Positive compression molding is a specialized form of compression molding used primarily when precise control over part density is required, or when working with expensive materials. It is also ideal for parts with deep draws, where the depth of the molded part exceeds its diameter. This method involves placing pre-shaped rubber stock into mold cavities, applying heat and pressure to fill the cavities, and allowing excess material (flash) to escape through designated grooves. While effective, it requires careful preparation to avoid defects caused by incorrect material placement or quantity.
Key Points Explained:
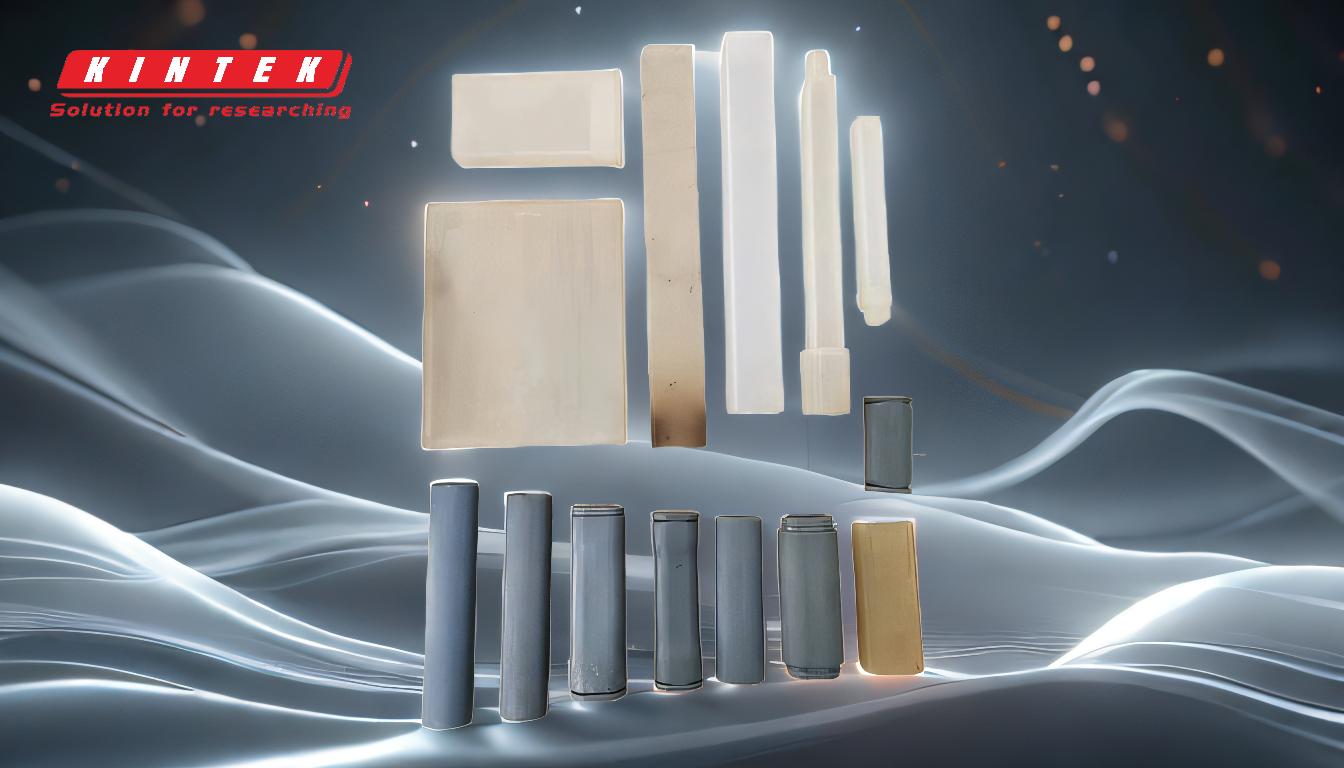
-
Definition and Purpose of Positive Compression Molding:
- Positive compression molding is a variant of compression molding used to achieve precise control over part density and material distribution.
- It is particularly useful for molding parts with deep draws, where the depth of the part exceeds its diameter.
- This method is often chosen for expensive materials to minimize waste and ensure high-quality results.
-
Process Overview:
- Pre-shaped, un-branched rubber stock is placed into each cavity of the mold.
- The mold is closed and subjected to a fixed temperature and pressure, causing the rubber to flow and fill the cavities.
- Excess material, known as mold flash, escapes through special grooves designed to handle overflow.
-
Advantages of Positive Compression Molding:
- Control Over Density: Ensures uniform density throughout the part, which is critical for high-performance applications.
- Material Efficiency: Reduces waste, especially when working with costly materials.
- Deep Draw Capability: Suitable for parts with significant depth-to-diameter ratios, which other molding methods may struggle with.
-
Challenges and Considerations:
- Material Preparation: Accurately cutting or weighing the rubber stock is crucial. Too little material can result in defects like flow lines, blisters, or unfilled cavities.
- Flash Management: Excessive material can lead to heavy flash, which is difficult to remove and may require additional finishing steps.
- Mold Design: Special grooves must be incorporated into the mold to allow for the escape of excess material without compromising the part's integrity.
-
Applications:
- Commonly used in industries where precision and material efficiency are paramount, such as aerospace, automotive, and medical device manufacturing.
- Ideal for producing complex or deep-drawn components that require consistent material properties.
-
Comparison to Other Molding Techniques:
- Unlike injection molding, which uses high-pressure injection of material into a mold, positive compression molding relies on heat and pressure to shape the material.
- It offers better control over density and material distribution compared to traditional compression molding, making it suitable for high-stakes applications.
By understanding these key points, equipment and consumable purchasers can make informed decisions about when and how to use positive compression molding, ensuring optimal results for their specific needs.
Summary Table:
Aspect | Details |
---|---|
Purpose | Achieve precise control over part density and material distribution. |
Key Advantages | Uniform density, material efficiency, and deep draw capability. |
Process | Pre-shaped rubber stock is heated and pressurized to fill mold cavities. |
Challenges | Accurate material preparation, flash management, and specialized mold design. |
Applications | Aerospace, automotive, and medical device manufacturing. |
Comparison | Better control over density compared to traditional compression molding. |
Optimize your manufacturing process with positive compression molding—contact us today to learn more!