Dry ashing is a common sample preparation technique used in analytical chemistry to remove organic material from a sample by heating it at high temperatures in the presence of oxygen. While it is effective for many applications, one significant disadvantage of dry ashing is the potential loss of volatile elements or compounds during the high-temperature process. This loss can lead to inaccurate results, especially when analyzing samples that contain elements or compounds with low boiling points. Additionally, dry ashing can be time-consuming and may require specialized equipment, which can increase costs and complexity in the laboratory.
Key Points Explained:
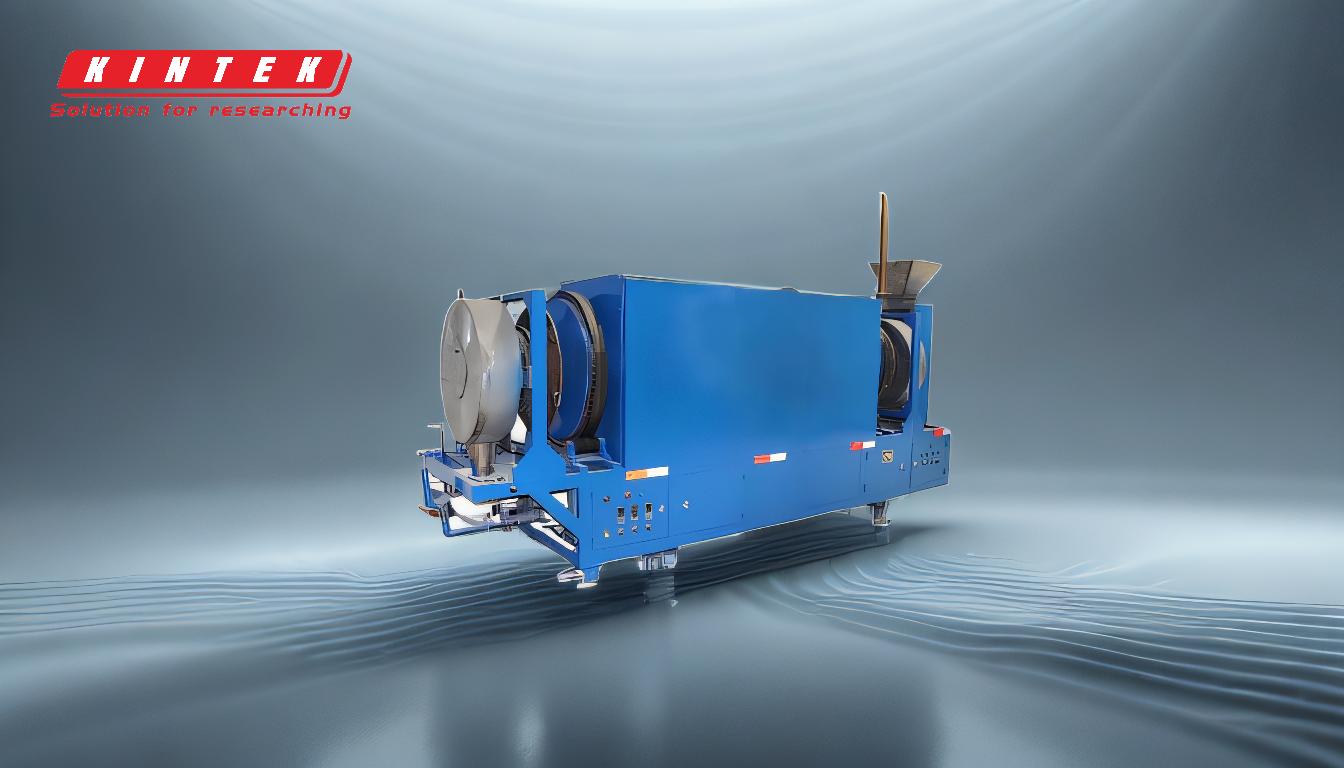
-
Loss of Volatile Elements or Compounds:
- Dry ashing involves heating samples to high temperatures (typically 500–600°C) in a muffle furnace to oxidize organic matter.
- During this process, volatile elements or compounds, such as mercury, arsenic, or certain organic compounds, may evaporate or decompose, leading to their loss from the sample.
- This loss can result in inaccurate analytical results, particularly when quantifying trace elements or volatile organic compounds.
-
Impact on Analytical Accuracy:
- The loss of volatile components can skew the results of subsequent analyses, such as atomic absorption spectroscopy (AAS) or inductively coupled plasma mass spectrometry (ICP-MS).
- For example, if a sample contains trace amounts of mercury, dry ashing may cause the mercury to volatilize, leading to an underestimation of its concentration in the sample.
-
Time-Consuming Process:
- Dry ashing typically requires several hours to complete, depending on the sample type and the temperature used.
- This prolonged heating process can delay the overall analysis, making it less suitable for high-throughput laboratories or time-sensitive projects.
-
Specialized Equipment Requirements:
- Dry ashing requires a muffle furnace capable of maintaining high temperatures for extended periods.
- The need for such specialized equipment can increase the cost and complexity of the laboratory setup, particularly for smaller labs with limited budgets.
-
Alternative Methods:
- To mitigate the disadvantages of dry ashing, alternative sample preparation methods, such as wet ashing or microwave digestion, can be used.
- Wet ashing involves using strong acids to oxidize organic matter at lower temperatures, reducing the risk of losing volatile elements.
- Microwave digestion uses microwave energy to rapidly heat samples in a closed vessel, minimizing the loss of volatile components and reducing processing time.
In summary, while dry ashing is a widely used technique for sample preparation, its primary disadvantage lies in the potential loss of volatile elements or compounds, which can compromise the accuracy of analytical results. Additionally, the method can be time-consuming and may require specialized equipment, making it less suitable for certain applications or laboratories. Alternative methods, such as wet ashing or microwave digestion, can address these limitations and provide more reliable results in specific scenarios.
Summary Table:
Disadvantage | Impact |
---|---|
Loss of volatile elements or compounds | Inaccurate results, especially for trace elements and volatile compounds. |
Time-consuming process | Delays analysis, unsuitable for high-throughput labs. |
Specialized equipment requirements | Increases costs and complexity, especially for smaller labs. |
Alternative methods (e.g., wet ashing) | Reduce loss of volatile elements and save time. |
Struggling with dry ashing limitations? Discover better solutions—contact our experts today!