Physical Vapor Deposition (PVD) is a widely used technique in crystal growth and thin-film deposition, where a solid material is vaporized in a vacuum environment and then deposited onto a substrate to form a thin, uniform coating. This process involves transitioning materials from their condensed phase (solid or liquid) to a vapor phase, followed by condensation onto the substrate. PVD is characterized by its ability to produce high-purity, dense, and adherent coatings, making it suitable for applications in semiconductors, optics, and protective coatings. The process typically involves methods such as sputtering, evaporation, and thermal treatment, carried out in a controlled vacuum chamber to ensure uniformity and prevent contamination.
Key Points Explained:
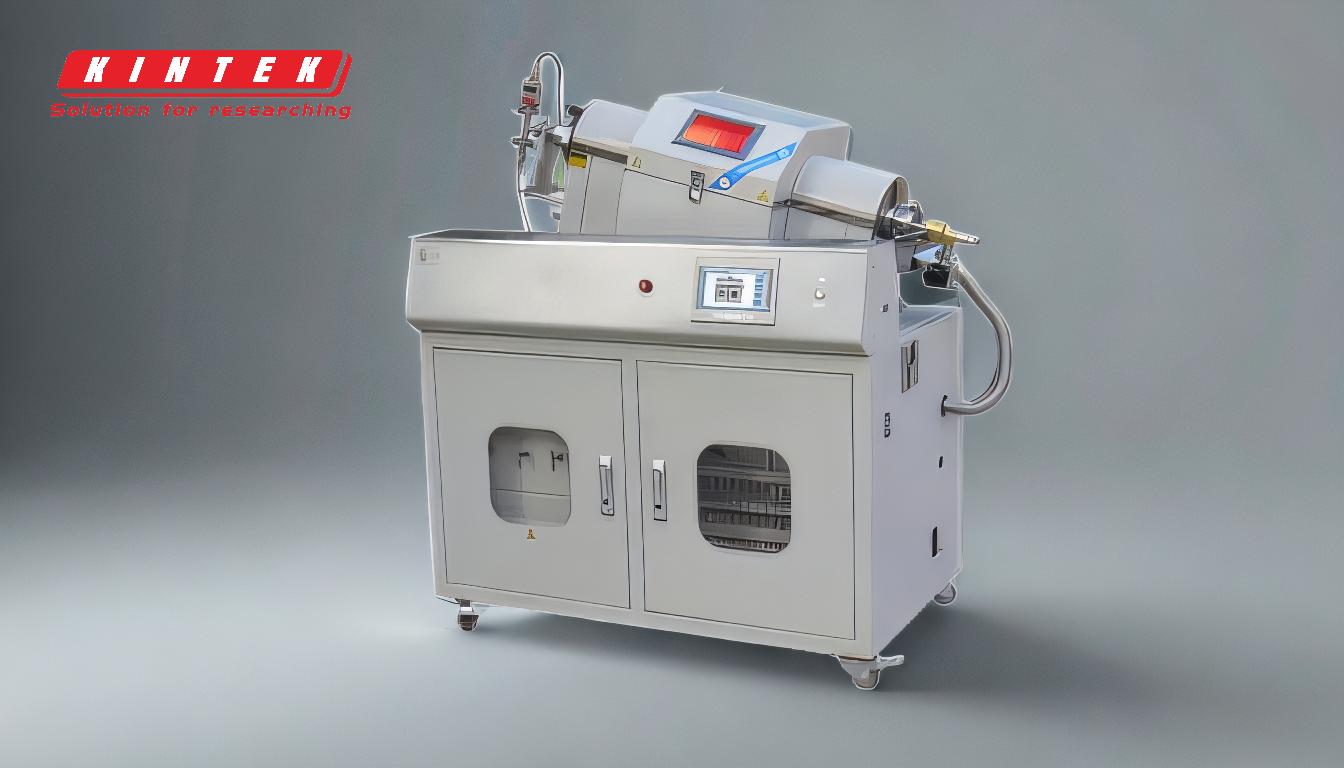
-
Basic Principles of PVD:
- PVD involves the transition of materials from a condensed phase (solid or liquid) to a vapor phase, followed by deposition onto a substrate.
- The process occurs in a vacuum chamber to maintain process integrity, avoid contamination, and ensure uniform deposition.
- Key elements include the target material (e.g., metals or semiconductors), deposition technology (e.g., sputtering, evaporation), chamber pressure, and substrate temperature.
-
Methods of PVD:
- Sputtering: A target material is bombarded with high-energy ions, causing atoms to be ejected and deposited onto the substrate. This method is widely used due to its ability to produce high-quality, uniform coatings.
- Evaporation: The target material is heated to its evaporation point using methods such as electron beams, laser beams, or resistive heating. The evaporated material then condenses onto the substrate.
- Thermal Treatment: The substrate is heated to enhance the adhesion and uniformity of the deposited film.
-
Vacuum Environment:
- The PVD process is carried out in a vacuum chamber to minimize contamination from atmospheric gases and ensure a clean deposition environment.
- The vacuum also allows for better control over the deposition rate and film properties, such as thickness and uniformity.
-
Target Materials:
- The target material is the source of the coating and can be a metal, semiconductor, or ceramic.
- Common target materials include titanium, aluminum, gold, and silicon, depending on the desired properties of the final coating.
-
Substrate Preparation:
- The substrate must be carefully cleaned and prepared to ensure good adhesion of the deposited film.
- Substrate temperature is a critical parameter, as it influences the film's microstructure, adhesion, and overall quality.
-
Applications of PVD:
- PVD is used in various industries, including semiconductors (for creating thin films in integrated circuits), optics (for anti-reflective coatings), and protective coatings (for wear and corrosion resistance).
- It is also used in the production of decorative coatings, such as those on watches and jewelry.
-
Advantages of PVD:
- High-purity coatings with excellent adhesion and uniformity.
- Ability to deposit a wide range of materials, including metals, ceramics, and composites.
- Environmentally friendly compared to some chemical deposition methods, as it typically does not involve hazardous chemicals.
-
Challenges and Considerations:
- The process requires specialized equipment and a controlled environment, which can be costly.
- Achieving uniform coatings on complex geometries can be challenging.
- The deposition rate is generally slower compared to some chemical vapor deposition (CVD) methods.
By understanding these key points, a purchaser of equipment or consumables for PVD processes can make informed decisions about the materials, methods, and conditions needed to achieve the desired coating properties for their specific application.
Summary Table:
Aspect | Details |
---|---|
Basic Principles | Transition of materials from solid/liquid to vapor, then deposition. |
Methods | Sputtering, Evaporation, Thermal Treatment. |
Vacuum Environment | Ensures clean deposition, uniform coatings, and controlled film properties. |
Target Materials | Metals (e.g., titanium, gold), semiconductors, ceramics. |
Substrate Preparation | Cleaning and temperature control for optimal adhesion. |
Applications | Semiconductors, optics, protective coatings, decorative finishes. |
Advantages | High-purity, dense, adherent, and environmentally friendly coatings. |
Challenges | High equipment costs, slower deposition rates, complex geometries. |
Ready to enhance your coating processes with PVD? Contact us today for expert guidance and solutions!