employed in processes like annealing, hardening, and tempering, where precise temperature control is critical.
- Versatility: It can melt a wide range of materials, including non-ferrous metals and alloys, making it suitable for diverse industrial applications.
-
Protection and Safety Features:
- The furnace is equipped with comprehensive protection systems, including over-current, over-voltage, current-limiting, pressure-limiting, and water shortage protection.
- These features ensure reliable operation, prevent equipment damage, and enhance safety for operators.
-
Role of IGBT Technology:
- The use of IGBT induction furnace technology in medium frequency induction furnaces provides stable and efficient power output.
- IGBT (Insulated Gate Bipolar Transistor) technology improves the furnace's performance by enabling faster switching, reducing energy losses, and enhancing overall control.
-
Operational Simplicity:
- The furnace is designed for ease of use, with user-friendly controls and automation features.
- Operators can quickly learn to operate the furnace, reducing downtime and increasing productivity.
In summary, the medium frequency induction furnace is a versatile and efficient tool for heating and melting conductive materials. Its advanced technology, combined with features like precise temperature control, energy efficiency, and robust safety systems, makes it an essential piece of equipment in modern industrial processes. The integration of IGBT induction furnace technology further enhances its performance, making it a reliable choice for various applications.
Summary Table:
Aspect | Details |
---|---|
Working Principle | Uses electromagnetic induction to heat and melt conductive materials. |
Frequency Range | 1 kHz to 10 kHz. |
Advantages | High efficiency, fast heating, precise temperature control, energy-saving. |
Applications | Metal casting, forging, heat treatment, and more. |
Safety Features | Over-current, over-voltage, current-limiting, and water shortage protection. |
IGBT Technology | Enhances performance with stable and efficient power output. |
Discover how a medium frequency induction furnace can optimize your industrial processes—contact our experts today!