Negative molding is a manufacturing process that involves creating a concave-shaped mold, which is designed to replicate the intended final shape of a product. This mold is used to produce consistent and precise copies of the desired design. The process is essential in industries where uniformity and accuracy are critical, such as in the production of consumer goods, automotive parts, and medical devices. Negative molds are typically made from durable materials like metal, silicone, or plastic, depending on the application and the material being molded.
Key Points Explained:
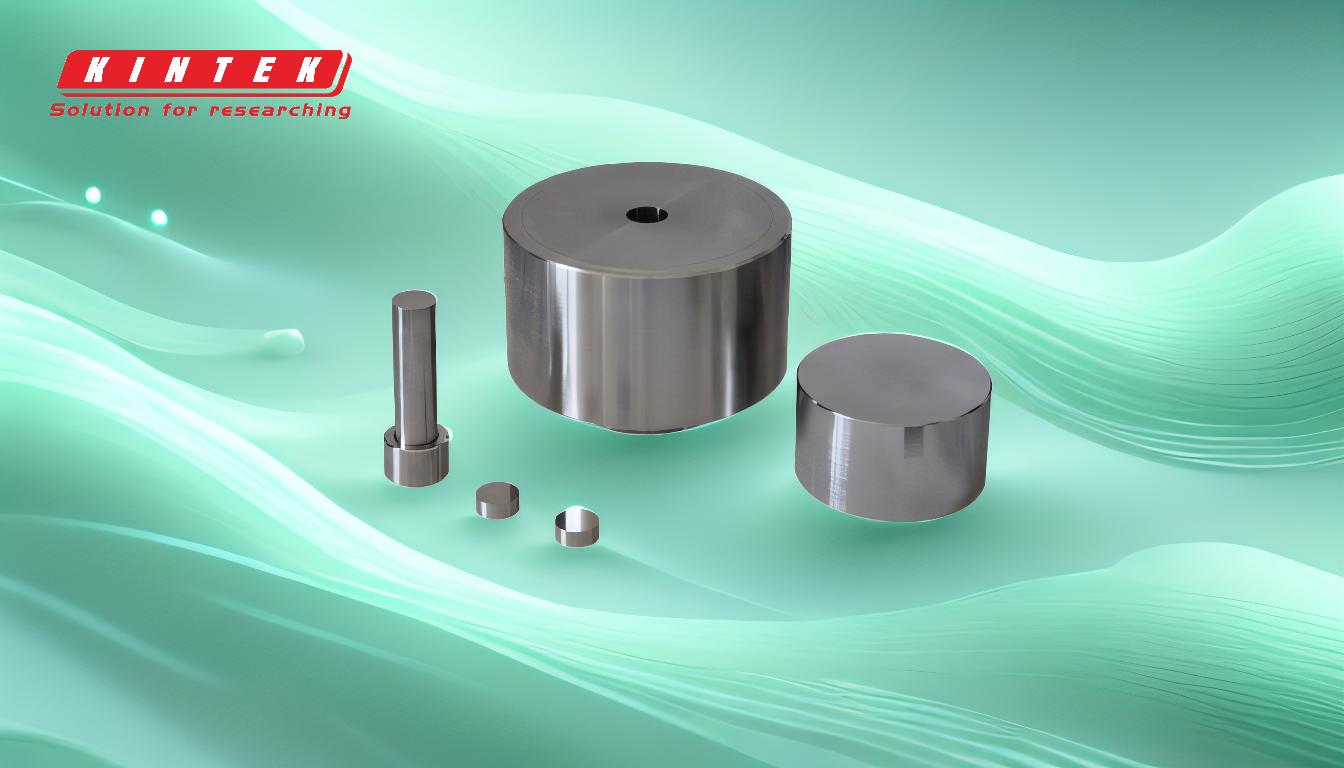
-
Definition of Negative Molding:
- Negative molding refers to the creation of a concave-shaped mold that mirrors the final shape of the product to be manufactured.
- The mold is designed to ensure that each copy produced is consistent with the original design, maintaining uniformity across multiple units.
-
Purpose of Negative Molds:
- The primary purpose of a negative mold is to reproduce identical copies of a product with high precision.
- It is widely used in industries where consistency and accuracy are paramount, such as in the production of plastic components, automotive parts, and medical devices.
-
Design and Shape:
- Negative molds are concave in shape, meaning they have an inward curve that matches the outer surface of the final product.
- The design of the mold is based on the exact specifications of the product, ensuring that the molded item matches the intended dimensions and features.
-
Materials Used for Negative Molds:
- The choice of material for a negative mold depends on the application and the material being molded.
- Common materials include:
- Metal: Used for high-temperature applications and long-lasting durability.
- Silicone: Ideal for flexible molds and intricate designs.
- Plastic: Suitable for cost-effective and lightweight molds.
-
Applications of Negative Molding:
- Negative molding is used in various industries, including:
- Consumer Goods: For producing items like toys, containers, and household products.
- Automotive: For creating parts like dashboards, bumpers, and interior components.
- Medical Devices: For manufacturing precise and sterile components like syringes and implants.
- Negative molding is used in various industries, including:
-
Advantages of Negative Molding:
- Consistency: Ensures that each product is identical, reducing variations and defects.
- Efficiency: Allows for mass production of items with minimal manual intervention.
- Precision: Captures intricate details and complex shapes with high accuracy.
-
Considerations for Purchasing Negative Molds:
- When purchasing negative molds, consider:
- Material Compatibility: Ensure the mold material is suitable for the product material.
- Durability: Choose a mold material that can withstand the production process and expected usage.
- Cost: Balance the initial investment with the expected lifespan and production volume.
- Design Complexity: Ensure the mold can accurately replicate the desired design features.
- When purchasing negative molds, consider:
By understanding the principles and applications of negative molding, manufacturers can make informed decisions about selecting and using molds to achieve high-quality and consistent production outcomes.
Summary Table:
Aspect | Details |
---|---|
Definition | Creation of concave-shaped molds to replicate final product shapes. |
Purpose | Reproduce identical copies with high precision. |
Design | Concave shape matching the outer surface of the final product. |
Materials | Metal, silicone, or plastic, depending on application. |
Applications | Consumer goods, automotive parts, medical devices. |
Advantages | Consistency, efficiency, and precision in production. |
Purchasing Considerations | Material compatibility, durability, cost, and design complexity. |
Ready to enhance your production process with negative molding? Contact us today to get started!