Thin film deposition is a critical process in various industries, particularly in semiconductor manufacturing, where precision and control are paramount. Among the numerous methods available, Atomic Layer Deposition (ALD) stands out as a technique for depositing extremely controlled thin films. ALD offers unparalleled precision, allowing for the deposition of films at the atomic level, with exceptional uniformity and conformality. This method is particularly advantageous for applications requiring ultra-thin, high-quality films, such as in microelectronics, optics, and nanotechnology. Below, we explore the key aspects of ALD, its advantages, and why it is considered one of the most controlled methods for thin film deposition.
Key Points Explained:
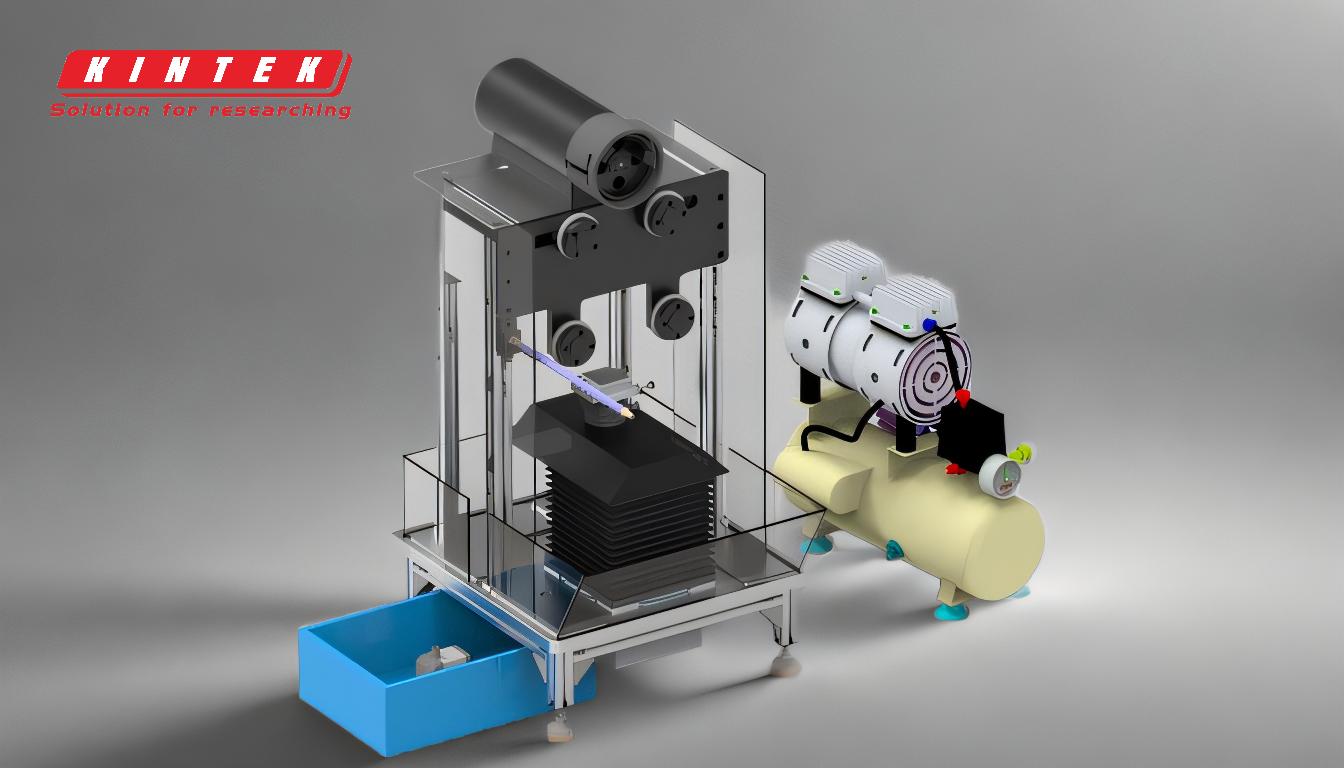
-
What is Atomic Layer Deposition (ALD)?
- ALD is a chemical vapor deposition (CVD) technique that deposits thin films one atomic layer at a time.
- It relies on sequential, self-limiting surface reactions between gaseous precursors and the substrate.
- Each reaction cycle deposits a single atomic layer, ensuring precise control over film thickness and composition.
-
How Does ALD Work?
-
Step 1: Precursor Exposure
A gaseous precursor is introduced into the reaction chamber, where it chemisorbs onto the substrate surface. -
Step 2: Purging
Excess precursor and byproducts are removed from the chamber using an inert gas purge. -
Step 3: Reactant Exposure
A second reactant is introduced, which reacts with the chemisorbed precursor to form a single atomic layer. -
Step 4: Purging
The chamber is purged again to remove any remaining reactants and byproducts. - This cycle is repeated to build up the desired film thickness, with each cycle adding a single atomic layer.
-
Step 1: Precursor Exposure
-
Advantages of ALD for Controlled Thin Film Deposition
- Atomic-Level Precision: ALD allows for precise control over film thickness, often down to the sub-nanometer scale.
- Uniformity and Conformality: Films deposited by ALD are highly uniform and conformal, even on complex 3D structures.
- Low Defect Density: The self-limiting nature of ALD reactions minimizes defects and ensures high-quality films.
- Material Versatility: ALD can deposit a wide range of materials, including oxides, nitrides, metals, and polymers.
- Scalability: ALD is compatible with industrial-scale manufacturing processes.
-
Applications of ALD
- Semiconductor Manufacturing: ALD is widely used for depositing high-k dielectrics, gate oxides, and diffusion barriers in advanced semiconductor devices.
- Optics and Photonics: ALD is used to create anti-reflective coatings, optical filters, and waveguides.
- Energy Storage: ALD is employed in the fabrication of thin-film batteries, supercapacitors, and fuel cells.
- Nanotechnology: ALD is essential for creating nanostructured materials and devices with precise dimensions.
-
Comparison with Other Thin Film Deposition Methods
- Chemical Vapor Deposition (CVD): While CVD is also precise, it lacks the atomic-level control and conformality of ALD.
- Physical Vapor Deposition (PVD): PVD methods like sputtering and evaporation are less precise and struggle with conformality on complex structures.
- Spin Coating and Dip Coating: These methods are simpler but lack the precision and uniformity of ALD.
-
Challenges and Considerations
- Slow Deposition Rate: ALD is a relatively slow process due to its sequential nature, which may not be suitable for high-throughput applications.
- Cost: ALD equipment and precursors can be expensive, making it less accessible for some applications.
- Precursor Selection: The choice of precursors is critical, as they must be highly reactive and volatile for effective ALD.
-
Future Trends in ALD
- Area-Selective ALD: Developing techniques to deposit films only on specific areas of a substrate.
- Low-Temperature ALD: Expanding ALD capabilities to temperature-sensitive substrates.
- Hybrid ALD-CVD Processes: Combining ALD with other deposition methods to enhance efficiency and versatility.
In summary, Atomic Layer Deposition (ALD) is a highly controlled method for depositing thin films, offering atomic-level precision, uniformity, and conformality. While it has some limitations, such as slower deposition rates and higher costs, its advantages make it indispensable for applications requiring ultra-thin, high-quality films. As technology advances, ALD is expected to play an increasingly important role in fields ranging from semiconductors to energy storage and nanotechnology.
Summary Table:
Aspect | Details |
---|---|
Definition | ALD is a chemical vapor deposition technique for depositing thin films one atomic layer at a time. |
How It Works | Sequential steps: precursor exposure, purging, reactant exposure, and purging. |
Advantages | Atomic-level precision, uniformity, low defect density, material versatility, scalability. |
Applications | Semiconductor manufacturing, optics, energy storage, nanotechnology. |
Challenges | Slow deposition rate, high costs, precursor selection. |
Future Trends | Area-selective ALD, low-temperature ALD, hybrid ALD-CVD processes. |
Want to learn more about how ALD can benefit your applications? Contact our experts today!