Physical Vapor Deposition (PVD) is a vacuum-based coating process used to deposit thin films of material onto a substrate. It involves converting a solid target material into a vapor phase, which then condenses onto the substrate to form a thin, durable, and high-performance coating. PVD is widely used in industries such as electronics, optics, and aerospace due to its ability to produce coatings with excellent adhesion, corrosion resistance, and thermal stability. The process can be categorized into methods like sputtering, thermal evaporation, and ion plating, depending on how the solid material is vaporized. PVD is carried out in a vacuum chamber, often at elevated temperatures, and is known for its precision and ability to handle high-melting-point materials.
Key Points Explained:
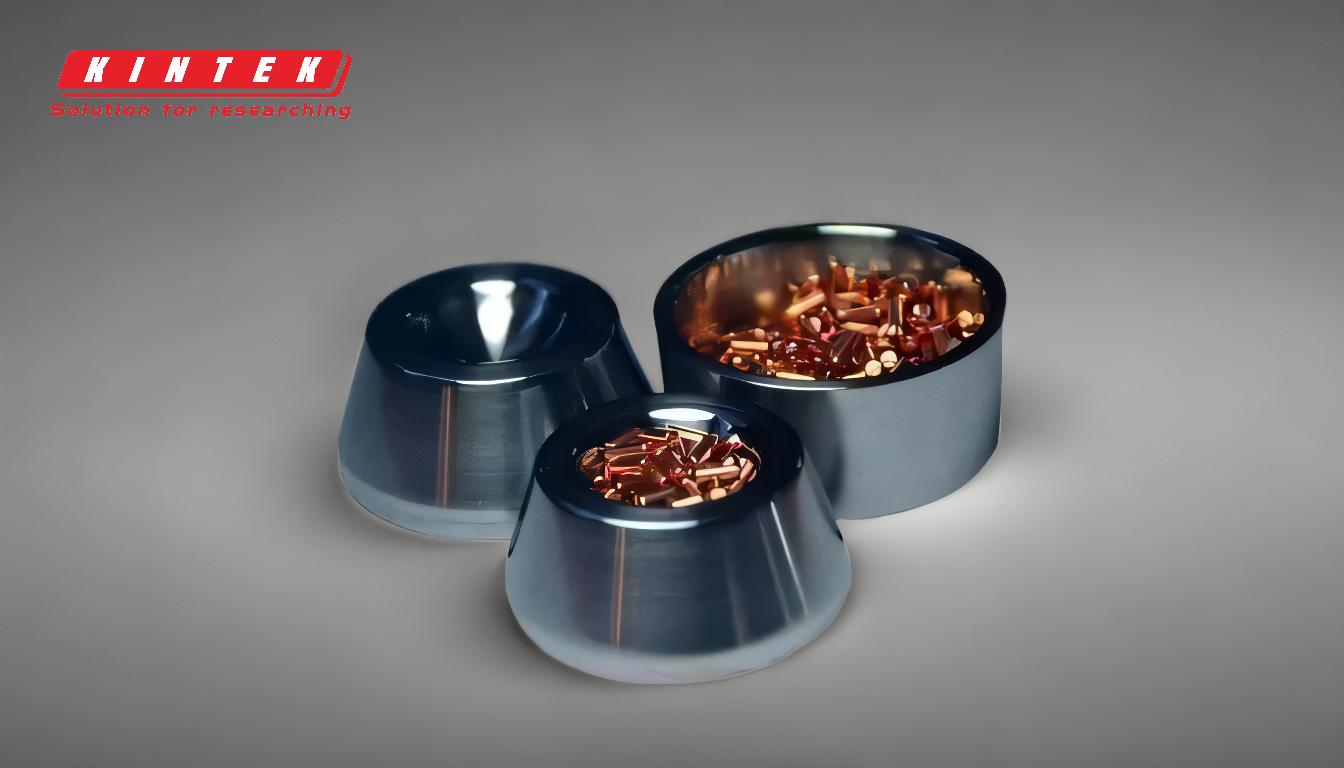
-
Definition and Purpose of PVD:
- PVD is a vacuum-based process used to deposit thin films of material onto a substrate.
- The primary purpose is to create coatings that are durable, corrosion-resistant, and capable of withstanding high temperatures.
- It is widely used in industries such as electronics, optics, and aerospace for applications requiring precise and high-performance coatings.
-
Basic Steps of the PVD Process:
- Vaporization: The solid target material is converted into a vapor phase using methods like thermal evaporation, sputtering, or laser ablation.
- Transport: The vaporized material travels through a vacuum chamber to the substrate.
- Condensation: The vapor condenses onto the substrate, forming a thin film.
- Adhesion: The deposited material adheres to the substrate, creating a durable coating.
-
Methods of PVD:
- Sputtering: Involves bombarding the target material with high-energy ions, causing atoms to be ejected and deposited onto the substrate.
- Thermal Evaporation: The target material is heated until it evaporates, and the vapor condenses onto the substrate.
- Ion Plating: Combines sputtering and evaporation with ion bombardment to enhance adhesion and film quality.
-
Equipment and Environment:
- PVD is carried out in a high-tech vacuum chamber to prevent contamination and ensure a controlled environment.
- The process often involves the use of precious metals or a combination of metals and energized gases.
- Temperatures in the chamber typically range from 50 to 600 degrees Celsius, depending on the material and application.
-
Advantages of PVD:
- High Adhesion: PVD coatings have excellent adhesion to the substrate, making them durable and long-lasting.
- Material Versatility: PVD can handle materials with high melting points, such as titanium and tungsten.
- Precision: The process allows for the deposition of very thin and uniform coatings, often at the nanoscale.
- Environmental Friendliness: PVD is a clean process that produces minimal waste and does not involve harmful chemicals.
-
Applications of PVD:
- Electronics: Used for depositing conductive and insulating layers in semiconductor devices.
- Optics: Applied in the production of anti-reflective and reflective coatings for lenses and mirrors.
- Aerospace: Used for coatings that provide wear resistance and thermal protection.
- Medical Devices: PVD coatings are used to enhance the biocompatibility and durability of implants and surgical tools.
-
Challenges and Considerations:
- Cost: PVD equipment and materials can be expensive, making the process costly for some applications.
- Complexity: The process requires precise control of parameters such as temperature, pressure, and power, which can be challenging.
- Line-of-Sight Limitation: PVD is a line-of-sight process, meaning it may not coat complex geometries uniformly.
-
Future Trends in PVD:
- Nanotechnology: Advances in PVD are enabling the deposition of nanostructured coatings with unique properties.
- Hybrid Processes: Combining PVD with other techniques like Chemical Vapor Deposition (CVD) to achieve enhanced performance.
- Sustainability: Development of more environmentally friendly PVD processes and materials to reduce the environmental impact.
Summary Table:
Aspect | Details |
---|---|
Process | Converts solid material into vapor, condensing it onto a substrate. |
Methods | Sputtering, thermal evaporation, ion plating. |
Advantages | High adhesion, material versatility, precision, environmental friendliness. |
Applications | Electronics, optics, aerospace, medical devices. |
Challenges | High cost, process complexity, line-of-sight limitations. |
Future Trends | Nanotechnology, hybrid processes, sustainability. |
Discover how PVD can enhance your applications—contact our experts today!