A muffle furnace is a specialized high-temperature heating device used in laboratories and industrial settings for processes like ashing, sintering, heat treatment, and material testing. Its design features a separate combustion chamber and a gas-sealed heating chamber, ensuring that the material being heated is not contaminated by combustion by-products. Modern muffle furnaces often use electric heating elements, offering precise temperature control and consistency. The procedure for using a muffle furnace involves preparing the sample, setting the desired temperature, and monitoring the heating process to achieve the required results. Safety features, such as gas-tight doors and temperature controllers, are essential for safe operation.
Key Points Explained:
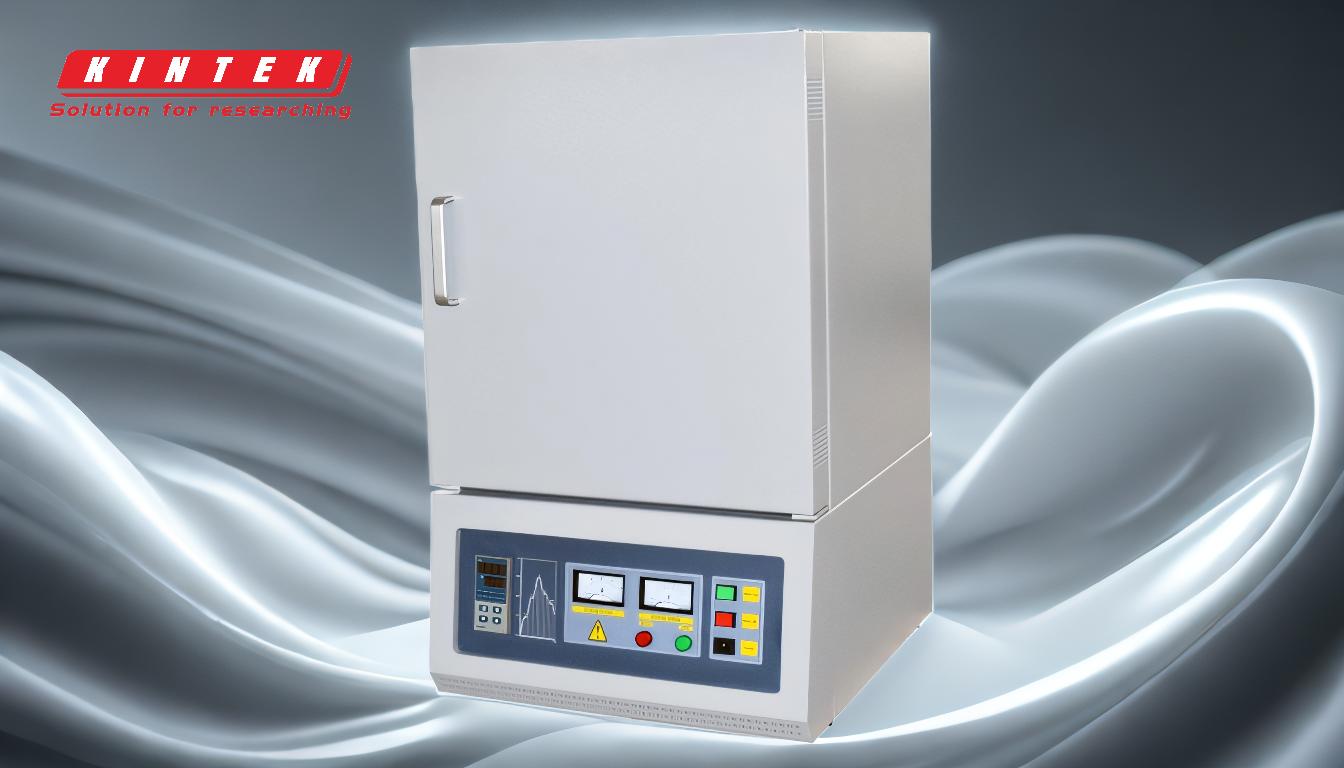
-
Principle of a Muffle Furnace:
- The muffle furnace operates on the principle of isolating the material being heated from the combustion process. This is achieved through a gas-sealed heating chamber, which prevents contamination from combustion by-products. Modern muffle furnaces often use electric heating elements, which provide cleaner and more controlled heating compared to traditional combustion-based systems. This design is particularly useful for processes requiring high temperatures and precise control, such as sintering, annealing, and ashing. For more details, refer to muffle furnace.
-
Design and Components:
- A muffle furnace typically consists of:
- Heating Chamber: A gas-sealed chamber where the material is placed for heating.
- Heating Elements: Electric or combustion-based elements that generate heat.
- Insulation: High-quality insulation materials to maintain high temperatures and improve energy efficiency.
- Temperature Control System: Advanced controllers for precise temperature regulation.
- Safety Features: Gas-tight doors, over-temperature protection, and alarms to ensure safe operation.
- A muffle furnace typically consists of:
-
Procedure for Using a Muffle Furnace:
- Sample Preparation: Ensure the sample is clean and properly prepared for heating.
- Loading the Furnace: Place the sample in the heating chamber, ensuring it is securely positioned.
- Setting the Temperature: Use the temperature control system to set the desired temperature.
- Heating Process: Start the furnace and monitor the heating process. Modern furnaces often have programmable controllers for automated heating cycles.
- Cooling and Unloading: After the heating process is complete, allow the furnace to cool before removing the sample.
-
Applications of Muffle Furnaces:
- Ashing: Used to determine the ash content of materials by burning off organic components.
- Sintering: Heating powdered materials to form a solid mass without melting.
- Heat Treatment: Processes like annealing, hardening, and tempering to alter material properties.
- Firing Ceramics: Heating ceramic materials to high temperatures to achieve desired properties.
- Melting Metals: Used in metallurgical processes to melt metals for casting or alloying.
-
Safety Considerations:
- Gas-Tight Doors: Ensure the furnace doors are properly sealed to maintain a safe environment.
- Temperature Monitoring: Use built-in temperature controllers and alarms to prevent overheating.
- Ventilation: Ensure proper ventilation to avoid the buildup of harmful gases.
- Personal Protective Equipment (PPE): Wear appropriate PPE, such as heat-resistant gloves and safety glasses, when operating the furnace.
-
Advantages of Modern Muffle Furnaces:
- Precision: Electric heating elements provide precise temperature control.
- Clean Heating: No combustion by-products, ensuring a clean heating environment.
- Versatility: Suitable for a wide range of high-temperature applications.
- Energy Efficiency: Advanced insulation and heating elements reduce energy consumption.
By understanding the principle, design, and procedure of using a muffle furnace, users can effectively utilize this equipment for various high-temperature applications while ensuring safety and precision.
Summary Table:
Aspect | Details |
---|---|
Principle | Isolates material from combustion by-products using a gas-sealed chamber. |
Key Components | Heating chamber, heating elements, insulation, temperature control system. |
Procedure | Sample prep, loading, temperature setting, heating, cooling, and unloading. |
Applications | Ashing, sintering, heat treatment, firing ceramics, melting metals. |
Safety Features | Gas-tight doors, temperature controllers, alarms, ventilation, PPE. |
Advantages | Precision, clean heating, versatility, energy efficiency. |
Discover how a muffle furnace can enhance your lab processes—contact us today for expert guidance!