Physical vapor deposition (PVD) is a sophisticated coating process that involves the physical transformation of a material into a vapor, which is then deposited onto a substrate to form a thin film or coating. This process is widely used in industries such as semiconductors, optics, and tool manufacturing due to its ability to produce high-quality, durable coatings. PVD systems utilize various technologies, including sputter deposition, arc vapor deposition, and plasma-assisted methods, to achieve precise and controlled deposition. The process is conducted in a vacuum chamber, ensuring a clean and controlled environment for the deposition of materials. Key components of a PVD system include the deposition chamber, thermal management system, and power sources, which work together to ensure the proper formation and adhesion of the coating.
Key Points Explained:
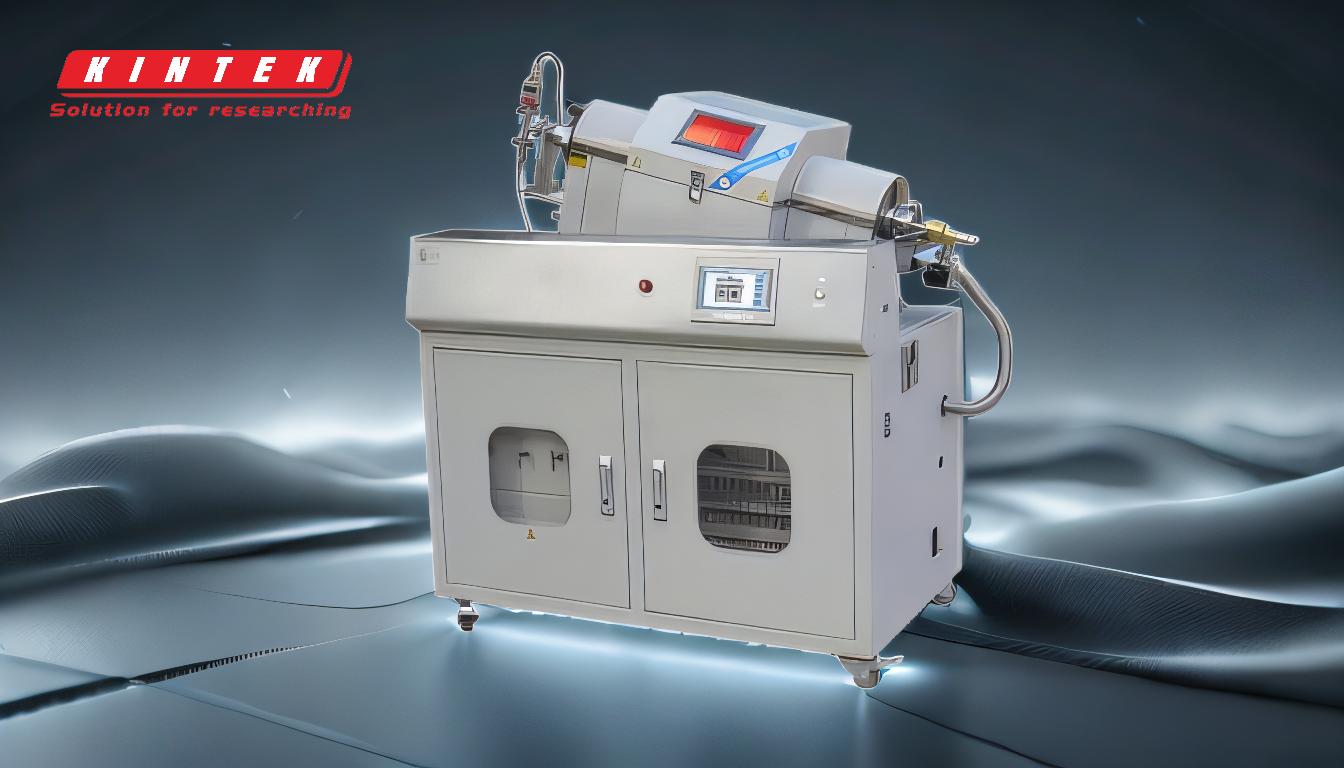
-
Definition and Process of PVD:
- Physical vapor deposition (PVD) is a process where atoms are removed from a source material through physical means, such as sputtering or evaporation, and then deposited onto a substrate to form a thin film or coating.
- The process typically involves the use of a vacuum chamber to create a controlled environment, which helps in achieving high-quality coatings with excellent adhesion and uniformity.
-
Types of PVD Technologies:
- Sputter Deposition: This involves bombarding a target material with high-energy ions, causing atoms to be ejected and deposited onto a substrate. Sputter deposition is widely used due to its ability to deposit a wide range of materials, including metals, alloys, and ceramics.
- Arc Vapor Deposition: In this method, a high-current electric arc is used to vaporize the source material, which is then deposited onto the substrate. This technique is particularly useful for depositing hard coatings, such as titanium nitride (TiN), which are commonly used in cutting tools.
- Plasma-Assisted PVD (PAPVD): This variant of PVD uses plasma to enhance the deposition process. PAPVD can be further divided into different power source technologies, such as direct current (DC) diode, radio-frequency (RF), and pulsed plasma. These technologies allow for better control over the deposition process and can improve the properties of the deposited films.
-
Components of a PVD System:
- Deposition Chamber: The chamber is where the actual deposition takes place. It is designed to maintain a high vacuum and specific temperature conditions, which are crucial for the proper formation of the coating.
- Thermal Management System: This system regulates the temperature within the deposition chamber, ensuring that the substrate and source material are maintained at the correct temperatures throughout the process. Proper thermal management is essential for achieving consistent and high-quality coatings.
- Power Sources: Different power sources, such as DC, RF, and pulsed plasma, are used to generate the energy needed to vaporize the source material and create the plasma required for deposition.
-
Applications of PVD:
- Semiconductors: PVD is used to deposit thin films of metals and dielectrics onto semiconductor wafers, which are essential for the fabrication of integrated circuits.
- Optics: PVD coatings are applied to optical components, such as lenses and mirrors, to enhance their performance by reducing reflections and increasing durability.
- Tool Manufacturing: PVD is widely used to coat cutting tools with hard, wear-resistant materials, such as titanium nitride (TiN), which significantly extends the life of the tools.
-
Advantages of PVD:
- High-Quality Coatings: PVD produces coatings with excellent adhesion, uniformity, and durability, making them suitable for a wide range of applications.
- Environmentally Friendly: PVD is a clean process that does not involve the use of hazardous chemicals, making it more environmentally friendly compared to other coating methods.
- Versatility: PVD can be used to deposit a wide variety of materials, including metals, alloys, ceramics, and even some polymers, making it a versatile coating technology.
In summary, physical vapor deposition (PVD) is a highly advanced and versatile coating technology that plays a crucial role in various industries. By understanding the different types of PVD technologies, the components of a PVD system, and the applications of PVD, one can appreciate the complexity and importance of this process in modern manufacturing and technology.
Summary Table:
Aspect | Details |
---|---|
Definition | Coating process transforming materials into vapor for thin film deposition. |
Technologies | Sputter deposition, arc vapor deposition, plasma-assisted PVD. |
Key Components | Deposition chamber, thermal management system, power sources. |
Applications | Semiconductors, optics, tool manufacturing. |
Advantages | High-quality, durable, environmentally friendly, versatile coatings. |
Discover how PVD systems can elevate your manufacturing process—contact our experts today!