Chemical Vapor Deposition (CVD) is a versatile and widely used process in which a workpiece is exposed to gaseous chemicals in a vacuumed environment, leading to a chemical reaction that deposits a solid material onto the surface of the workpiece. This process is used to create coatings, films, and structures with specific properties such as wear resistance, corrosion resistance, and high-temperature protection. CVD is essential in industries like electronics, optics, and materials science, where it is used to produce semiconductors, optical fibers, and advanced composites. The process involves thermally induced chemical reactions at the surface of a heated substrate, with reagents supplied in gaseous form. CVD is particularly valued for its ability to produce high-quality, uniform coatings and complex structures that are difficult to achieve with other methods.
Key Points Explained:
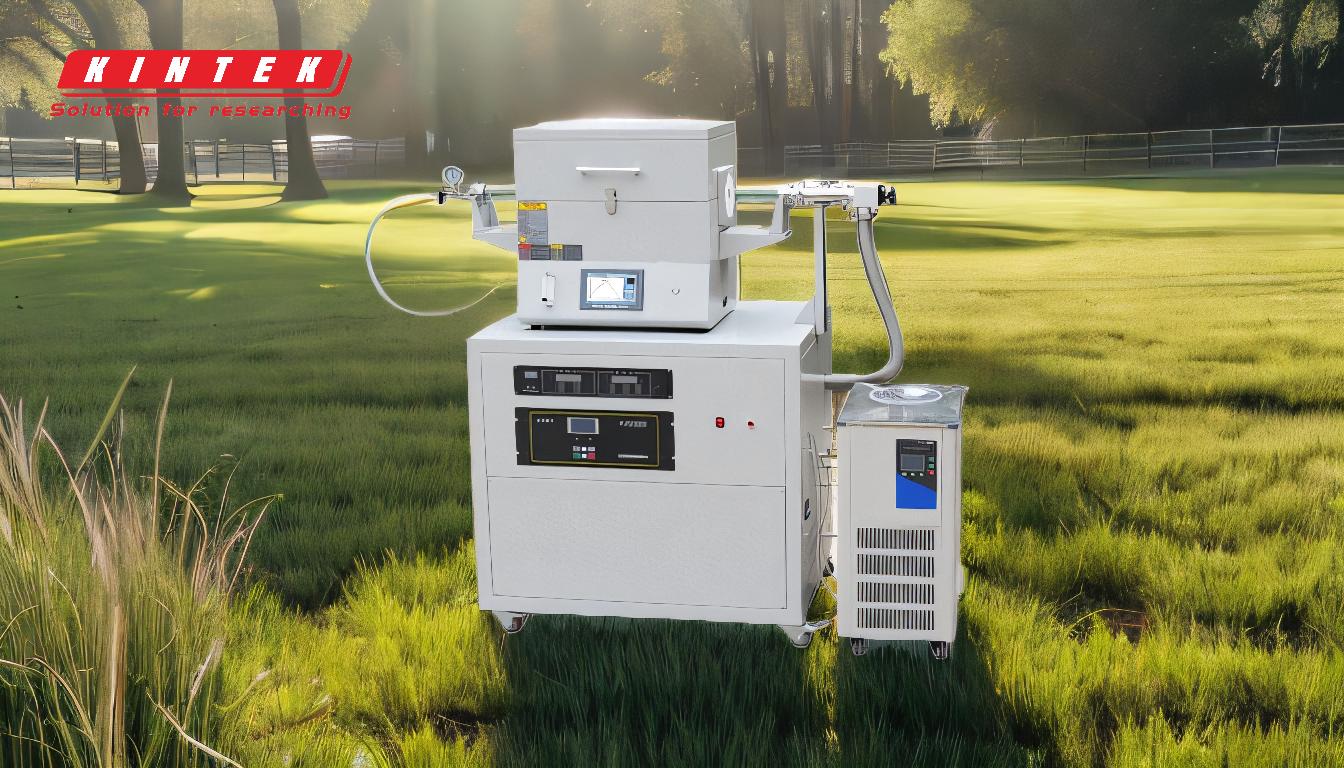
-
Definition of CVD:
- Chemical Vapor Deposition (CVD) is a process where a workpiece is exposed to gaseous chemicals in a vacuumed environment. The vacuum facilitates the deposition of these chemicals onto the workpiece's surface, where they undergo a chemical reaction and harden, forming a solid coating or film.
-
Mechanism of CVD:
- In CVD, the part to be coated is placed in a reaction chamber filled with the coating material in gaseous form. The gas reacts with the target material, leading to the deposition of a solid layer on the workpiece. This process is driven by thermally induced chemical reactions at the surface of a heated substrate.
-
Applications of CVD:
- Electronics Industry: CVD is crucial in the manufacture of semiconductors, integrated circuits, and sensors. It is used to deposit thin films that are essential for the functionality of electronic devices.
- Coatings: CVD is used to apply coatings that provide wear resistance, corrosion resistance, and high-temperature protection. These coatings are used in various industries, including aerospace and automotive.
- Optical Coatings: CVD is used to deposit optical coatings on glass and plastic, enhancing their performance in applications like telecommunications and protective eyewear.
- Structural Parts and Composites: CVD is used to produce dense structural parts and advanced composites such as carbon-carbon and silicon carbide composites, which are used in high-performance applications.
-
Advantages of CVD:
- Uniform Coatings: CVD produces high-quality, uniform coatings that are difficult to achieve with other methods.
- Complex Structures: CVD can be used to create complex structures and coatings with specific properties, such as wear resistance and high-temperature stability.
- Versatility: CVD is applicable to a wide range of materials and industries, making it a versatile and widely used process.
-
Comparison with Other Deposition Methods:
- Unlike sputtering deposition, where high-energy ions bombard the surface of a target material to remove its molecules, CVD relies on chemical reactions to deposit material onto the substrate. This difference in mechanism allows CVD to produce coatings with unique properties and structures.
-
Future Directions:
- The ongoing development of CVD techniques is expected to lead to further advancements in materials science, particularly in the fields of nanotechnology and advanced composites. The ability to produce high-quality coatings and complex structures with CVD will continue to drive innovation in various industries.
In summary, CVD is a critical process in modern manufacturing and materials science, offering unique advantages in the production of high-quality coatings and complex structures. Its applications span a wide range of industries, from electronics to aerospace, making it an indispensable tool in the development of advanced materials and technologies.
Summary Table:
Aspect | Details |
---|---|
Definition | A process where gaseous chemicals deposit solid materials on a workpiece. |
Mechanism | Thermally induced chemical reactions at a heated substrate's surface. |
Applications | Semiconductors, wear-resistant coatings, optical fibers, advanced composites. |
Advantages | Uniform coatings, complex structures, versatility across industries. |
Comparison | Differs from sputtering by relying on chemical reactions for deposition. |
Explore how CVD can enhance your manufacturing process—contact us today for expert guidance!