Plasma-activated chemical vapor deposition (PACVD) is a specialized form of chemical vapor deposition (CVD) that utilizes plasma to enhance the chemical reactions necessary for depositing thin films or coatings on substrates. Unlike traditional CVD, which relies solely on thermal energy to decompose precursor gases, PACVD introduces plasma—a partially ionized gas containing free electrons, ions, and neutral species—to activate the precursor gases at lower temperatures. This method is particularly advantageous for depositing high-quality coatings on temperature-sensitive materials and achieving precise control over film properties such as thickness, composition, and uniformity. PACVD is widely used in industries such as electronics, optics, and surface engineering to create functional coatings with enhanced performance characteristics.
Key Points Explained:
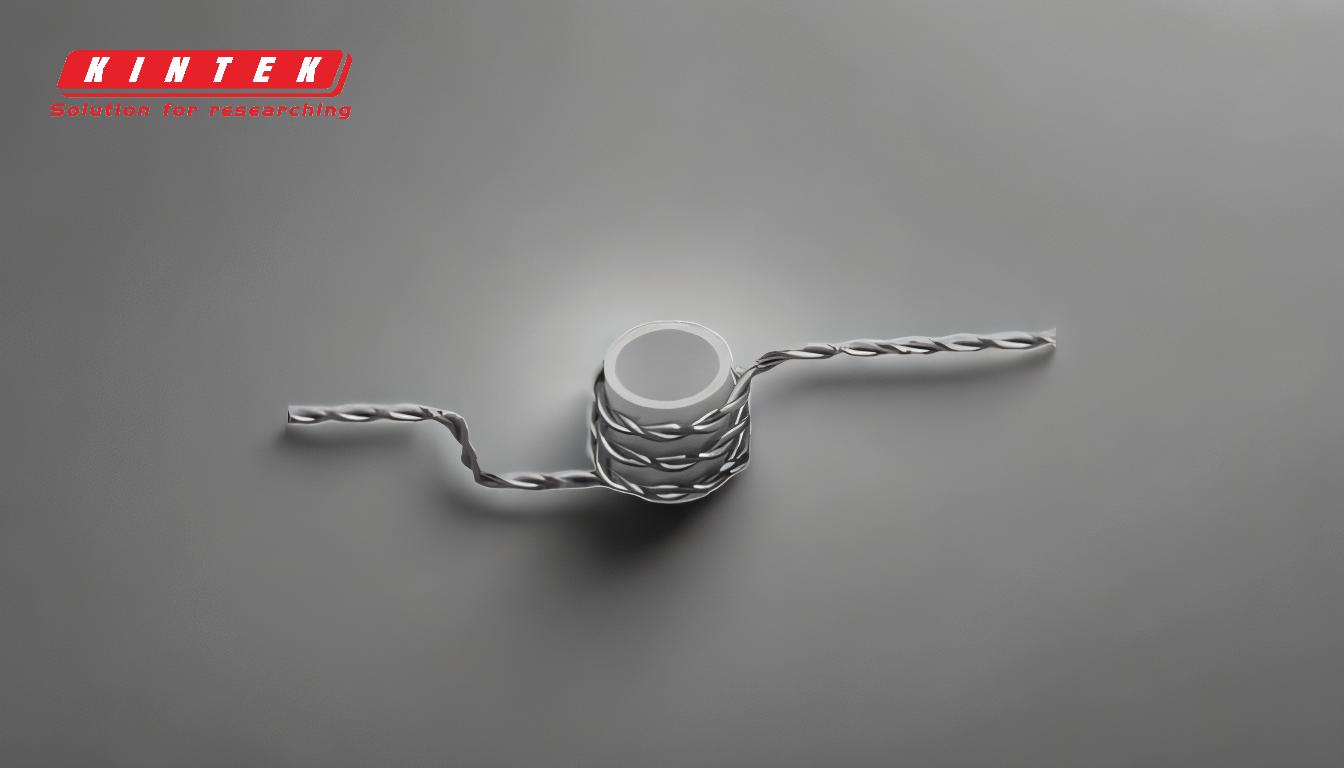
-
Definition of PACVD:
- PACVD is a variant of chemical vapor deposition (CVD) that incorporates plasma to activate precursor gases. The plasma provides energy to break down gas molecules into reactive species, enabling deposition at lower temperatures compared to traditional CVD.
-
How PACVD Works:
- Precursor Introduction: A volatile precursor gas is introduced into a vacuum chamber.
- Plasma Generation: Plasma is created using an external energy source, such as radiofrequency (RF) or microwave power, which ionizes the gas and generates reactive species.
- Surface Reaction: The activated species react or decompose on the substrate's surface, forming a thin film or coating.
- Deposition: The coating material builds up uniformly on the substrate over time.
-
Advantages of PACVD:
- Lower Temperature Operation: PACVD allows deposition at lower temperatures, making it suitable for temperature-sensitive materials like polymers or certain metals.
- Enhanced Film Quality: Plasma activation improves the reactivity of precursor gases, resulting in denser, more uniform, and higher-quality coatings.
- Versatility: PACVD can deposit a wide range of materials, including metals, ceramics, and polymers, with precise control over film properties.
-
Applications of PACVD:
- Electronics: Used to deposit thin films on semiconductors, insulating layers, and conductive traces in microelectronics.
- Optics: Applied to create anti-reflective, scratch-resistant, or protective coatings on lenses and optical components.
- Surface Engineering: Utilized to enhance the wear resistance, corrosion resistance, and hardness of cutting tools, molds, and mechanical components.
- Energy: Employed in the fabrication of thin-film solar cells and energy storage devices.
-
Comparison with Traditional CVD:
- Temperature: Traditional CVD requires high temperatures (often above 500°C), while PACVD operates at lower temperatures due to plasma activation.
- Energy Source: CVD relies on thermal energy, whereas PACVD uses plasma energy to drive chemical reactions.
- Substrate Compatibility: PACVD is more suitable for substrates that cannot withstand high temperatures, such as polymers or certain alloys.
-
Challenges and Considerations:
- Complexity: PACVD systems are more complex and require precise control over plasma parameters, such as power, pressure, and gas flow rates.
- Cost: The equipment and operational costs for PACVD are generally higher than for traditional CVD.
- Uniformity: Achieving uniform deposition over large or complex-shaped substrates can be challenging and may require advanced process optimization.
-
Future Trends:
- Hybrid Techniques: Combining PACVD with other deposition methods, such as physical vapor deposition (PVD), to achieve unique material properties.
- Sustainability: Developing eco-friendly precursor gases and reducing energy consumption in PACVD processes.
- Nanotechnology: Expanding the use of PACVD for depositing nanostructured materials with tailored properties for advanced applications.
By leveraging plasma activation, PACVD offers a powerful and versatile method for depositing high-performance coatings across a wide range of industries. Its ability to operate at lower temperatures and produce superior film quality makes it an attractive choice for modern manufacturing and surface engineering applications.
Summary Table:
Aspect | Details |
---|---|
Definition | PACVD uses plasma to activate precursor gases for thin film deposition. |
Key Advantage | Operates at lower temperatures, ideal for temperature-sensitive materials. |
Applications | Electronics, optics, surface engineering, and energy storage. |
Comparison with CVD | Lower temperature, plasma energy, and better substrate compatibility. |
Challenges | Higher complexity, cost, and uniformity challenges. |
Future Trends | Hybrid techniques, sustainability, and nanotechnology applications. |
Discover how PACVD can revolutionize your coating processes—contact our experts today!