Metal sintering is a manufacturing process that involves compacting and forming solid materials, typically metals, by applying heat and pressure without reaching the material's melting point. This process reduces porosity and enhances the material's strength and durability by forcing atoms into tighter bonds. It is widely used in powder metallurgy and ceramic manufacturing due to its cost-effectiveness, energy efficiency, and ability to handle high-melting-point materials. The process is divided into stages, including blending fine powdered metals, compacting them into a desired shape, and sintering in a controlled atmosphere to bond the material. Metal sintering offers better control over the process, leading to consistent results and fewer imperfections compared to melting.
Key Points Explained:
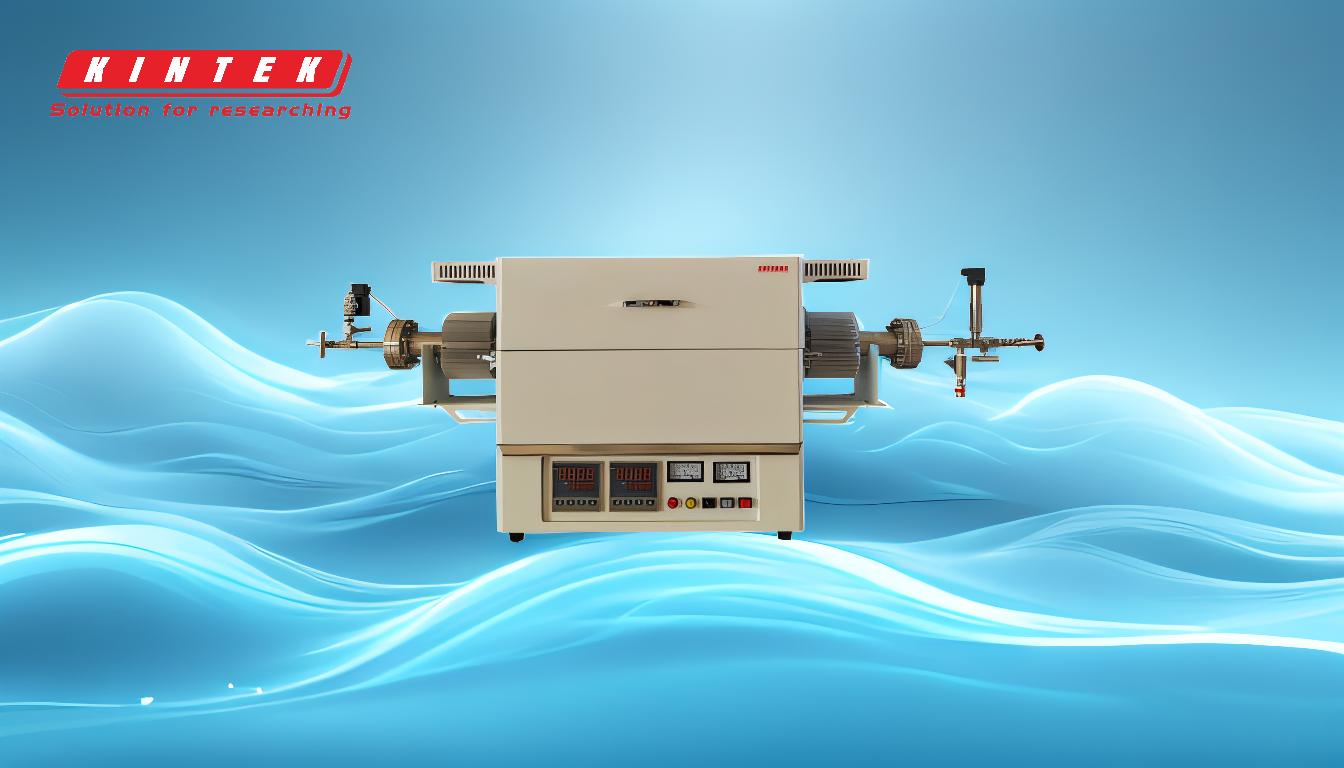
-
Definition of Metal Sintering:
- Metal sintering is a process that compacts and forms solid materials by applying heat and pressure below the material's melting point. This process reduces porous spaces between particles and forces atoms into tighter bonds, resulting in a harder, stronger, and more durable mass.
-
Stages of the Sintering Process:
- Blending: Fine powdered metals are mixed to achieve a uniform composition.
- Compaction: The blended powder is pressed into a desired shape using high pressure.
- Sintering: The compacted part is heated in a controlled atmosphere to bond the material, leading to the formation of a solid piece.
-
Mechanism of Sintering:
- During sintering, the diffusion of atoms drives the interface between powder particles to disappear. This process starts with the formation of neck connections between the powders and ends with the elimination of small pores, resulting in a dense and strong material.
-
Types of Sintering:
- Solid-State Sintering: Involves heating the material below its melting point, allowing atoms to diffuse and bond without any liquid phase.
- Liquid-Phase Sintering: Small volumes of additives form a liquid at the sintering temperature. Primary powder particles rearrange due to capillary forces, and some particles dissolve in the liquid and re-precipitate at neck areas between particles, removing pores and achieving full density.
-
Advantages of Metal Sintering:
- Cost-Effectiveness: Sintering is generally less expensive than other manufacturing processes like casting.
- Energy Efficiency: The process requires less energy since it does not involve melting the material.
- Material Versatility: Sintering can be used with high-melting-point materials such as tungsten and molybdenum.
- Consistency and Control: The process offers better control, leading to more consistent results and fewer imperfections.
-
Applications of Metal Sintering:
- Metal sintering is widely used in powder metallurgy for producing components such as gears, bearings, and automotive parts.
- It is also used in ceramic manufacturing to produce high-strength, durable ceramic components.
-
Comparison with Metal Casting:
- Unlike metal casting, which involves melting the metal and pouring it into a mold, sintering does not require the material to reach its melting point. This makes sintering suitable for materials with extremely high melting points and reduces the risk of defects associated with melting and solidification.
By understanding these key points, one can appreciate the complexity and benefits of the metal sintering process, making it a valuable technique in modern manufacturing.
Summary Table:
Aspect | Details |
---|---|
Definition | Compacting and forming metals using heat and pressure below melting point. |
Stages | Blending, Compaction, Sintering. |
Types | Solid-State Sintering, Liquid-Phase Sintering. |
Advantages | Cost-effective, energy-efficient, versatile, consistent results. |
Applications | Powder metallurgy (gears, bearings), ceramic manufacturing. |
Comparison with Casting | No melting required, fewer defects, suitable for high-melting-point metals. |
Learn how metal sintering can optimize your manufacturing process—contact our experts today!