Porosity in sintering refers to the presence of voids or pores within a material, which is a critical factor in determining the final properties of sintered products. During sintering, these pores diminish or close up, leading to densification and improved mechanical properties. The rate of pore elimination is influenced by factors such as the initial porosity of the green compact, sintering temperature, and sintering time. Higher initial porosity and uniform pore sizes accelerate pore elimination due to shorter boundary diffusion distances. In later stages, boundary diffusion and lattice diffusion from grain boundaries play significant roles in further reducing porosity. The final porosity of sintered ceramics depends on the initial porosity, sintering temperature, and duration, with pure oxide ceramics requiring longer sintering times and higher temperatures due to solid-state particle diffusion. Applying pressure can also reduce sintering time and porosity.
Key Points Explained:
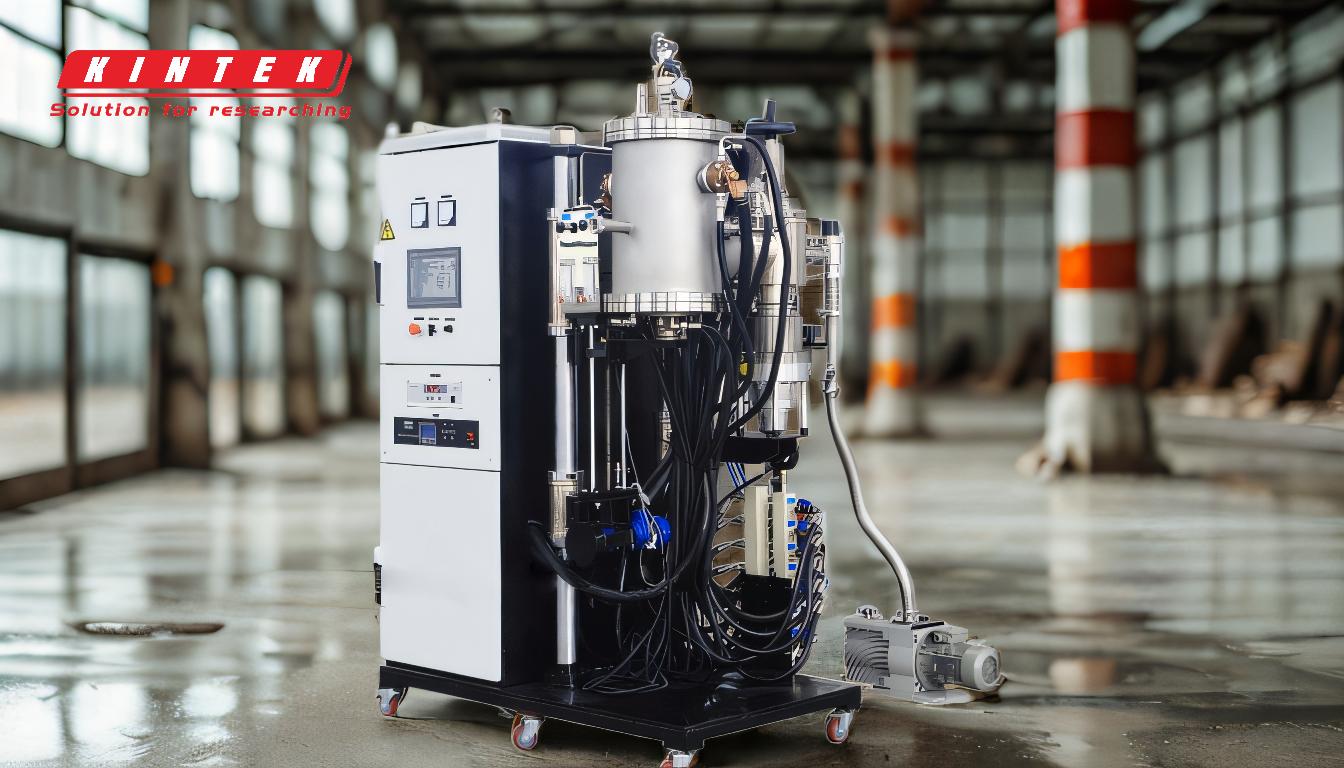
-
Definition of Porosity in Sintering:
- Porosity refers to the voids or pores present within a material. In the context of sintering, these pores are initially present in the green compact and are gradually eliminated during the sintering process.
-
Role of Porosity in Sintering:
- Porosity is a critical factor that influences the densification and mechanical properties of sintered materials. The elimination of pores leads to densification, which enhances the material's strength, hardness, and other mechanical properties.
-
Factors Influencing Porosity Elimination:
- Initial Porosity: The level of porosity in the green compact significantly affects the rate of pore elimination. Higher initial porosity can lead to faster pore elimination, especially if the pores are of uniform size.
- Sintering Temperature: Higher temperatures facilitate faster diffusion processes, which are essential for pore elimination. However, excessively high temperatures can lead to undesirable grain growth.
- Sintering Time: Longer sintering times allow for more complete pore elimination, but the relationship between time and porosity reduction is not linear and depends on other factors like temperature and material composition.
-
Mechanisms of Porosity Reduction:
- Boundary Diffusion: In the early stages of sintering, boundary diffusion is the primary mechanism for pore elimination. This process is more efficient when the pores are of uniform size and the diffusion distances are shorter.
- Lattice Diffusion: In later stages, lattice diffusion from grain boundaries becomes important. This mechanism involves the movement of atoms through the crystal lattice, contributing to further densification and pore elimination.
-
Impact of Material Composition:
- Pure Oxide Ceramics: These materials require longer sintering times and higher temperatures because particle diffusion occurs in the solid state. The absence of a liquid phase makes the diffusion process slower, leading to higher final porosity if not adequately sintered.
- Effect of Pressure: Applying pressure during sintering can significantly reduce sintering time and porosity. Pressure-assisted sintering techniques, such as hot pressing, can achieve higher densities at lower temperatures and shorter times compared to conventional sintering.
-
Final Porosity and Material Properties:
- The final porosity of sintered ceramics is a result of the interplay between initial porosity, sintering temperature, and sintering time. Lower final porosity generally leads to better mechanical properties, but the optimal porosity level depends on the intended application of the material.
-
Practical Considerations for Purchasers:
- When purchasing sintered materials, it is essential to consider the intended application and the required mechanical properties. Understanding the relationship between porosity and material performance can help in selecting the right material with the appropriate porosity level.
- For applications requiring high strength and durability, materials with lower final porosity are preferred. Conversely, for applications where thermal insulation or lightweight properties are more critical, materials with controlled porosity may be more suitable.
In summary, porosity in sintering is a complex phenomenon influenced by various factors, including initial porosity, sintering temperature, and time. Understanding these factors and their interactions is crucial for optimizing the sintering process to achieve the desired material properties.
Summary Table:
Aspect | Description |
---|---|
Definition | Voids or pores within a material, eliminated during sintering. |
Role in Sintering | Influences densification and mechanical properties like strength and hardness. |
Key Factors | Initial porosity, sintering temperature, sintering time, and material composition. |
Mechanisms | Boundary diffusion (early stages) and lattice diffusion (later stages). |
Material Impact | Pure oxide ceramics require longer sintering times and higher temperatures. |
Pressure Effect | Applying pressure reduces sintering time and porosity. |
Final Porosity | Depends on initial porosity, temperature, and time; affects material properties. |
Optimize your sintering process for superior material properties—contact our experts today!