Pressing and sintering of metals is a widely used powder metallurgy process that involves compacting metal powders into a desired shape and then heating them to bond the particles together. This process is cost-effective, allows for high precision, and is suitable for producing complex shapes. The key steps include powder blending, compaction (pressing), and sintering (heating). During compaction, the powder is pressed into a "green" part, which has initial strength but is not fully dense. Sintering then heats the part to just below its melting point, causing the particles to bond and form a solid, dense structure. This process is used in industries like automotive, aerospace, and electronics to create components with specific mechanical properties.
Key Points Explained:
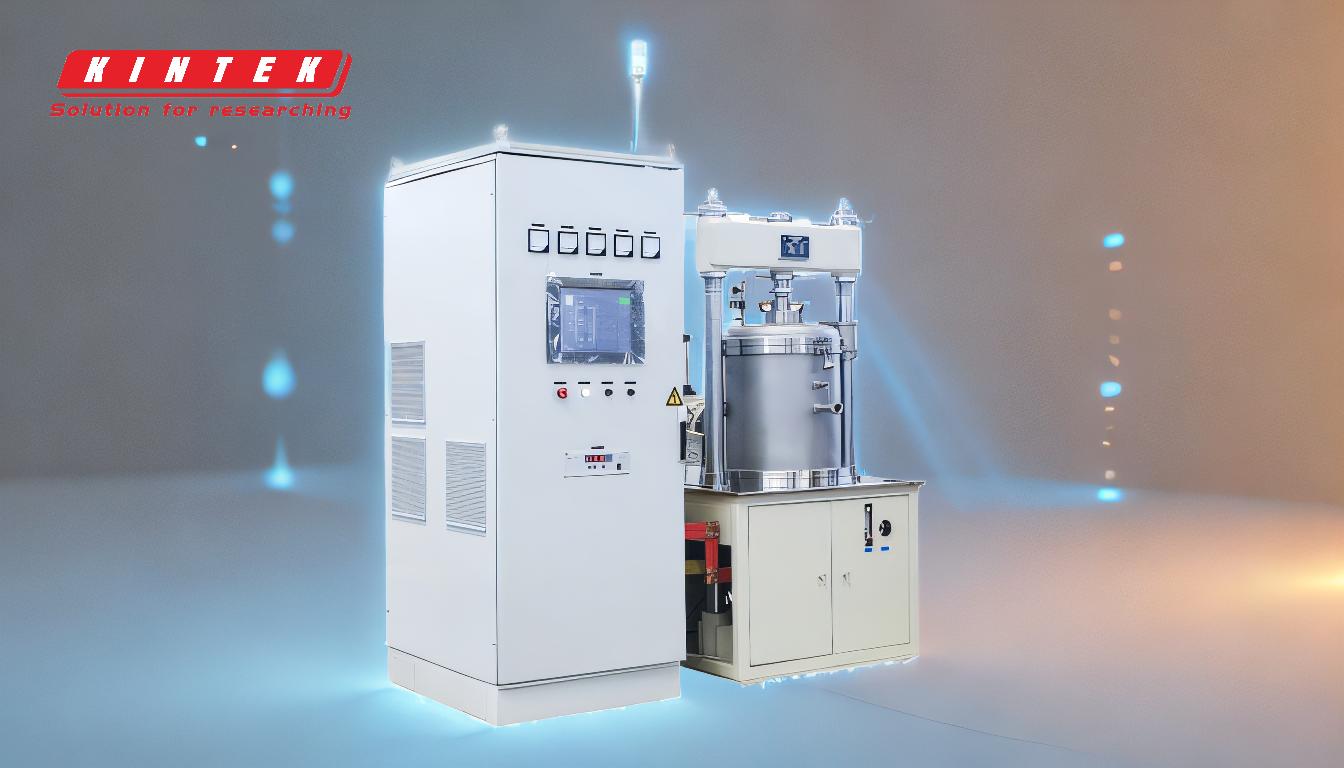
-
Powder Blending:
- The process begins with selecting and mixing metal powders, which can include pure metals like iron, nickel, or copper, or alloying elements like molybdenum.
- Additives such as lubricants are often included to improve flowability and reduce friction during compaction.
- The choice of powder composition determines the final properties of the product, such as strength, hardness, and corrosion resistance.
-
Compaction (Pressing):
- The blended powder is placed into a die and pressed at high pressure, typically at room temperature, to form a "green" part.
- Compaction gives the part its initial shape and strength, but the part remains porous and not fully dense.
- The pressure applied during compaction ensures uniformity and minimizes defects in the final product.
-
Sintering (Heating):
- The green part is transferred to a sintering furnace, where it is heated to a temperature just below the melting point of the metal.
- During sintering, the particles bond together through diffusion, reducing porosity and increasing density.
- The process often occurs in a controlled atmosphere (e.g., hydrogen, nitrogen, or vacuum) to prevent oxidation and ensure proper bonding.
- Sintering enhances the mechanical properties of the part, such as strength, hardness, and wear resistance.
-
Post-Treatment (Optional):
- After sintering, additional treatments like machining, heat treatment, or surface finishing may be applied to achieve specific properties or tolerances.
- These steps further refine the part to meet the required specifications for its intended application.
-
Applications and Advantages:
- Pressing and sintering are used to produce a wide range of components, including gears, bearings, filters, and structural parts.
- The process is highly efficient, with minimal material waste, and allows for the production of complex shapes that are difficult to achieve with traditional machining.
- It is particularly advantageous for high-volume production due to its repeatability and cost-effectiveness.
By understanding these key steps, manufacturers can optimize the pressing and sintering process to produce high-quality metal components tailored to specific industrial needs.
Summary Table:
Step | Description |
---|---|
Powder Blending | Select and mix metal powders with additives for desired properties. |
Compaction (Pressing) | Press blended powder into a die to form a porous "green" part. |
Sintering (Heating) | Heat the green part to bond particles, increasing density and strength. |
Post-Treatment | Optional steps like machining or surface finishing for final specifications. |
Applications | Used in automotive, aerospace, and electronics for high-precision components. |
Optimize your metal components with pressing and sintering—contact our experts today!