PVD (Physical Vapor Deposition) coating thickness typically ranges from 0.25 microns (μm) to 5 microns (μm), depending on the application and desired properties. This thin film coating is designed to enhance surface properties such as hardness, smoothness, corrosion resistance, and wear resistance without significantly altering the dimensions or appearance of the substrate. The thickness is carefully controlled to ensure optimal performance, with decorative applications often requiring thinner coatings (e.g., 0.30 microns) and functional applications (e.g., tools or industrial parts) requiring thicker coatings (e.g., 2 to 5 microns). PVD coatings are highly durable, resistant to wear and corrosion, and can replicate the original finish of materials with minimal effort.
Key Points Explained:
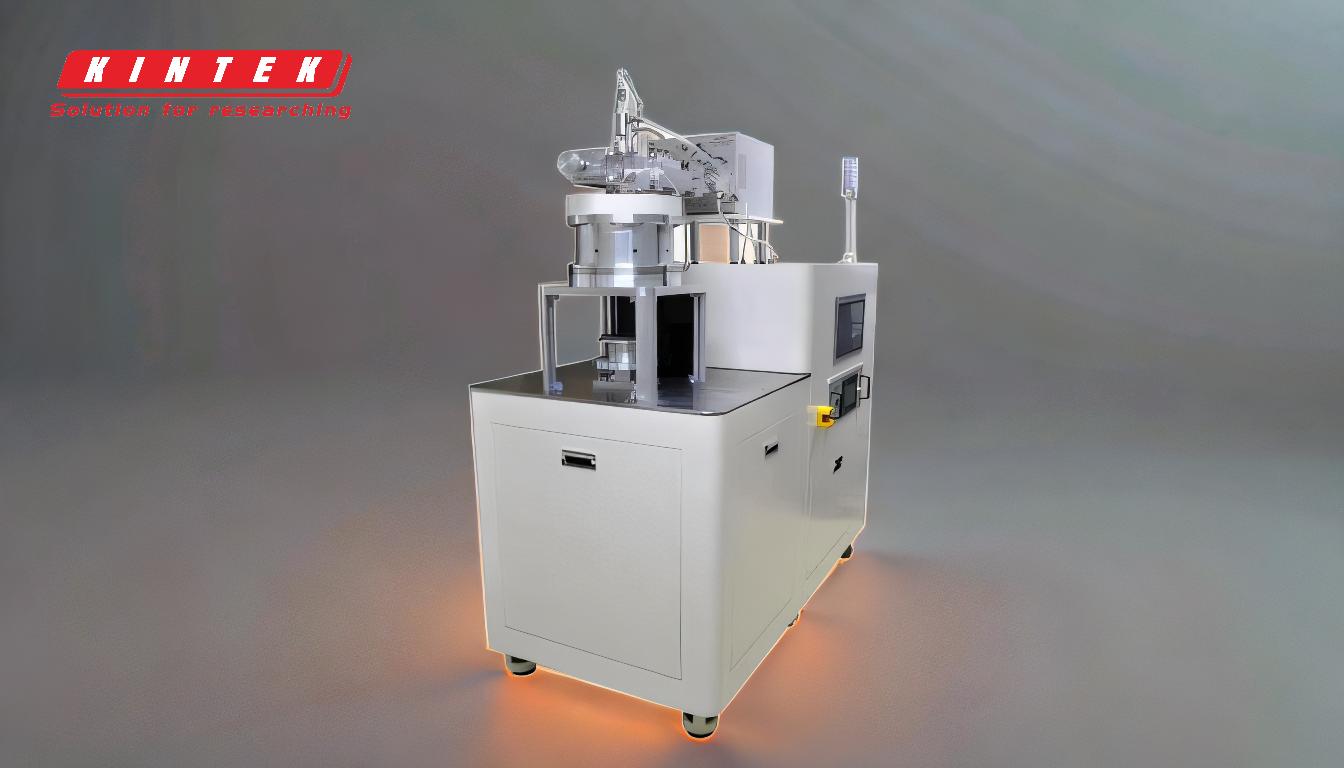
-
Typical Thickness Range of PVD Coatings:
- PVD coatings generally range from 0.25 microns to 5 microns in thickness.
- This range is chosen to balance performance enhancements (e.g., hardness, corrosion resistance) with minimal impact on the substrate's dimensions and appearance.
- For decorative purposes, coatings may be as thin as 0.30 microns, while functional applications often require thicker coatings of 2 to 5 microns.
-
Why PVD Coating Thickness is Thin:
- PVD coatings are designed to be thin to avoid altering the specifications of engineered parts.
- The thinness ensures that the coating adheres well to the substrate and maintains the part's original dimensions and tolerances.
- Despite their thinness, PVD coatings provide significant improvements in surface properties, such as hardness, wear resistance, and corrosion resistance.
-
Applications and Thickness Variations:
- Decorative Applications: For items like stainless steel sheets, the coating thickness is often around 0.30 microns to achieve a polished, metallic finish without adding bulk.
- Functional Applications: In industrial or tooling applications, thicker coatings (e.g., 2 to 5 microns) are used to enhance durability, hardness, and resistance to wear and corrosion.
- The choice of thickness depends on factors such as the type of motion, lubrication, and surface finish required for the application.
-
Benefits of Thin PVD Coatings:
- High Purity and Uniformity: PVD coatings are highly uniform and pure, ensuring consistent performance across the coated surface.
- Excellent Adhesion: The thin films adhere strongly to the substrate, reducing the risk of peeling or flaking.
- Enhanced Surface Properties: Despite their thinness, PVD coatings significantly improve hardness, abrasion resistance, and corrosion resistance.
- Aesthetic Replication: PVD coatings can replicate the original finish of materials, maintaining their appearance while adding functional benefits.
-
Comparison to Other Coating Methods:
- PVD coatings are often harder and more corrosion-resistant than coatings applied by electroplating.
- The thinness of PVD coatings allows them to be applied without the need for additional protective topcoats, simplifying the coating process and reducing costs.
- PVD coatings are also more durable and resistant to high temperatures and impacts compared to traditional coating methods.
-
Challenges with PVD Coating Thickness:
- Uniformity on Complex Shapes: PVD coatings may have difficulty achieving uniform thickness on the back and sides of tools or complex geometries due to low air pressure during the deposition process.
- Thickness Control: Precise control of coating thickness is required to ensure optimal performance, especially in functional applications where too thin or too thick a coating could compromise performance.
-
Real-World Examples of Thickness:
- For reference, 25 microns equals 0.001 inches, a red blood cell is about 8 microns in diameter, and a human hair is approximately 80 microns in diameter.
- This highlights how thin PVD coatings are, even at their maximum thickness of 5 microns.
In summary, PVD coating thickness is a critical factor in determining the performance and suitability of the coating for specific applications. The thinness of PVD coatings ensures that they enhance surface properties without compromising the substrate's dimensions or appearance, making them ideal for both decorative and functional uses.
Summary Table:
Aspect | Details |
---|---|
Typical Thickness Range | 0.25 to 5 microns |
Decorative Applications | ~0.30 microns for polished finishes |
Functional Applications | 2 to 5 microns for durability and wear resistance |
Key Benefits | Hardness, corrosion resistance, wear resistance, and aesthetic replication |
Challenges | Uniformity on complex shapes and precise thickness control |
Learn how PVD coatings can improve your product's performance—contact our experts today!