Physical Vapor Deposition (PVD) is a sophisticated coating process used to deposit thin films of material onto a substrate. It involves converting a solid target material into a vapor phase, which then condenses onto the substrate to form a durable, high-performance coating. PVD is widely used in industries such as electronics, optics, and aerospace due to its ability to produce coatings with excellent adhesion, corrosion resistance, and thermal stability. The process is carried out in a vacuum chamber and utilizes methods like sputtering, evaporation, and thermal treatment to achieve precise and uniform coatings. PVD is particularly valued for its ability to handle materials with high melting points and create nanoscale thin films.
Key Points Explained:
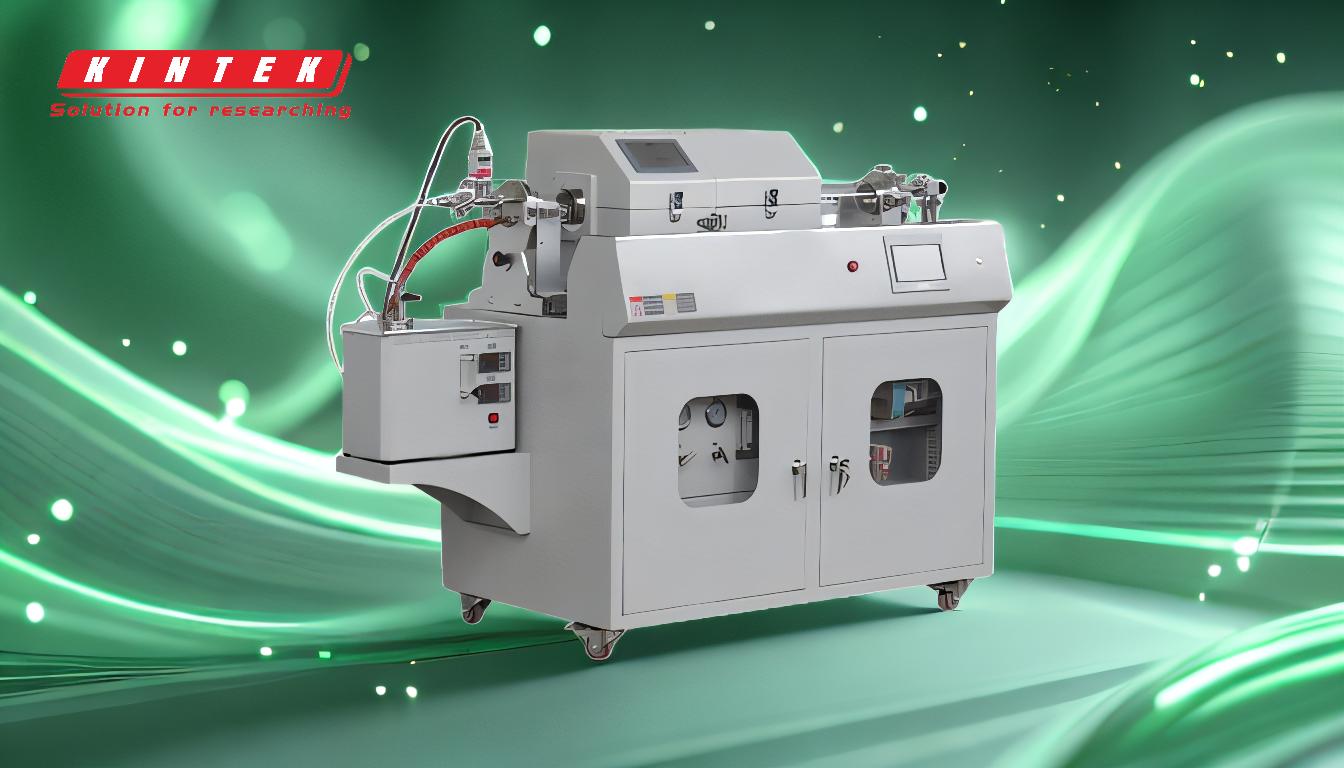
-
Definition and Purpose of PVD:
- PVD is a process that transforms a solid material into a vapor phase, which then condenses onto a substrate to form a thin film.
- The primary goal is to create coatings that enhance the properties of the substrate, such as improving durability, corrosion resistance, and thermal stability.
-
Key Steps in the PVD Process:
- Vaporization: The solid target material is converted into a vapor phase using methods like thermal evaporation or sputtering.
- Transport: The vaporized material travels through a reaction chamber in a vacuum environment.
- Condensation: The vapor condenses onto the substrate, forming a thin, uniform coating.
-
Methods of PVD:
- Sputtering: This method involves bombarding the target material with high-energy ions, causing atoms to be ejected and deposited onto the substrate.
- Thermal Evaporation: The target material is heated until it evaporates, and the vapor then condenses onto the substrate.
- Spraying: Surface atoms are removed from the target and deposited onto the substrate, often used for specific applications requiring precise control.
-
Advantages of PVD:
- High Adhesion: PVD coatings exhibit strong adhesion to the substrate, ensuring long-lasting performance.
- Material Versatility: PVD can handle materials with high melting points, making it suitable for a wide range of applications.
- Precision and Uniformity: The process allows for the creation of nanoscale thin films with precise control over thickness and composition.
-
Applications of PVD:
- Electronics: Used to create thin films for semiconductors, solar panels, and other electronic components.
- Optics: Applied in the production of anti-reflective coatings and optical filters.
- Aerospace: Used to enhance the durability and performance of aerospace components.
- Medical Devices: Provides biocompatible coatings for implants and surgical instruments.
-
Environmental and Operational Considerations:
- Vacuum Environment: PVD is performed in a vacuum chamber to prevent contamination and ensure the purity of the coating.
- Temperature Control: The process typically operates at temperatures ranging from 50 to 600 degrees Celsius, depending on the materials and desired outcomes.
- Line-of-Sight Method: The deposition occurs in a direct line from the target to the substrate, ensuring precise and uniform coating application.
In summary, Physical Vapor Deposition is a versatile and precise method for creating high-performance thin film coatings. Its ability to handle a wide range of materials and produce coatings with excellent adhesion and durability makes it a valuable process in numerous industries. The process's reliance on vacuum conditions and precise temperature control ensures the production of high-quality, uniform coatings that meet the stringent requirements of modern applications.
Summary Table:
Aspect | Details |
---|---|
Definition | Converts solid material to vapor, condensing into a thin film on substrates. |
Key Steps | Vaporization, Transport, Condensation |
Methods | Sputtering, Thermal Evaporation, Spraying |
Advantages | High adhesion, material versatility, precision, and uniformity |
Applications | Electronics, optics, aerospace, medical devices |
Operational Factors | Vacuum environment, temperature control, line-of-sight deposition |
Ready to enhance your materials with PVD coatings? Contact us today for expert solutions!